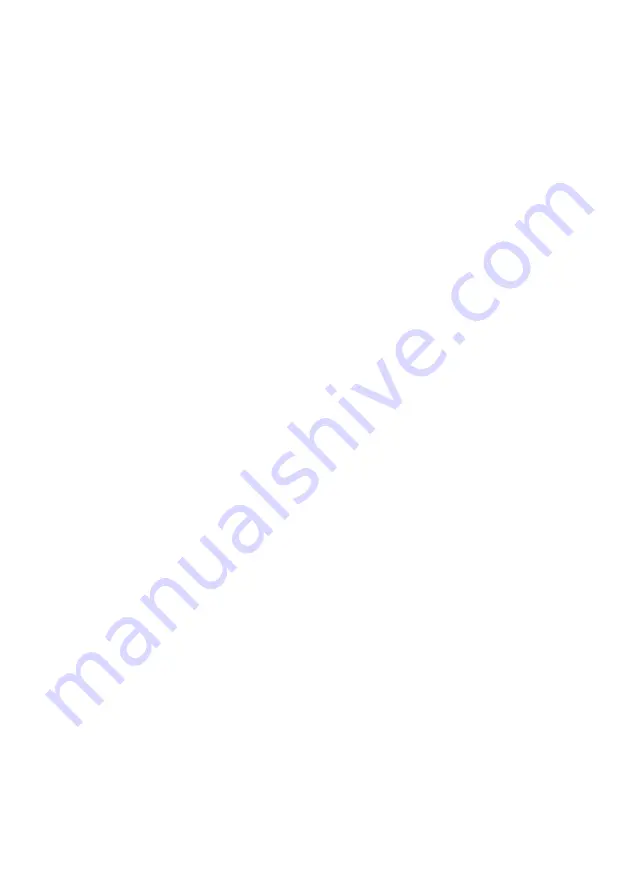
8
that the operator stops the engine. Be careful
not to startle or distract the operator which can
cause an unsafe situation.
Never touch the nylon cutting head when ever
the engine is running. If it is necessary to adjust
the protector or nylon cutting head, be sure
to stop the engine and confirm that the nylon
cutting head has stopped running.
The engine should be turned off when the
machine is moved between work areas.
Be careful not to hit the nylon cutting head
against stones, or the ground. Unreasonable
rough operation will shorten the life of
the machine as well as create an unsafe
environment for yourself and those around you.
Pay attention to loosening and overheating
of parts. If there is any abnormality of the
machine, stop operation immediately and
check the machine carefully. If necessary, have
the machine serviced by a authorized dealer.
Never continue to operate a machine which
may be malfunctioning.
In start-up or during operation of the engine,
never touch hot parts such as the muffler, the
high voltage wire or the spark plug.
After the engine has stopped, the muffler is
still hot.Never place the machine in any places
where there are flammable materials (dry
grass, etc.), combustible gasses or combustible
liquids.
Pay special attention to operation in the rain
or just after the rain as the ground may be
slippery.
If you slip or fall to the ground or into a hole,
release the throttle lever immediately.
Be careful not to drop the machine or hit it
against obstacles.
Before proceeding to adjust or repair the
machine, be sure to stop the engine and
detach the spark plug cap from the spark plug.
When the machine is placed in storage for a
long time, drain fuel from the fuel tank and
carburetor, clean the parts, move the machine
to a safe place and confirm that the engine is
cooled down.
Make periodic inspections to assure safe and
efficient operation. For a thorough inspection of
your machine, please contact a dealer.
Keep the machine away from fire or spark.
It is believed that a condition called Raynaud's
○
phenomenon, which affects the fingers of certain
individuals may be brought about by exposure
to vibration and cold. Exposure to vibration and
cold may cause tingling and burning sensations
followed by loss of color and numbness in the
fingers. The following precautions are strongly
recommended because the minimum exposure
which might trigger the ailment is unknown.
Keep your body warm, especially the head,
neck, feet, ankles, hands and wrists.Maintain
good blood circulation by performing vigorous
arm exercises during frequent work breaks and
also by not smoking.
Limit the hours of operation. Try to fill each
day with jobs where operating the brush cutter
or other hand-held power equipment is not
required.
If you experience discomfort, redness and
swelling of the fingers followed by whitening and
loss of feeling, consult your physician before
further exposing yourself to cold and vibration.
Always wear ear protection, as being exposed to
loud noise for long time can result in diminished
hearing or even loss of hearing. Total face
and head protection must be worn to prevent
bodily injury from either slipping or falling into
shrubbery,branches,or bushes.
Wear no-slip heavy duty work gloves to improve
your grip on the brush cutter handle. Gloves also
reduce the transmission of machine vibration to
your hands.
WARNING: The cutter area is still dangerous
while the machine is coasting to a stop.
Note: Noise and vibration
1.The running at low speed can reduce the
noise and quiver.
2.In order to lower noise, the brush cutter should
be operated in an open environment.
3.The vibration can be lowered if the handle is
grasped firmly.
4.In order to avoid disturbing others, the
machine should be operated in daytime.
5.Wear personal protective equipment, such as
gloves and ear protection during the operation.
6.The machine is not for professional work and
not for long time operation.
7.“In order to keep the user's fit and prolong the
machine's life, please do not work more than 2
hours in a whole day and don't keep working
more than 10 minutes at a time.
○
○
○
○
○
○
○
○
○
○
○
○
○
○
○
○
○
○
○
Summary of Contents for KZ-4000BC-PRO-2S
Page 3: ...1 2 3 8 7 5 6 4 3 2 1 6 5 4 9 8 7 1 0 1...
Page 4: ...9 1 0 1 1 1 2 1 3 1 4 1 5 1 6 1 6 3 1 2 1 1 1 5 1 4 1 7 1 6 1 2...
Page 5: ...3...
Page 6: ...2 9 3 0 3 1 2 3 1 3 0 3 5 3 4 3 3 3 7 3 6 3 3 8 4...
Page 23: ...21 KASEI BRUSH CUTTER KZ 4000BC PRO 2S ENGINE DIAGRAM...
Page 34: ...32 Small Maintenance Big Savings Small Maintenance Big Savings Small Maintenance Big Savings...
Page 35: ......