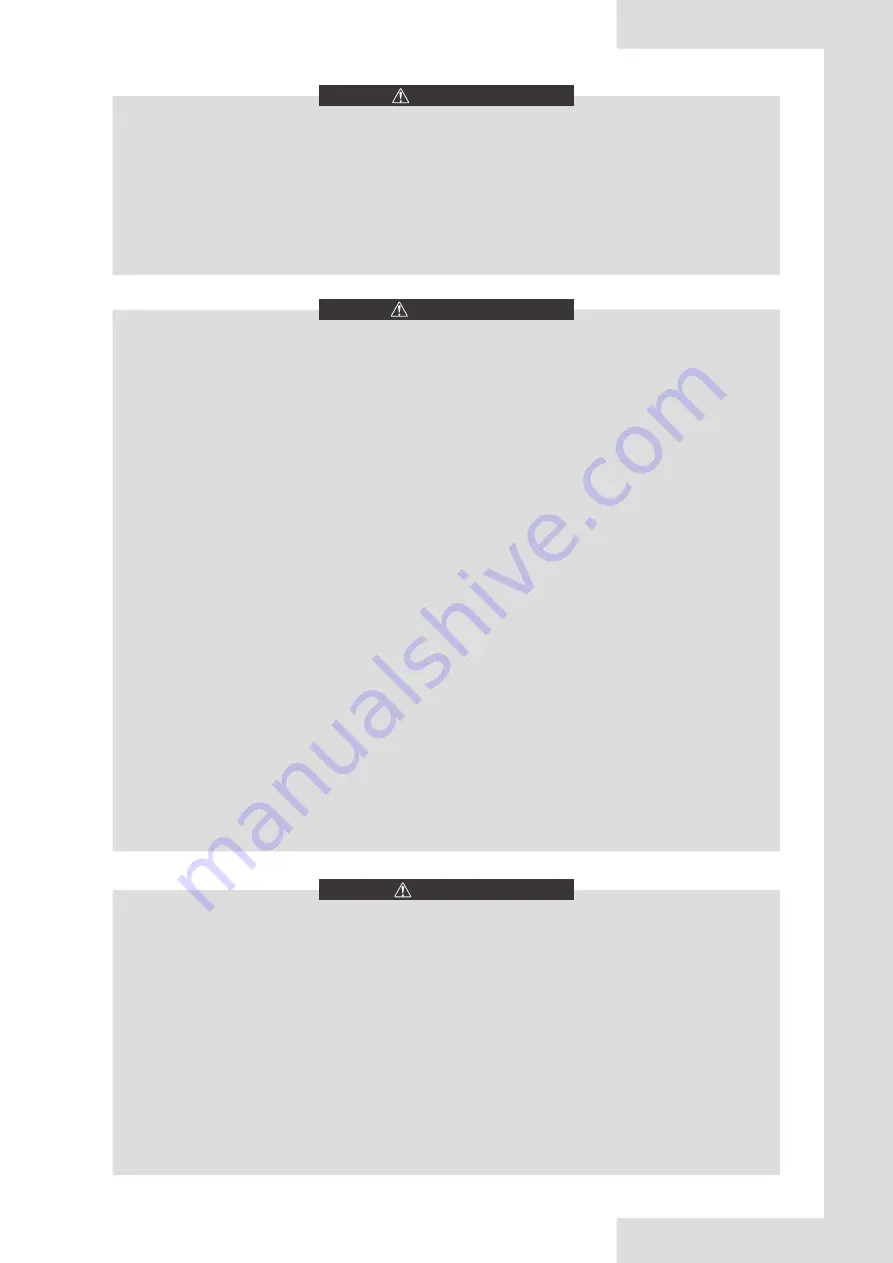
03
DANGER
• Before touching electric terminal parts, turn off power switch.
• When service panels are removed, live parts can be easily touched by accident.
• Never leave the unit unattended during installation or servicing when the service panel is removed.
• Do not touch water pipes during and immediately after operation as the pipes may be hot and could burn your
hands. To avoid injury, give the piping time to return to normal temperature or be sure to wear protective gloves.
• Do not touch any switch with wet fingers. Touching a switch with wet fingers can cause electrical shock.
• Before touching electrical parts, turn off all applicable power to the unit.
WARNING
• Tear apart and throw away plastic packaging bags so that children will not play with them.Children playing with
plastic bags face danger by suffocation.
• Safely dispose of packing materials such as nails and other metal or wood parts that could cause injuries.
• Ask your dealer or qualified personnel to perform installation work in accordance with this manual. Do not install
the unit yourself. Improper installation could result in water leakage, electric shocks or fire
• Be sure to use only specified accessories and parts for installation work. Failure to use specified parts may result
in water leakage, electric shocks, fire, or the unit falling from its mount.
• Install the unit on a foundation that can withstand its weight. Insufficient physical strength may cause the
equipment to fall and possible injury.
• Perform specified installation work with full consideration of strong wind, hurricanes, or earthquakes. Improper
installation work may result in accidents due to equipment falling.
• Make certain that all electrical work is carried out by qualified personnel according to the local laws and regulations
and this manual using a separate circuit. Insufficient capacity of the power supply circuit or improper electrical
construction may lead to electric shocks or fire.
• Be sure to install a ground fault circuit interrupter according to local laws and regulations. Failure to install a
ground fault circuit interrupter may cause electric shocks and fire.
• Make sure all wiring is secure. Use the specified wires and ensure that terminal connections or wires are protected
from water and other adverse external forces. Incomplete connection or affixing may cause a fire.
• When wiring the power supply, form the wires so that the front panel can be securely fastened. If the front panel is
not in place there could be overheating of the terminals, electric shocks or fire.
• After completing the installation work, check to make sure that there is no refrigerant leakage.
• Never directly touch any leaking refrigerant as it could cause severe frostbite.Do not touch the refrigerant pipes
during and immediately after operation as the refrigerant pipes may be hot or cold, depending on the condition
of the refrigerant flowing through the refrigerant piping, compressor and other refrigerant cycle parts. Burns or
frostbite are possible if you touch the refrigerant pipes. To avoid injury, give the pipes time to return to normal
temperature or, if you must touch them, be sure to wear protective gloves.
• Do not touch the internal parts (pump, backup heater, etc.) during and immediately after operation. Touching the
internal parts can cause burns. To avoid injury, give the internal parts time to return to normal temperature or, if
you must touch them, be sure to wear protective gloves.
CAUTION
• Ground the unit.
• Grounding resistance should be according to local laws and regulations.
• Do not connect the ground wire to gas or water pipes, lightning conductors or telephone ground wires.
• Incomplete grounding may cause electric shocks.
- Gas pipes: Fire or an explosion might occur if the gas leaks.
- Water pipes: Hard vinyl tubes are not effective grounds.
- Lightning conductors or telephone ground wires: Electrical threshold may rise abnormally if struck by a lightning
bolt.
• Install the power wire at least 3 feet (1 meter) away from televisions or radios to prevent interference or noise.
(Depending on the radio waves, a distance of 3 feet (1 meter) may not be sufficient to eliminate the noise.)
• Do not wash the unit. This may cause electric shocks or fire. The appliance must be installed in accordance with
national wiring regulations. If the supply cord is damaged, it must be replaced by the manufacturer, its service agent
or similarly qualified persons in order to avoid a hazard.