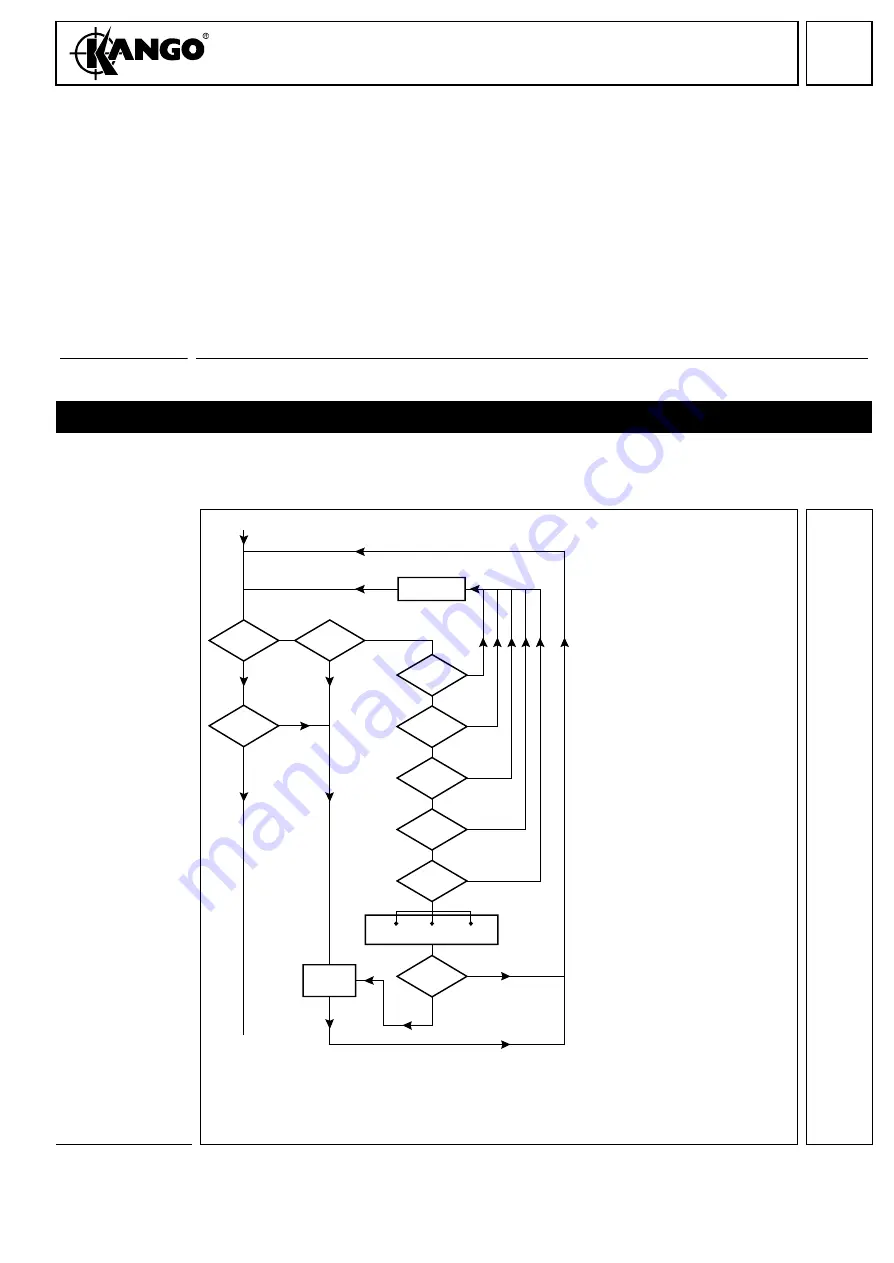
16
PAGE
Repair Instructions
K 350
WARNING
After completed assembly, the machine should be submitted to a flashover test with 4000 volts.
It is advisable to run the machine with half the rated voltage to make sure that the brushes are
inserted correctly. After 10 minutes the machine should be run with full rated voltage. The per-
formance test values should be compared with these values.
With the breaker completely assembled and with the switch “ON” apply 2000 volts initially and increase
rapidly to 4000 volts between the main casting and one of the pins of the plug on the power supply cord.
Apply test to both live and neutral pins.
WARNING
Do not touch the other pin during this test since it is live.
The full voltage of 4000 volts should be maintained without breakdown or flashover for a few seconds.
If the armature has been tested, remove the carbon brushes before carrying out the test, (thus avoiding
over-stressing the armature insulation system.) As a result, a further over-stressing of the armature in-
sulation is avoided. In this case the test voltage must be carried out between the conductive cast part
and each pin one after the other.
WARNING
If the machine is not switched on, faults could be not found and the user could suffer an elec-
tric shock. Make sure the switch is in the “On” position.
Fault finding
With the aid of the Fault Finding chart (below) the source of any malfunction may be quick-
ly identified and repaired.
REMEDY FAULT
AND RETEST
MOTOR
REVOLVES?
MACHINE
HAMMERS?
MACHINE
IDLES?
SUPPLY
OK?
PLUG FUSE
OK?
BRUSHES
OK?
CORD
OK?
SWITCH
OK?
ARMATURE FIELD
INTERNAL
WIRING
SERVICE
MECHANISM
MODULE
WAS MOTOR
BURNT OUT?
MACHINE
OK
YES
NO
NO
YES
YES
YES
YES
YES
YES
YES
YES
NO
NO
NO
NO
NO
NO
NO
Summary of Contents for K 350
Page 1: ......