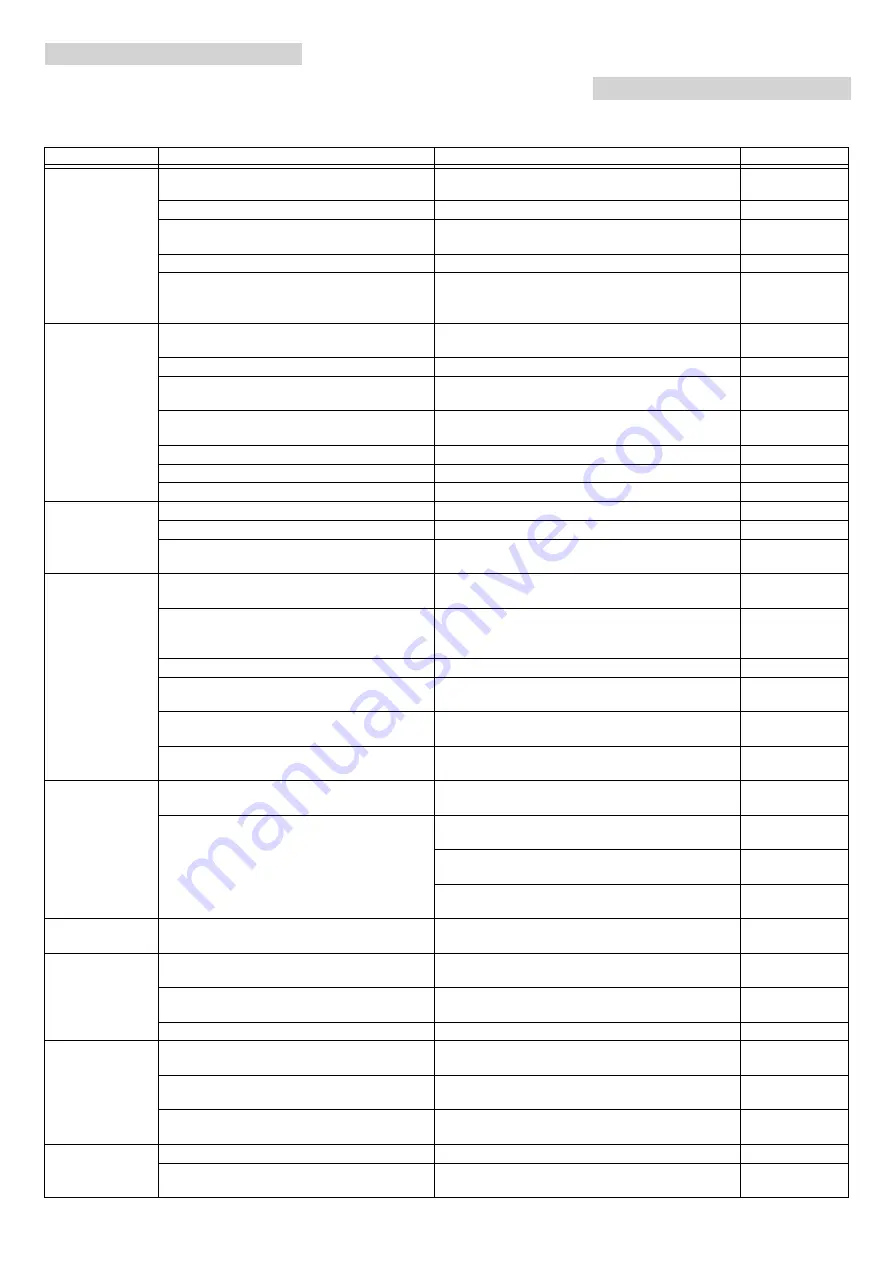
-
8
–
Operator
Work designated with the sign “Opera-
tor” may only be carried out by persons
who have been instructed in the safe
operation and maintenance on the
wash plant
–
Customer Service
Only KÄRCHER service engineers or
engineers authorized by KÄRCHER are
allowed to carry out work with the note
“Customer Service”.
There are indicator lamps in the switching
cabinet that display
Who may remedy faults?
Fault indication
Fault
Possible cause
Remedy
By whom
Indicator Lamp
"Fault" illuminates
The swimmer switch S4.2 has triggererd and
S4.1 is not in the top position.
Washing system runs with fresh water until level S4.1
top is reached. Find the cause.
Customer Service
Float switch S4.2 in the pump basin is defective.
Repair or replace float switch.
Customer Service
Motor protection switch of the immersion pump
has been triggered.
Reset motor protection switch; call Customer Service
if the problem recurs.
Operator
Filter inlay worn out.
Replacing filter inlay.
Customer Service
Fuse F5 blown or multiport valve drive defective.
Test the fuse, if necessary replace with new fuses of
the same capacity. (see "Fuses") If the fault persists,
call customer service.
Operator
The message "Re-
cycled water tank
empty" appears on
the washing sys-
tem and the "Fault"
indicator lights up.
Water level in the pump basin is too low and
emergency fresh water supply has failed
Refill pump basin; check emergency fresh water sup-
ply; repair, if required.
Operator, Custom-
er Service
Float switch S11 is defective or loose.
Replace the float switch or reattach it
Customer Service
Immersion pump has failed, is dirty or defective
Restart the plant by switching off and on; otherwise
call Customer service
Operator
Pipe connections are leaky
Check all pipe connections; seal them, if required
Operator, Custom-
er Service
Controls are defective
Check, repair or replace controls
Customer Service
Multi-channel defective
Repair multi-channel valve; replace defective parts
Customer Service
Manual valve on fresh water supply closed
Open and set to 3,000 l/h.
Customer Service
Plant out of order
Power supply is interrupted
Check power supply and ensure proper supply.
Operator
Controls are defective
Check, repair or replace controls
Customer Service
Replace fuse
Test the fuse, if necessary replace with new fuses of
the same capacity. (see "Fuses")
Operator
Recycled water is
coloured or is
foaming too much
Sludge collector or pump basin is dirty
Emptying and cleaning the basins
Operator/ Disposal
agency
Filter pre-tension is not correct.
Remove motor filament screws, push the motor up-
wards, twist the filter inlay 90° to the right, push the
motor filament filter back down, tighten screws.
Customer service /
trained operator
Filter inlay is defective (leaky)
Replacing filter inlay
Customer Service
Improper detergents are used in the washing
unit or washing hall
Use compatible detergents; rinse the system, if nec-
essary
Operator, Custom-
er Service
Detergent dosing in the washing unit is too high
Check detergent dosing; reset, if necessary
Operator, Custom-
er Service
Washing place cleaned with incompatible deter-
gents
Replace water and rinse the basins
Operator
Water in the recy-
cled water tank has
a bad odour
WRP was switched off during the night or over
the weekend
WRP must be ON continuously
Operator
none or very poor circulation, very little ventila-
tion
Check whether the recirculation valve is open and if
the flow is set to 0.5 m
3
/ h = 8 l/min.
Operator
Check pipes for dirt and damage; clean or replace
them as required
Operator, Cus-
tomer Service
Check the ventilation, the ventilator must clearly bub-
ble in the pump basin.
Operator, Cus-
tomer Service
Continuous flow
sound
Float switch, control or fresh water solenoid
valve defective
Check, repair or replace the concerned component
Operator, Custom-
er Service
Immersion pump is
not functioning
Water level in the pump basis is too low
Washing system runs with fresh water until level S6
top is reached. Find the cause.
Customer Service
Float switch S4 is defective.
Check the float switch; clean, repair or replace it as re-
quired
Operator, Custom-
er Service
Controls are defective
Check, repair or replace controls
Customer Service
Filter output is too
low
Filament filter is blocked
Backwash the filament filter; clean or replace filter in-
lay if required.
Operator, Custom-
er Service
Immersion pump is blocked, defective
Clean, repair, replace immersion pump
Operator, Custom-
er Service
Pipe or valve is leaky, defective, blocked
Check pipes and valves; clean, repair or replace as
required
Operator, Custom-
er Service
Fresh water con-
sumption is too
high
Float switch S9 is defective.
Replace
Customer Service
Conductivity sensor is defective or contaminat-
ed.
Check, clean or replace if necessary.
Operator, Cus-
tomer Service
19
EN
Summary of Contents for WRP 3000 Comfort
Page 2: ...2 ...