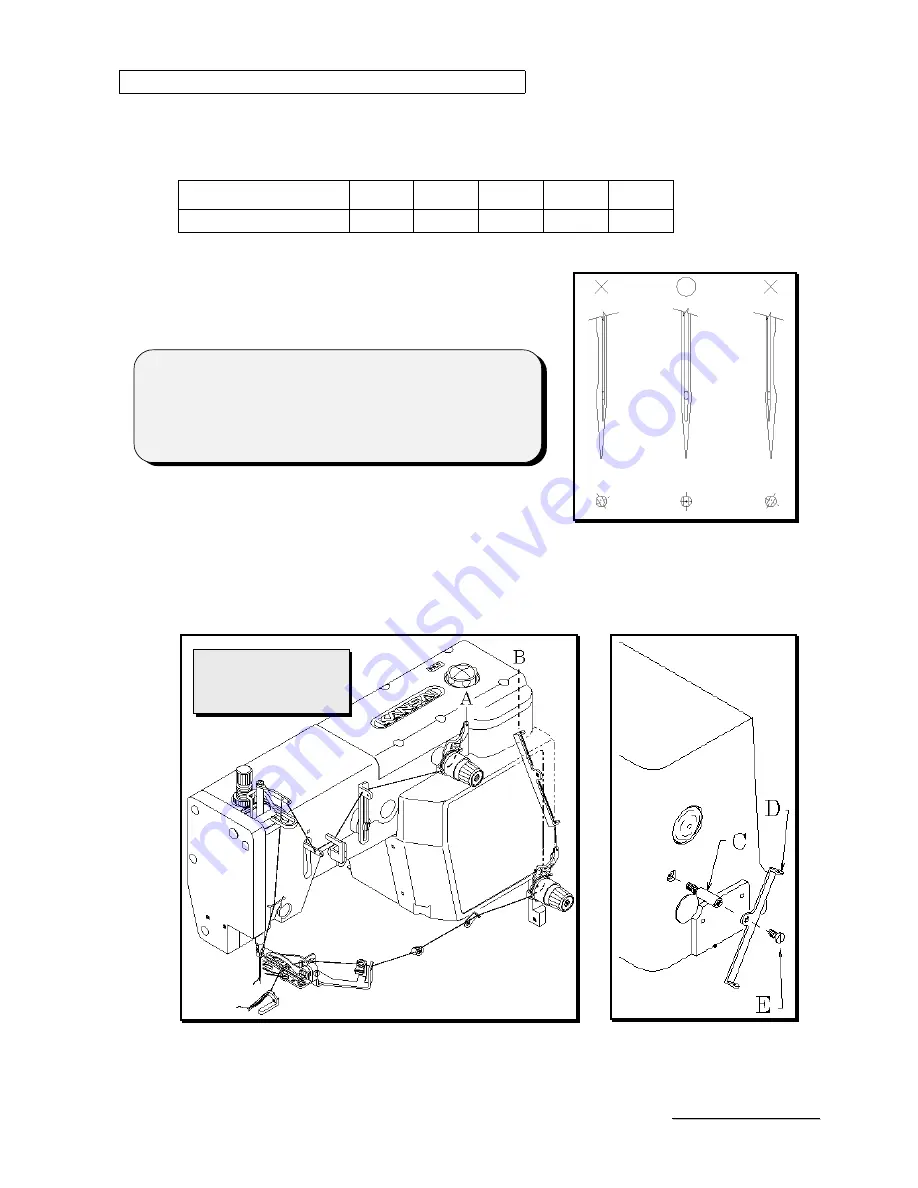
1
M
M
M
M
M
M
M
M
A
A
A
A
A
A
A
A
C
C
C
C
C
C
C
C
1
1
1
1
1
1
1
1
0
0
0
0
0
0
0
0
0
0
0
0
0
0
0
0
【
1
】
NEEDLES & THREADING THE MACHINE
1111----1 Needles
1 Needles
1 Needles
1 Needles
UO163 of Schmetz or Organ
Select the proper needle for the fabric and thread.
< Comparison table of needle sizes >
Schmetz
UY163GAS Nm65 Nm70 Nm75 Nm80 Nm90
Organ UO163
# 9
#10
#11
#12
#14
1111----2 Replacing the needle
2 Replacing the needle
2 Replacing the needle
2 Replacing the needle
When replacing the needle, check the needle carefully
to see that the scarf is turned to the rear of the
machine (see the illustration).
1111----3 To thread the machine
3 To thread the machine
3 To thread the machine
3 To thread the machine
Thread the machine correctly by referring to the illustration below. Incorrect threading
may cause skip stitching, thread breakage and/or uneven stitch formation.
Furthermore, set the thread eyelet D, screw C, screw E (see the illustration).
< Note >
When replacing the needle, be sure to turn off the
machine. A clutch motor continues running for a while
after the machine is turned off. Therefore keep on
pressing the pedal until the machine stops.
A ... Needle threads
B ... Looper threads