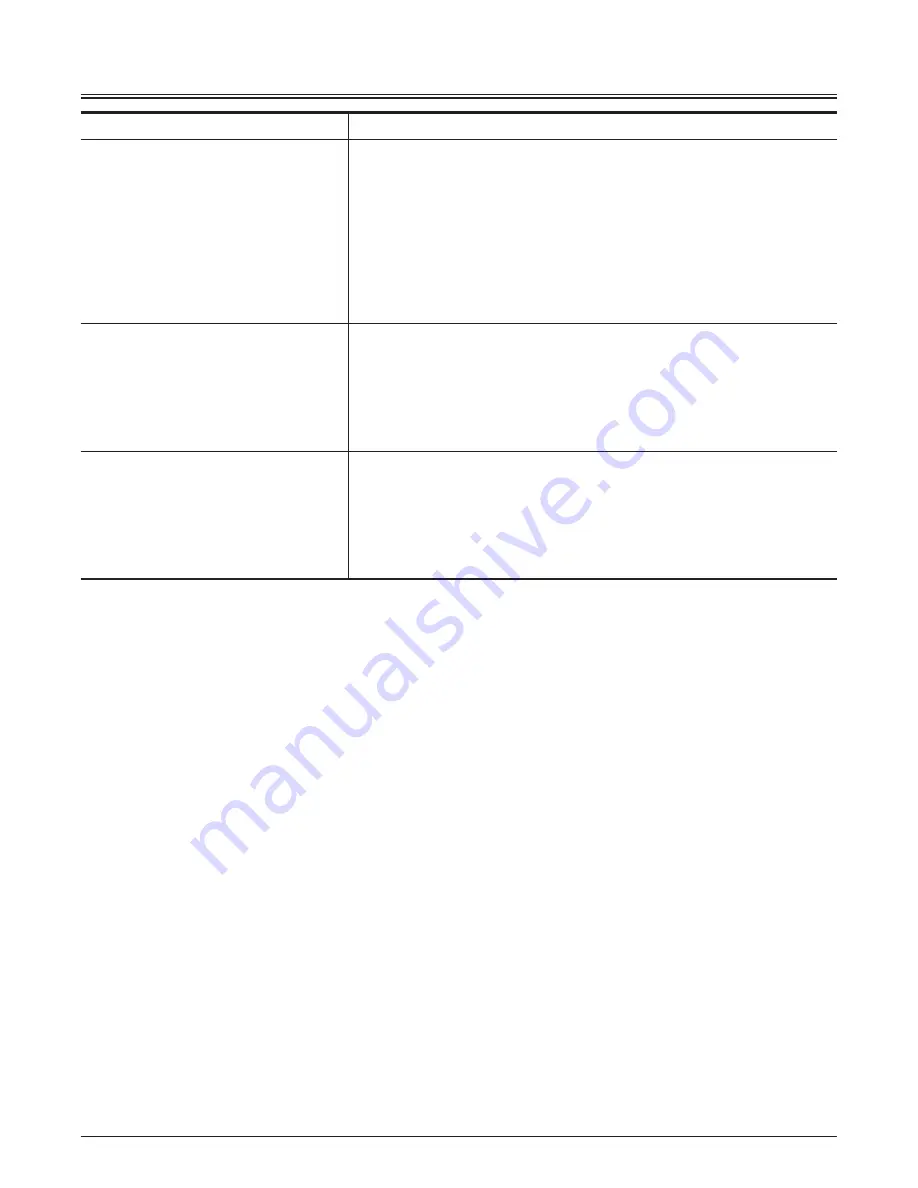
OPERATING THE ENGINE
3-2
Check Points
Check Contents
9.
Chassis
1. Oil leaks of the transmission and the axle
2. Level, leaks and contamination of the fuel tank. Drain water from fuel
tank.
3. Level and leaks of the hydraulic oil tank
4. Operation, play and operating force of control levers and steering wheel
5. Operation of hydraulic equipment. Oil leaks and damage to piping and
hoses.
6. Deformation, damage, and abnormal noise of chassis parts
7. Washer fluid level
10. Loader
1. Oil leaks and damage to cylinders, pipe lines and hoses
2. Loose, worn and missing cutting edges
3. Wear and damage to the bucket
4. Lubrication of the loader parts
5. Damage to the pin lock bolts, stoppers and links
6. Loose and missing mounting bolts/nuts
11. Others
1. Operation of instruments, switches, lights and buzzer/horn
2. Damage and deformation to the ROPS cab
3. Abnormal outside appearance of machine
4. Looseness of the battery terminals
5. Wear, damage, and expiration date of the seat belt
6. Damaged to the steps and handrails
Summary of Contents for 70Z7
Page 2: ...93108 00691 April 2015...
Page 5: ......
Page 11: ...MACHINE NUMBERS 2 MEMO...
Page 51: ...SAFETY LABELS S 40 6 10 4 1 3 9 6 5 SS 3461...
Page 171: ...OPERATOR S STATION 1 110 MEMO...
Page 173: ...BREAK IN 2 2 MEMO...
Page 187: ...OPERATING THE ENGINE 3 14 MEMO...
Page 231: ...OPERATING THE MACHINE 5 24 MEMO...
Page 359: ...MAINTENANCE 7 118 MEMO...
Page 363: ...MAINTENANCE UNDER SPECIAL ENVIRONMENTAL CONDITIONS 9 4 MEMO...
Page 367: ...STORAGE 10 4 MEMO...