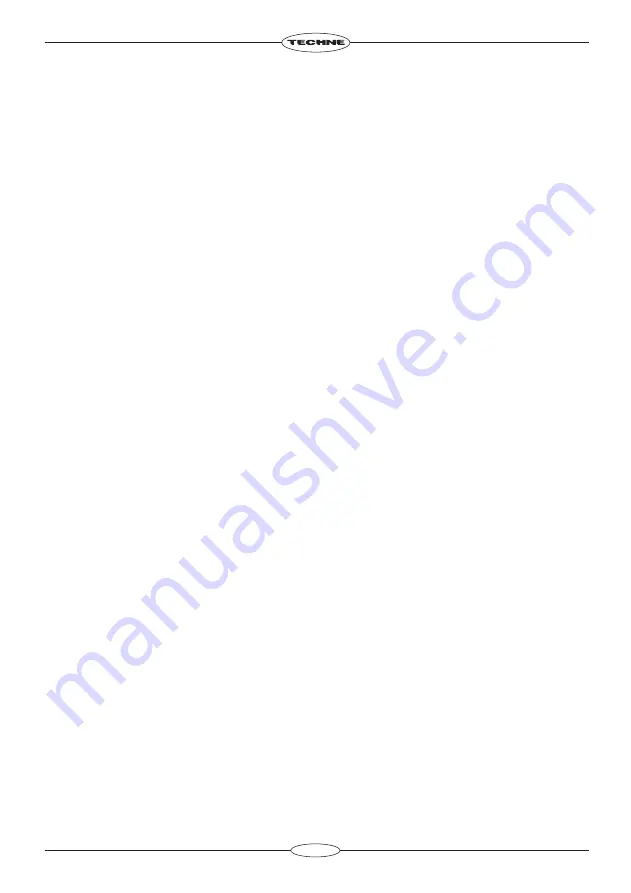
7
commissioning
With the extraction fan switched on and operating in the correct direction, ensure that the gas supply is
turned on at the remote manual shut off valve (if fitted in supply line), and that an input gas pressure of
greater than 6 inches is registered on the input gas pressure gauge.
With the main gas flow regulating valve (situated in the main gas line prior to the burner but within the
gas train console) in the off position, switch the power switch to the on position.
the fan failure neon should be extinguished. If the neon is illuminated, check the operation of the
extraction fan and the connections between either side of the differential pressure switch and the
ductwork/base of the afterburner. the operating position of the differential switch may be adjusted if
required by removing the yellow plastic plug on the side of the switch body and rotating, the internal
screw.
When the fan failure light is extinguished, the automatic start up sequence should commence, as detailed
in the General description of this manual.
It is not common for the burner to initially fail to ignite due to the air within the gas supply line or an
incorrectly set pilot flame adjuster. If the flame control system goes into a lock-out mode, leave for
approximately 60 seconds with the power switch in the on position before depressing the start button
to re-initiate the start up procedure.
the pilot light adjuster needs to be used either to establish a flame initially or to modify the flame.
remove the end cap of the pilot light adjuster, situated above the main gas flow manual adjusting valve,
and adjust the internal screw. a pilot flame of sufficient size to successfully sustain the flame control
system in the on position is needed.
once the pilot flame has been successfully established and detected by the flame probe, the main gas
solenoid valves will be heard to open as they are energised.
the main gas flow limiter, or ballofix valve, adjacent to the main gas flow valve, should initially be set in
the fully open position.
opening the main gas flow adjusting valve should establish the main burner flame. adjustment to the
size of the flame and the setting of the gas flow limiter should be attempted during a cleaning cycle in
the fluidised bath. under conditions where the maximum fumes are generated within the fluidised bath
the flame should be adjusted and may also be limited such that acceptable fume emission from the
exhaust stack is achieved.
adjustable profile plates are situated either side of the burner plate within the combustion chamber.
these plates may be moved towards or away from the burner plate so as to achieve ideal contact
between the flame and the fumes being treated with the minimum pressure drop within the system.
adjustments built into the ductwork system as described in the General description section of this
manual allow the fume treatment system to be tuned according to system requirements. however,
adjustments tend to be interactive, the best results being usually obtained by trial and error.
the ducting damper valve may be used to reduce the overall extraction flow rate, which reduces the gas
consumption of the exhaust fumes. however, the fume extraction flow rate must be high enough to
entrain any fumes produced during the cleaning process.