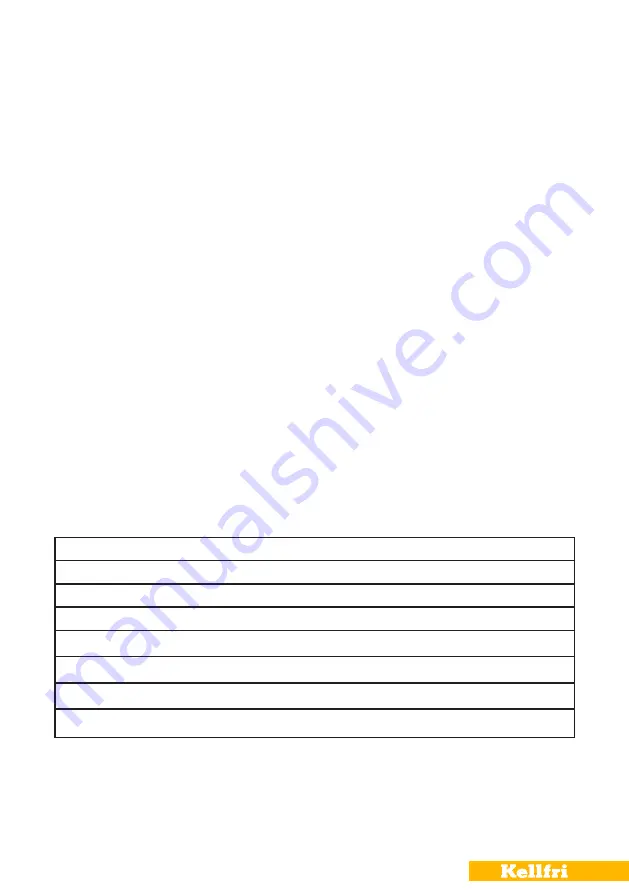
13
TRANSPORT AND STORAGE
Check that the area is free of persons, children and objects prior transportation. Always take
precaution when transporting and moving the machine. Make sure that the implement or
product is well anchored and that existing transport safety lock are fitted. Always place the
load as low as possible. Always have the risk zone in mind when transporting and moving the
machine. In case of lifting, nobody is allowed to stand under suspended load. Trailers used for
transport should have functional brakes.
Always store the machine or product in a dry place, preferably under roof when not in use.
Make sure that the implement or product is standing steady and there is no risk for it to tip
over. Never allow children to play where the machine is stored. Keep in mind the risk of tip-
ping! When storing a machine, it should be cleaned and all bearings and knives are lubricated.
MAINTENANCE AND SERVICE
Make sure the implement is stable and there’s no risk of falling over during maintenance and
service. Replace damaged and worn parts immediately to reduce the risk of machine failure
and injuries. Perform maintenance, service and inspections as recommended. Use only spare
parts with equivalent performance to reduce the risk of damage and failure.
Regularly check the condition of the machine. Retighten bolts and other nuts as needed. If
cracks, twisting, bending ore wear are detected, top the operation and rectify the error. Avoid
using the machine at lower temperatures more than -20 ° C and higher temperatures than +
30 ° C. Check that all bolts and nuts are tightened after maintenance and service. Always test
the machine before starting he operation. Take great care when repairing a machine. If the
ladder is to be used for repair or maintenance, ensure that it is stable.
Avoid burns, wait until the machine has cooled enough before repair or maintenance is carried
out, wear protective gloves.
Make sure there is no pressure left in the system before repair or maintenance is performed
on the machine.
OIL
First oil change after 30 hours
There after once a year
OIL FILTER
New machine - Replace after 30 hours
After every 100 hours or every time the oil is changed once a year
LUBRICATION OF JOINTS
Lubricte regularly, at least 2 times a year or every time service / maintenance is performed
For ordering spare parts
: Contact Kellfri Service
RECYCLING
Disposal of the product, disassemble and transport to the municipality’s recycling station.
Contact your local authority for further information