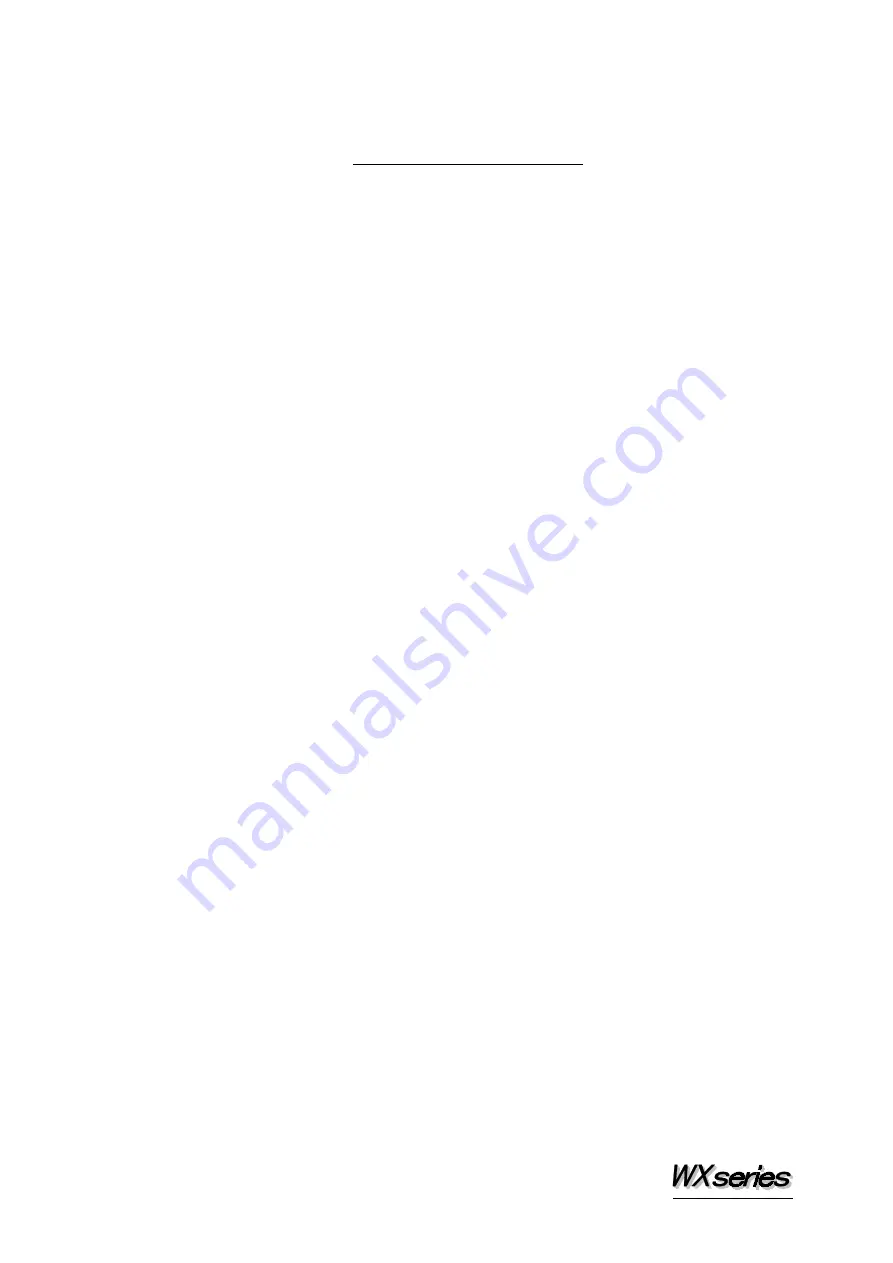
INTRODUCTION
INTRODUCTION
INTRODUCTION
INTRODUCTION
Thank you for your purchasing Kansai Special's WX Series.
Read and study this instruction manual carefully before beginning any of the
procedures and save it for later use.
1. This instruction manual describes adjustments and maintenance procedures on this
machine.
2. Before starting the machine check to make sure the pulley cover, safety cover, etc.
are secured.
3. Before adjusting, cleaning, threading the machine or replacing the needle, be sure
to turn off the power.
4. Never start the machine with no oil in the reservoir.
5. Refer to the parts list as well as this instruction manual before maintenance. If
the machine includes a thread trimmer, read and study the instruction manual for
the thread trimmer carefully.
6. The contents described in this instruction manual are subject to change without
notice.