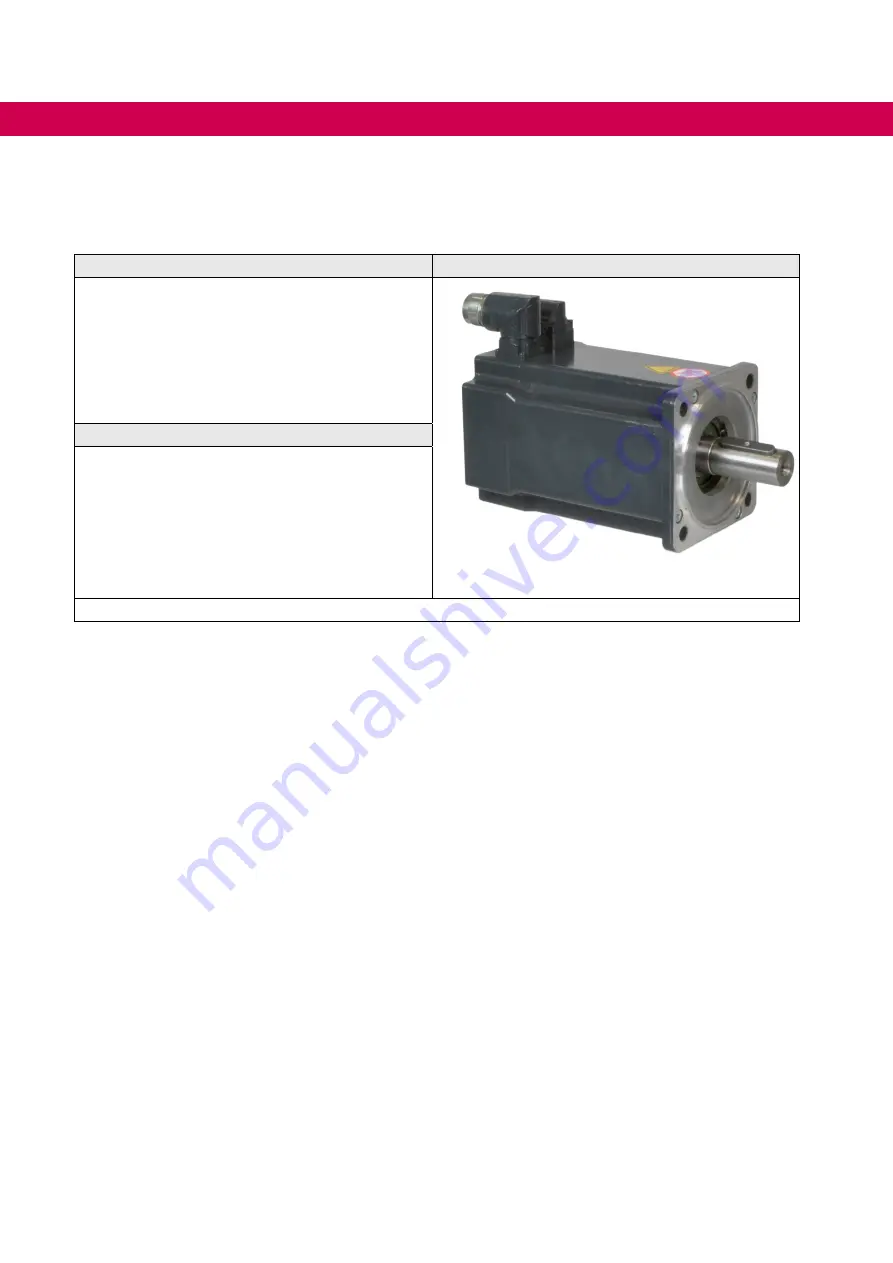
22
PRODUcT DEScRIPTION
2.7
Construction and definition
2.7.1 Drive end and direction of rotation
Drive end of the motor
View
the two ends of a motor are defined
as follows:
D
N
D (Drive End):
Drive end (AS) of the motor.
N (Non-Drive End):
Non-drive end (BS) of the motor.
Direction of rotation of the motor
When the motor terminals U1, V1, W1 are connect-
ed to the drive converter output with U, V, W (with
this same phase order) the motor rotates in a clock-
wise direction when viewed facing the D-end.
Figure 2:
Example figure of an engine
Summary of Contents for DYNAMIC LINE III
Page 2: ......
Page 12: ...12 Standards forasynchronousand synchronous motors ...
Page 58: ...58 NOTES ...