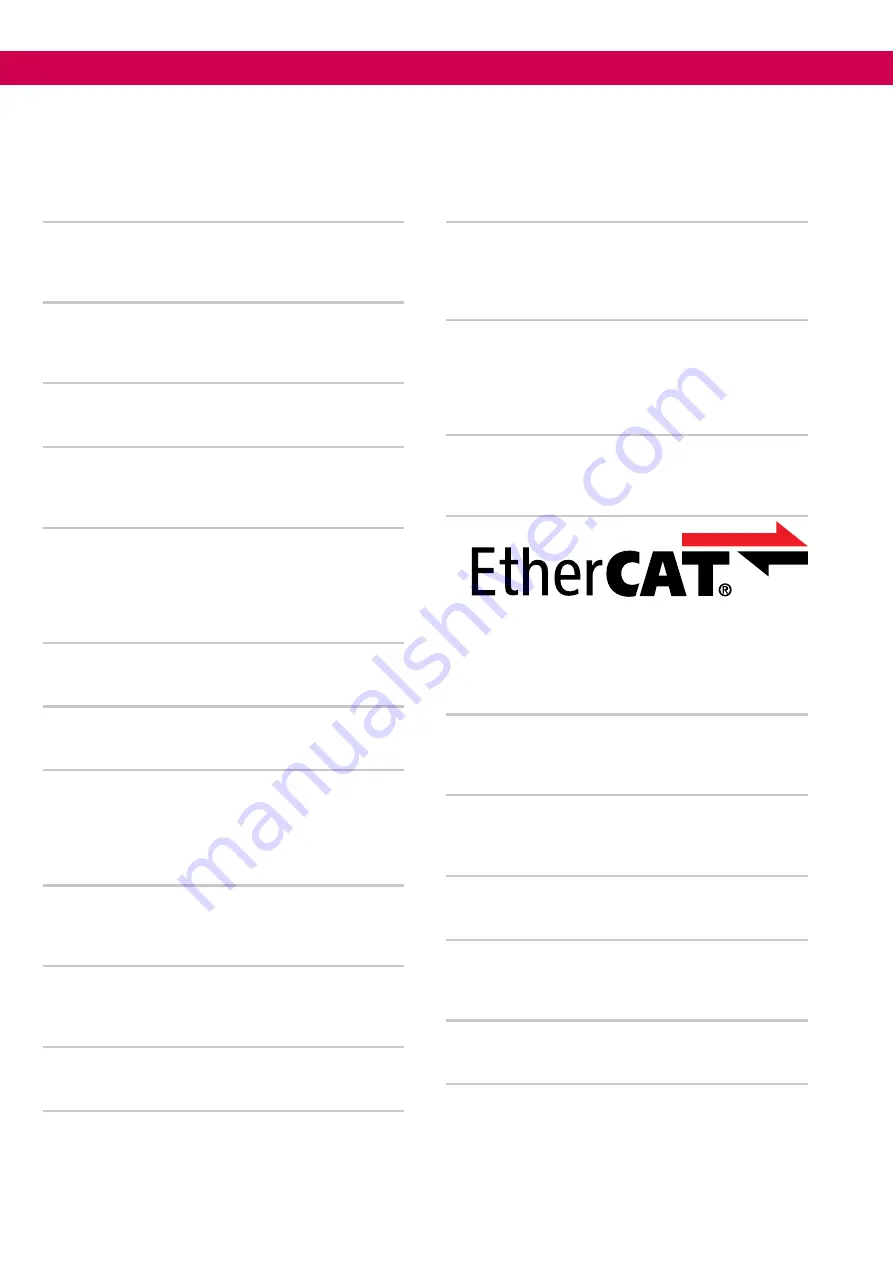
Glossary
KEB Automation KG
44
ma_dr_f6-cu-p-inst-20182705_en
Glossary
Application
The application is the intended use of the KEB
product.
Autonegotiation
Procedure for determining the max. transmission
speed.
Basic insulation
Protection against contact with electrical voltage.
BiSS
Open source real-time interface for sensors and
actuators
CAN®
Serial bus system running protocols such as CAN-
open, Devicenet or J1939. CAN is a registered
trademark of the CAN in AUTOMATION - Interna-
tional Users and Manufactures Group e.V.
COMBIVERT
Proper name for a KEB Drive Controller
COMBIVIS
KEB start-up and parameterizing software
Customer
The customer has purchased a product from KEB
and integrates the KEB product into his product
(customer product) or resells the KEB product (re-
seller).
DIN 66019
Information processing; control method with the 7-
bit code during data transmission.
DIN EN 61131-2
Programmable controllers - Part 2: Equipment re-
quirements and tests
Directive 2006/42/EC
Machinery Directive
Directive 2014/30/EU
Electromagnetic Compatibility (EMC) Directive
EN 60204-1
Safety of machinery - Electrical equipment of ma-
chines - Part 1: General requirements (VDE
0113-1, IEC 44/709/CDV).
EN 61800-5-1
Adjustable speed electrical power drive systems.
Part 5-1: Safety requirements - Electrical, thermal
and energy requirements (VDE 0160-105-1, IEC
61800-5-1)
EnDat
Bidirectional encoder interface of the company
Heidenhain
EtherCAT®
EtherCAT is a real-time Ethernet bus system. Eth-
erCAT is a registered trademark and patented
technology, licensed by Beckhoff Automation
GmbH, Germany.
HCT
Component for current measurement in the power
circuit.
Hiperface
Bidirectional encoder interface of the company
Sick-Stegmann
HSP5
Fast, serial protocol
HTL
Incremental signal with an output voltage (up to
30V) -> TTL
PELV
Safe protective extra-low voltage (earthed).
RS485
RS-485 is an industry standard according to
EIA-485 for a physical interface for asynchronous,
serial data transmission.