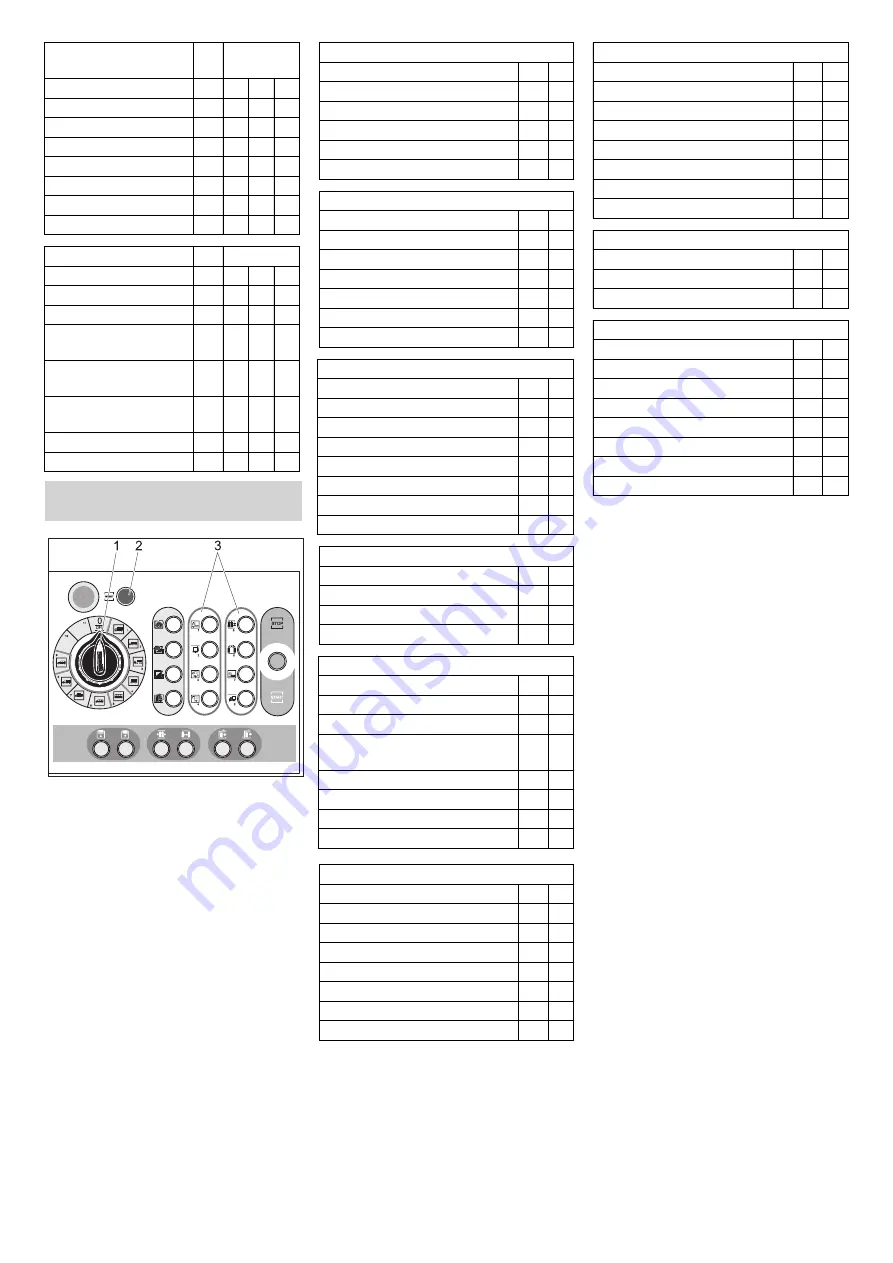
-
11
1 Program selection switch
2 Key "Reset"
3 Function keys
The expanded manual functions are divid-
ed into groups 1 through 9.
Turn the programme selection switch to
the desired number.
The blinking sequence of the "Reset" key
shows the selected group.
Press the function key with the respec-
tive number.
–
I: Function remains active as long as
the corresponding button is pressed.
–
0-I: function is activated the first time
the button is pressed and deactivated
when it is pressed again.
Group 6, signals, card
reader, traffic light
Button
Function
1
2
4
Alarm
0-I X
Wash readiness
0-I
X
Wash is running
0-I X
X
Frost alarm
0-I
X
Forward traffic light
0-I X
X
Stop traffic light
0-I
X
X
Backwards traffic light
0-I X
X
X
Group 7, frost protection
Button
Function
1
2
4
Start frost protection
I
X
Air valve fresh water
0-I
X
Air valve processed wa-
ter
0-I X
X
Air valve undercarriage
wash
0-I
X
Air valve intensive
cleaner
0-I X
X
Air valve high pressure 1 0-I
X
X
Air valve high pressure 2 0-I X
X
X
Manual operation Adv. control
panel
Select group
Select function
Group 1, roof brush
The roof brush rotates forward
0-I 1
Roof brush rotates backwards
0-I 2
Lower roof brush
I
3
Raise roof brush
I
4
Roof brush/roof bar - fast drive
I
5
Reset power meter
I
8
Group 2, side brushes
Rotate side-brushes forwards
0-I 1
Rotate side-brushes backwards 0-I 2
Move in side-brush 1
I
3
Move out side-brush 1
I
4
Move in side-brush 2
I
5
Move out side-brush 2
I
6
Inching mode, side brushes
I
7
Group 3, high pressure, intensive
High pressure roof
0-I 1
High-pressure side
0-I 2
Lower the roof bar
I
3
Raise the roof bar
I
4
Swivel the roof bar, front
0-I 5
Swivel the roof bar, rear
0-I 6
Intensive, side
0-I 7
Intensive, roof
0-I 8
Group 4, portal
Portal forwards
I
1
Portal backwards
I
2
Portal fast drive
0-I 3
(Initialise machine)
I
4
Group 5, water
Dosing pump CTH, front bow (A) 0-I 1
Dosing pump CTH, rear bow (C) 0-I 2
Foam (B)
0-I 3
Brush irrigation of processed wa-
ter A+B+(C)
0-I 4
Brush irrigation fresh water A+B 0-I 5
Post rinse bow fresh water C
0-I 6
Dosing pump shampoo
0-I 7
Dosing pump foam
0-I 8
Group 6, signals, card reader, traffic light
Alarm
0-I 1
Wash readiness
0-I 2
Wash is running
0-I 3
Frost alarm
0-I 4
Forward traffic light
0-I 5
Stop traffic light
0-I 6
Backwards traffic light
0-I 7
Lamp test
0-I 8
Group 7, frost protection
Start frost protection
I
1
Air valve fresh water
0-I 2
Air valve processed water
0-I 3
Air valve undercarriage wash
0-I 4
Air valve intensive cleaner
0-I 5
Air valve high pressure 1
0-I 6
Air valve high pressure 2
0-I 7
Air valve high pressure 3
0-I 8
Group 8, undercarriage wash
Start undercarriage wash
0-I 1
Switch valve pump 1
0-I 2
Switch valve pump 2
0-I 3
Group 9, door control
Open door 1
I
1
Close door 1
I
2
Open door 2
I
3
Close door 2
I
4
Door 1, red traffic light
0-I 5
Door 1, green traffic light
0-I 6
Door 2, red traffic light
0-I 7
Door 2, green traffic light
0-I 8
13
EN
Summary of Contents for TB 36
Page 1: ...TB 36 TB 42 TB 46 TB 50 59637510 1 2 02 19 ...
Page 2: ...2 ...