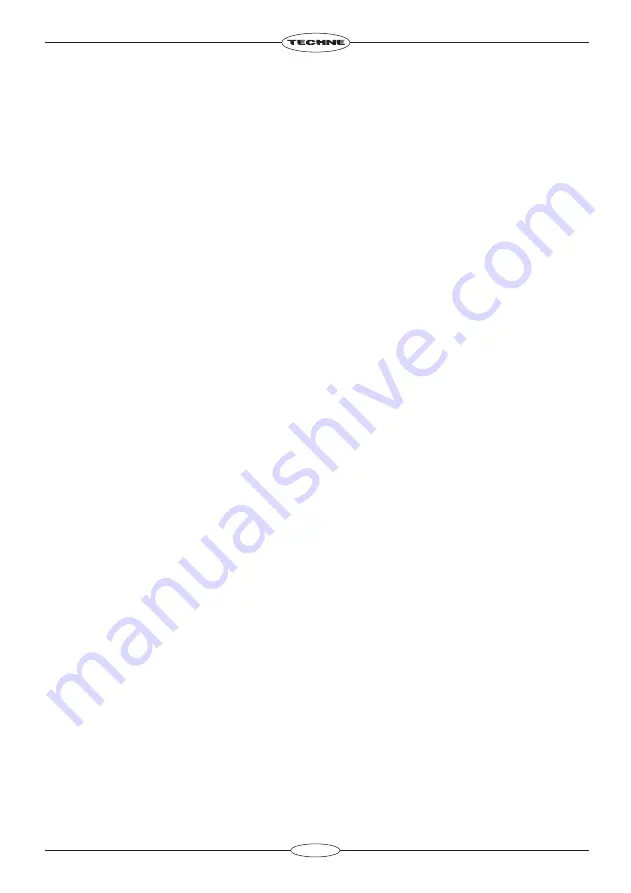
materials being treated and the working environment. a brief description of the components is as
follows:-
cyclone assemblies to remove the majority of any fluidised medium that may become entrained in the
extracted fumes. the cyclone(s) are positioned in the exhaust ductwork directly after the fluidised bath
so that the fluidised medium is removed from the fumes before it contaminates other fume treatment
equipment.
a filter assembly to remove any fine particles of fluidised medium and any non-organic particles such as
paint pigments or fillers that may be present in the extracted fumes. the filter assembly is positioned in
the exhaust ductwork directly after the cyclone(s).
a liquid scrubber to remove any corrosive acids and other soluble noxious fumes (especially hydrochloric
acid and harmful by products of pVc and other halogenated polymers) from being emitted into the
atmosphere. the scrubber is positioned in the exhaust ductwork after the cyclone(s) (and filter if used),
but before the extraction fan.
an extraction fan to direct any fumes generated in the fluidised bath through the various fume treatment
components. the extraction fan is positioned in the exhaust ductwork after the cyclone(s) (and filter and
scrubber, if used), but before the afterburner.
In addition, the exhaust ductwork should contain a damper valve to enable the rate of fume removal to
be adjusted according to system requirements. a dilution tee should be positioned between the fluidised
bath and the cyclone(s) to be optimised and to ensure that the oxygen content of the exhaust fumes is
sufficient to obtain stable combustion within the afterburner.
the exhaust ductwork should be designed to have a minimal pressure drop and should be as short as
possible with the minimum of bends. Some polymers produce oil vapour when thermally decomposed,
these oils can condense on the walls of the ductwork where they combine with any particular matter and
may eventually block the ductwork or the cyclone(s). It is therefore important to ensure that the ductwork
can easily be dismantled for cleaning. In applications where the formation of oils cause serious ductwork
problems, the ductwork may be thermally insulated to reduce the level of condensation.
the exhaust stack from the outlet spigot of the afterburner to atmosphere should be suitable for
operation with exhaust temperatures in the order of 450°c. a stainless steel lined double walled
insulation stack is suggested. the stack should be fitted with a weather-proof termination where it
terminates to atmosphere.
2