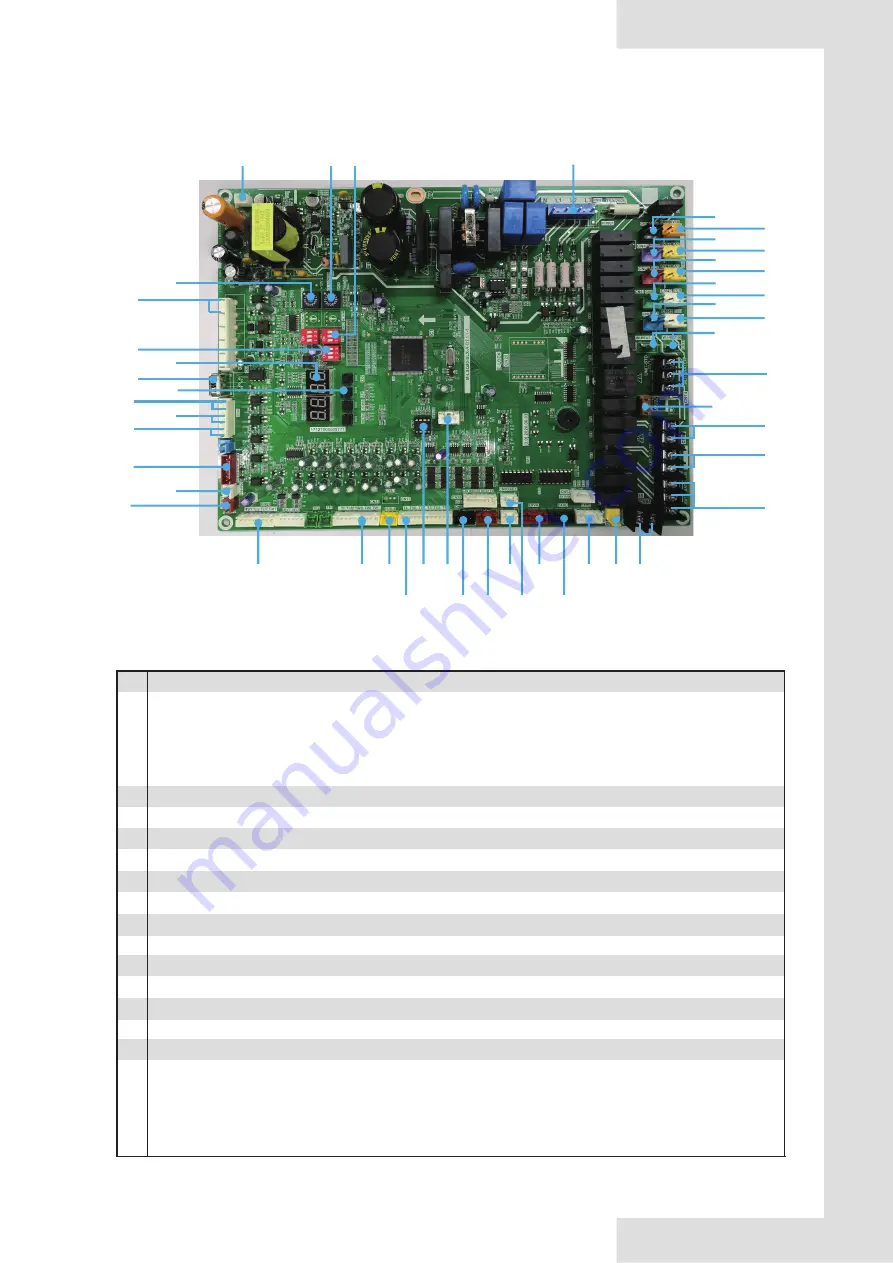
1) Label descriptions are given in Table 8-3
8.3.2MAIN PCB
CN13:Electric of water side heat exchanger heaters connection
CN42:Crankcase heater
NO.
1
2
3
4
5
6
7
8
9
10
11
12
13
14
15
Detail information
CN30
:
Input of three-phase four-wire power supply (fault code E1) Input of transformer, 220-240V AC
current. (only valid for the main unit) Three phases A, B and C of power supply should exist 120° among
them. If the conditions are not met, fault of phase sequence or phase lack may occur, and fault code will
be displayed. When the power supply returns to normal condition, fault is removed. Attention: phase lace
and phase dislocation of power supply are detected only in the early period after the power supply is
connected, and they are not detected while the unit is in operation.
CN12:Quick return oil solenoid valve
CN80:Injection solenoid valve of compressor system B
CN47:Injection solenoid valve of compressor system A
CN5:Water side heat exchanger heaters connection
CN40:Multi-function solenoid valve
Table 8-3
CN41:Liquid bypass solenoid valve
CN6:Four-way valve
Fig. 8-11 Main PCB of
KEM-90 DRS5 KH
and
KEM-180 DRS5 KH
26
1
28
2
3
4
5
6
7
8
9
10
11
12
13
15
16
18
19
20
21
22
24
25
27
29
30
31
32
33
34
35
36
37
38
41
40
42
43
44
45
46 47
17
23
14
39
CN43:Crankcase heater
CN4/CN11:Electric heater of water flow switch
CN27:Three-way valve(hot-water valve,reserve)
CN86:SV2,Spray cooling valve(reserve)
CN25:Pump(220-240V control power supply )
1
)
After receiving start-up instruction, the pump will be started up instantly, and will maintain start-up state
always in the process of operation.
2
)
In case of refrigerating or heating shutdown, the pump will be shut down 2 minutes after all modules stop
operating.
3
)
In case of shutdown under the pump mode, the pump can be directly shut down.
18