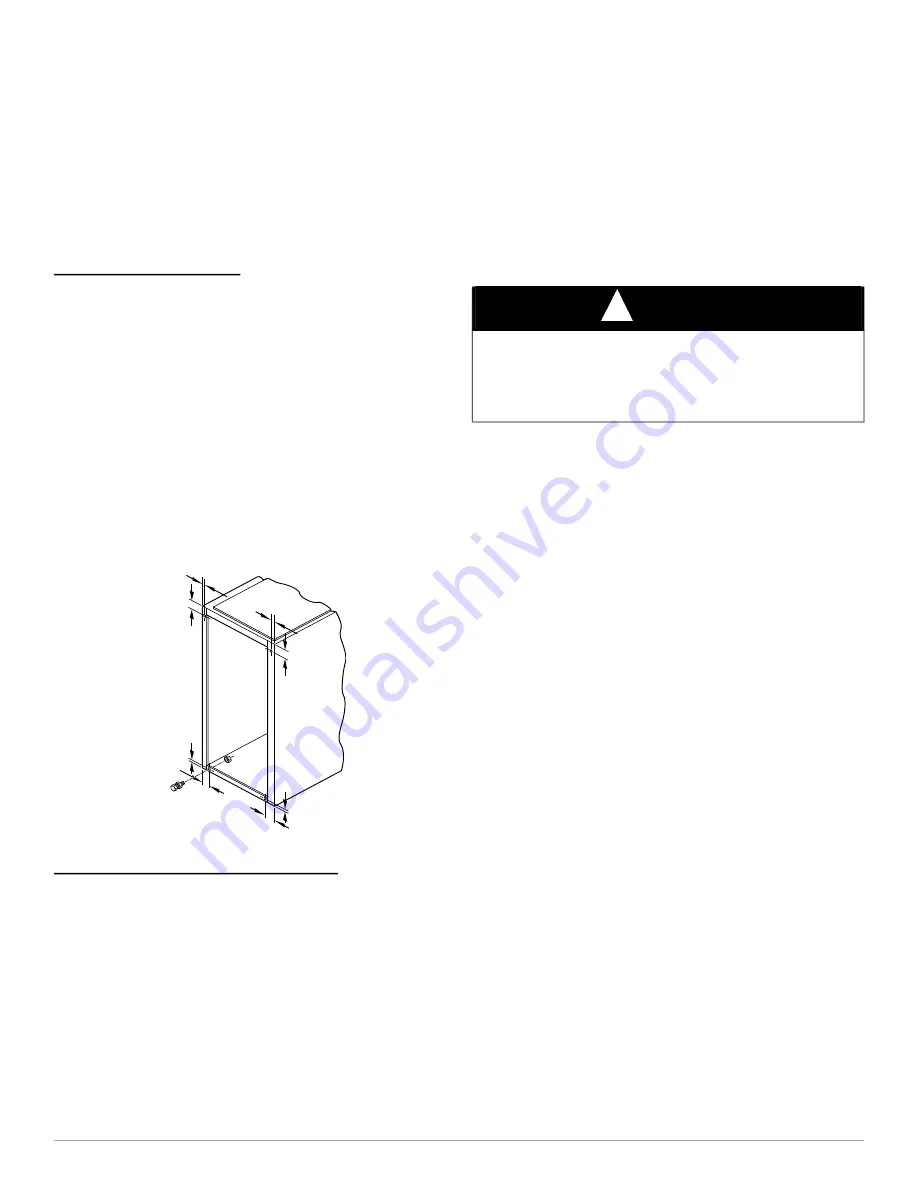
F96VTN and G96VTN: Installation, Start-up, Operating and Service and Maintenance Instructions
Manufacturer reserves the right to change, at any time, specifications and designs without notice and without obligations.
24
Cooling
4
and Heating Air Delivery - CFM (Bottom Return
5
with Filter) - NOTES
1.Nominal 350 CFM/ton cooling airflow is delivered with SW1-5 and SW2-2 set to OFF.
Set both SW1-5 and SW2-2 to ON for +7% airflow (nominal 370CFM/ton).
Set SW1-5 to ON and SW2-2 to OFF for +15% airflow (nominal 400CFM/ton)
Set SW1-5 to OFF and SW2-2 to ON for -7% airflow (nominal 325 CFM/ton)
The above adjustments in airflow are subject to motor horsepower range/capacity
This applies to Cooling and Low-Cooling airflow, but does not affect continuous fan airflow.
2.Max cooling airflow is achieved when switches SW2-6, SW2-7, SW2-8 and SW1-5 are set to ON, and SW2-2 is set to OFF.
3.All heating CFM’s are when comfort/efficiency adjustment switch SW1-4 is set to OFF.
4.Ductwork must be sized for high-heating CFM within the operational range of ESP. Operation within the blank areas of the chart is not recommended because high-heat operation will be
above 1.0 ESP.
5.All airflows on 21” (533 mm) casing size furnaces are 5% less on side-return only installations.
6.Side returns for 24.5” (622 mm) casing sizes require two sides, or a side and bottom to allow sufficient airflow at the return of the furnace.
7.Airflows over 1800 CFM require bottom return, two-side return, or bottom and side return or excessive watt draw may result. A minimum filter size of 20x25” (508 x 635 mm) is required.
Leveling Legs (If Desired)
In upflow position with side return inlet(s), leveling legs may be used.
See
. Install field-supplied, 5/16 x 1-1/2 in. (8 x 38 mm) (max)
corrosion-resistant machine bolts, washers and nuts.
NOTE:
Bottom closure must be used when leveling legs are used. It
may be necessary to remove and reinstall bottom closure panel to install
leveling legs. To remove bottom closure panel, see
To install leveling legs:
1. Position furnace on its back. Locate and drill a hole in each bottom
corner of furnace.
2. For each leg, install nut on bolt and then install bolt with nut in
hole. (Install flat washer if desired.)
3. Install another nut on other side of furnace base. (Install flat washer
if desired.)
4. Adjust outside nut to provide desired height, and tighten inside nut
to secure arrangement.
5. Reinstall bottom closure panel if removed.
A89014
Fig. 28 – Leveling Legs
Location Relative to Cooling Equipment
The cooling coil must be installed parallel with, or on the downstream
side of the unit to avoid condensation in the heat exchangers. When
installed parallel with the furnace, dampers or other flow control must
prevent chilled air from entering the furnace. If the dampers are
manually operated, they must be equipped with means to prevent
operation of either unit unless the damper is in the full-heat or full-cool
position.
AIR DUCTS
General Requirements
The duct system should be designed and sized according to accepted
national standards such as those published by: Air Conditioning
Contractors Association (ACCA Manual D), Sheet Metal and Air
Conditioning Contractors National Association (SMACNA) or
American Society of Heating, Refrigerating and Air Conditioning
Engineers (ASHRAE) or consult
The Air Systems Design Guidelines
reference tables available from your local distributor. The duct system
should be sized to handle the required system design CFM at the design
external static pressure. The furnace airflow rates are provided in
-Air Delivery-CFM (With Filter). When a furnace is installed so
that the supply ducts carry air circulated by the furnace to areas outside
the space containing the furnace, the return air shall also be handled by
duct(s) sealed to the furnace casing and terminating outside the space
containing the furnace.
Secure ductwork with proper fasteners for type of ductwork used. Seal
supply- and return-duct connections to furnace with code approved tape
or duct sealer.
NOTE:
Flexible connections should be used between ductwork and
furnace to prevent transmission of vibration.
Ductwork passing through unconditioned space should be insulated to
enhance system performance. When air conditioning is used, a vapor
barrier is recommended.
Maintain a 1-in. (25 mm) clearance from combustible materials to
supply air ductwork for a distance of 36-in. (914 mm) horizontally from
the furnace. See NFPA 90B or local code for further requirements.
Return Duct Sizing
Refer to the Filter Selection and Duct Sizing section for information on
the proper selection of filter sizes and the associated ductwork and duct
transitions. Improperly designed filtering systems and return ductwork
are the most common causes of airflow and/or noise complaints in
HVAC systems.
Ductwork Acoustical Treatment
NOTE:
Metal duct systems that do not have a 90 degree elbow and 10
ft. (3 M) of main duct to the first branch take-off may require internal
acoustical lining. As an alternative, fibrous ductwork may be used if
constructed and installed in accordance with the latest edition of
SMACNA construction standard on fibrous glass ducts. Both
1
3
/
4
″
1
3
/
4
″
1
3/
4
″
1
3/
4
″
5/
16
″
5
/
16
″
5/
16
″
5/
16
″
(44mm)
(8mm)
(44mm)
(8mm)
(8mm)
(8mm)
(44mm)
(44mm)
NOTICE
!
Many states, provinces and localities are considering or have
implemented standards and/or restrictions on duct sizing practices,
ductwork leakage, and/or ductwork thermal, airflow and electrical
efficiencies. CONSULT LOCAL CODE OFFICIALS for ductwork
design and performance requirements in your area.