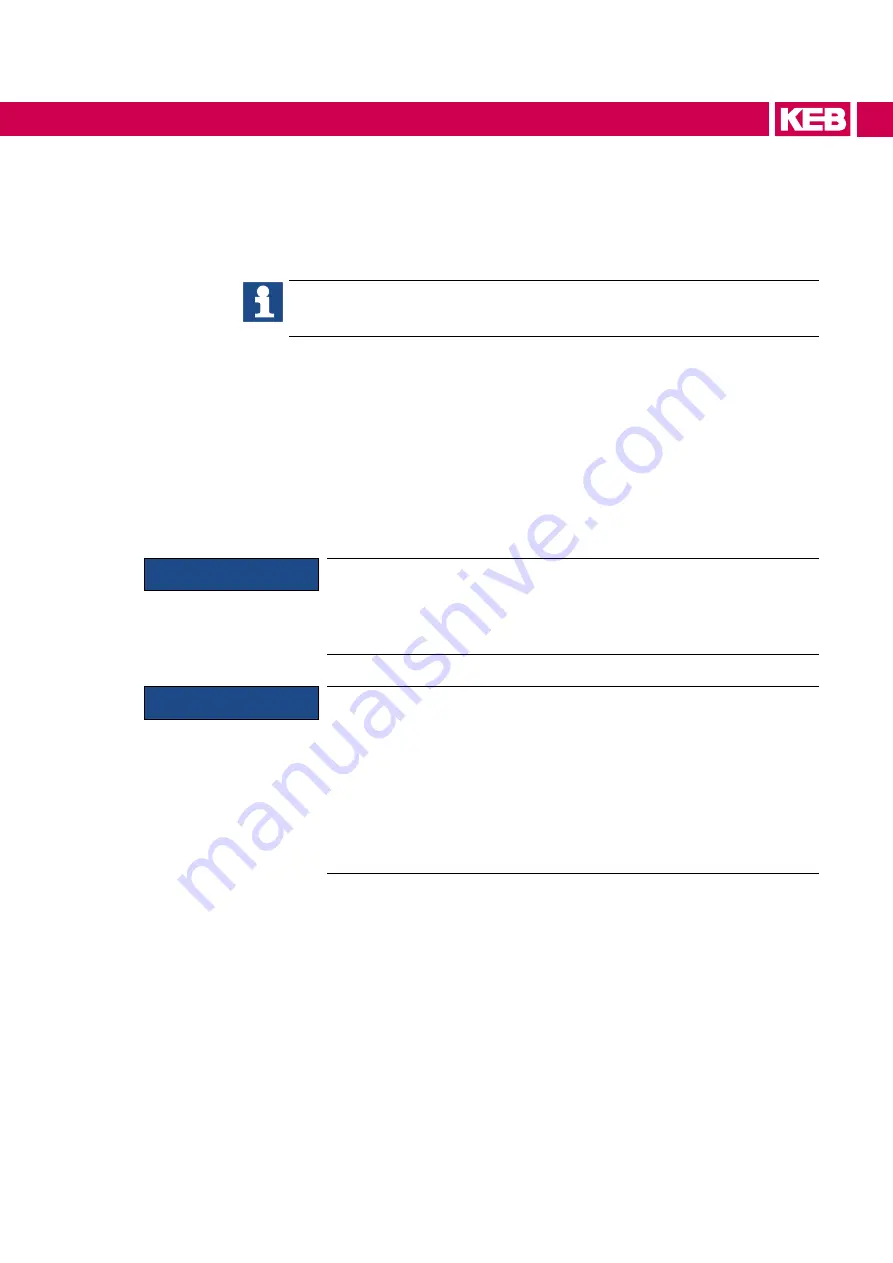
23
PRODUcT DEScRIPTION
2.7.2 Winding and insulation system
The insulation materials we use ensure insulation class 155 (F)
. There-
fore, the winding temperature may be max. 105 K at a coolant temperature of +40°C.
The insulation system of the motors is designed such that they can be connected to a
drive converter with a maximum DC link voltage
U
ZK max
= 840 V DC (constant 690 V DC).
U
link max
.
is the maximum value of the DC link voltage which is only transient
and approximately equivalent to the inception voltage of the braking transistor
or of the regenerative unit.
2.7.3
Holding brake (optional)
The optional built-in holding brake is used to fix the motor shaft when the motor is at
standstill or de-energized. It is a permanent-field single-disc brake which operates on
the closed-cicuit principle, i.e. the brake is effective when the motor is de-energized,
thus the motor shaft is held.
Holding brakes are operated on DC current. The rated voltage is 24 V. They can be con-
nected to a central DC voltage supply. Overvoltages are not permitted, even not tempo-
rary. The excitation current ripple must be less than 20 % to ensure reliable opening of
the brake and prevent disturbing humming noises.
ATTENTION
Holding brake is not a working brake!
Check the proper functioning of the brake (optional) after installing the
motor. The optional holding brake is only designed for a limited number
of emergency brakings. Never use it as a working brake.
ATTENTION
Motor rotation in spite of an active brake!
Since the holding brakes are permanent-magnet brakes, be sure to
observe the correct polarity of the DC voltage, otherwise the brake will
not open.
Modern (field-oriented) drive converters are able to produce a high
torque even at low motor speeds. If the drive converter has sufficient
current reserve, a multiple of the rated motor torque can be generat-
ed. In this case the motor shaft may turn even if the holding brakle is
applied, because the holding torque of the brake is exceeded.
Summary of Contents for DYNAMIC LINE III
Page 2: ......
Page 12: ...12 Standards forasynchronousand synchronous motors ...
Page 58: ...58 NOTES ...