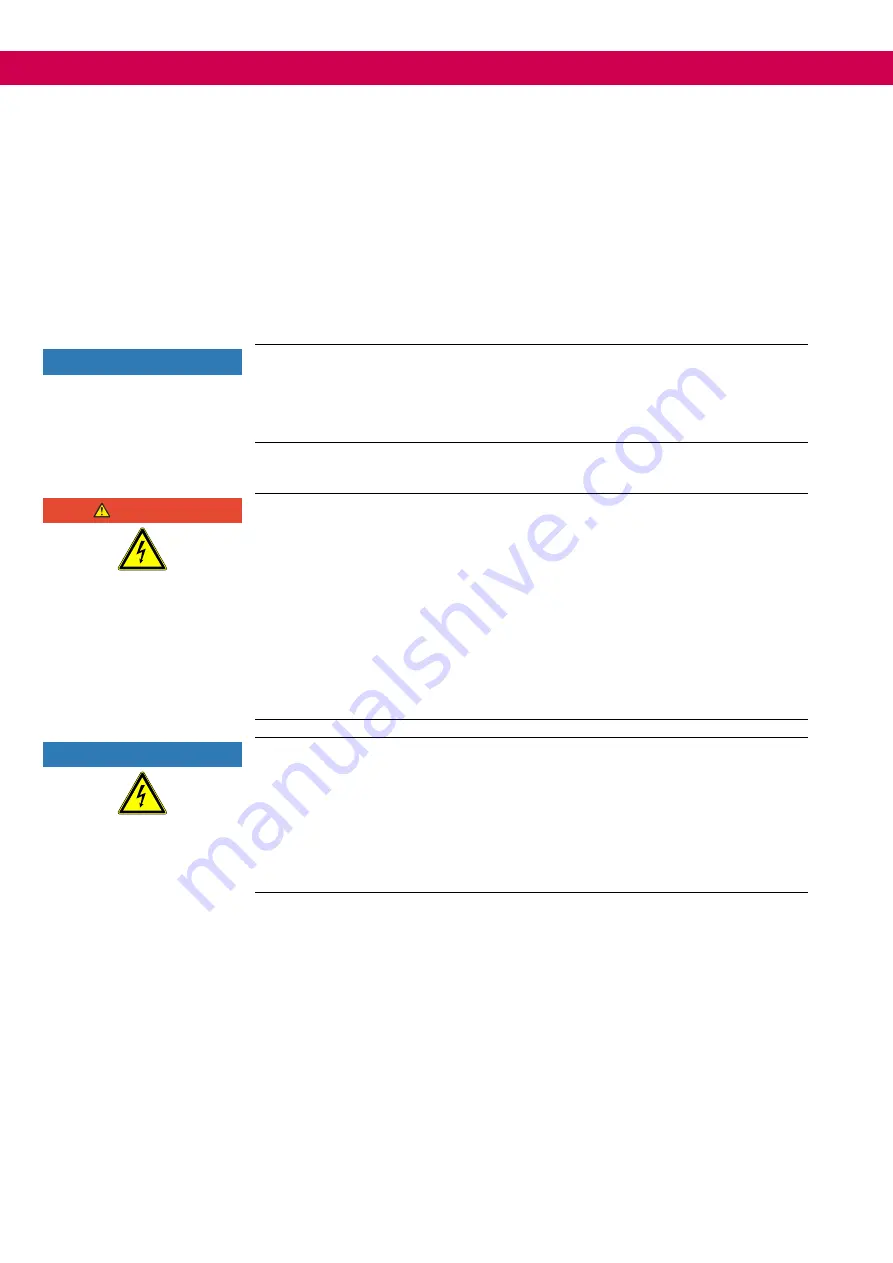
2 | General Safety Instructions
KEB Automation KG
10
ma_dr_f6-cu-a-inst-20118593_en
2 General Safety Instructions
The products are developed and built according to the state of the art and recog-
nized safety rules. Nevertheless, their use may create dangers to life and limb of
the user or third parties or damage to the machine and other material property.
The following safety instructions have been created by the manufacturer for the
area of electric drive technology. They can be supplemented by local, country- or
application-specific safety instructions. This list is not exhaustive. Non-observance
of the safety instructions by the customer, user or other third party leads to the loss
of all resulting claims against the manufacturer.
ACHTUNG
Hazards and risks through ignorance!
a) Read the instructions for use.
b) Observe the safety and warning instructions.
c) Ask if something is unclear.
2.1 Installation
GEFAHR
Electrical voltage at terminals and in the device!
Danger to life due to electric shock !
ü
For any work on the device
a) Switch off the supply voltage.
b) Secure it against switching on.
c) Wait until all drives has been stopped in order that no regenerative energy can
be generated.
d) Await capacitor discharge time (min. 5 minutes). Measure DC voltage at the
terminals.
e) Never bridge upstream protective devices. Also not for test purposes.
ACHTUNG
Use of unsuitable voltage sources!
Electric Shock!
a) Use for the connection only suitable voltage sources with safe isolation (
) in accordance with VDE 0100 with nominal voltage of DC 24 V ±10 %.
b) Pay attention on a sufficient overvoltage category of the voltage supply.
c) With existing or newly wired circuits the person installing the units or machines
must ensure that the
For a trouble-free and safe operation, please pay attention to the following instruc-
tions:
• The electrical installation shall be carried out in accordance with the relevant re-
quirements.
• Cable cross-sections and fuses must be dimensioned by the user according to
the specified minimum/maximum values for the application.
• For drive converters that are not isolated from the supply circuit (in accordance
with
) all control lines must be included in other protective meas-
ures (e.g. double insulation or shielded, earthed and insulated).
• When using components without isolated inputs/outputs, it is necessary that
equipotential bonding exists between the components to be connected (e.g. by
the equipotential line). Disregard can cause destruction of the components by
equalizing currents.