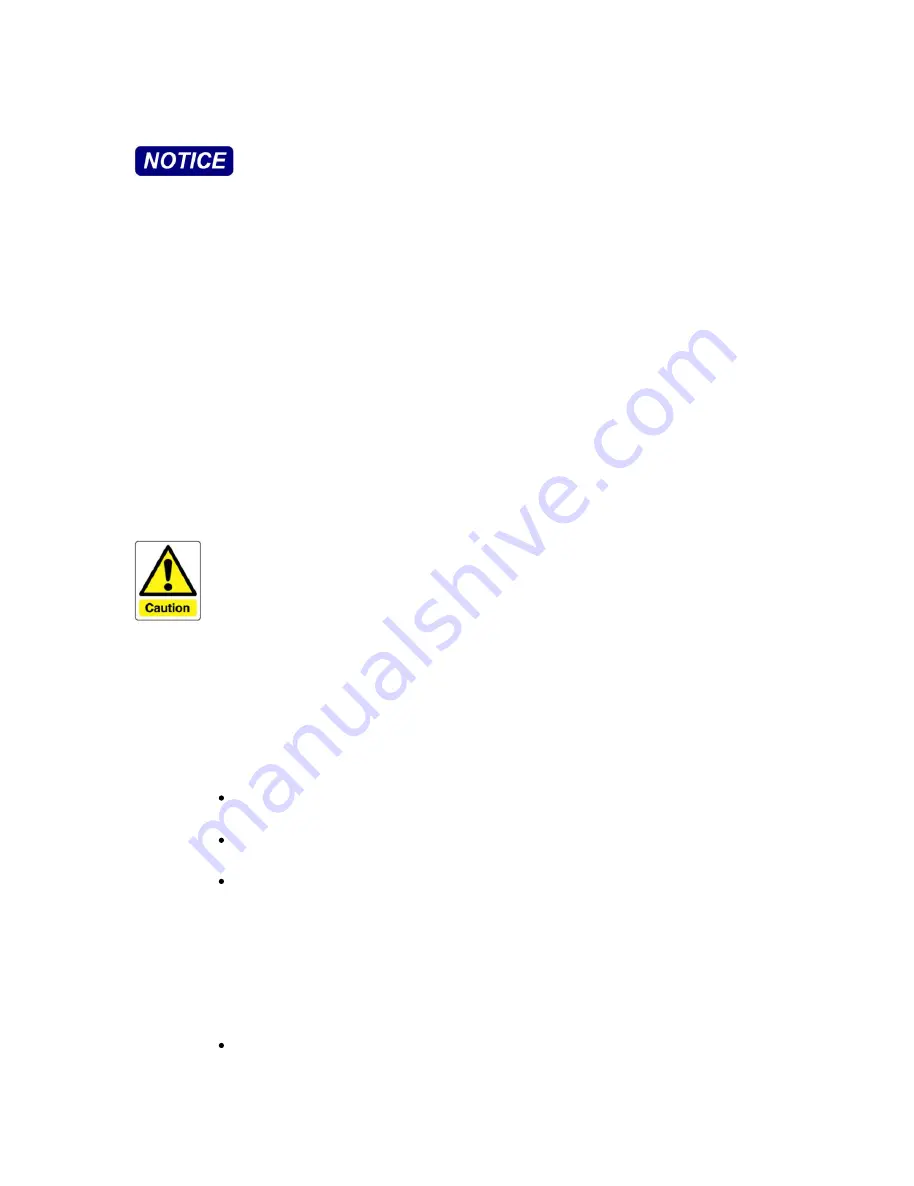
6
To obtain reliable and satisfactory service, this unit requires a consistent preventative
maintenance program. Maintenance schedule pages should be used to aid in keeping
proper records.
General:
1.
Check your compressor regularly!
2.
Check the entire system for air leakage around fittings, connections, and gaskets,
using soap and water solution.
3.
Remove rust and oil soiling.
4.
Check fastener tightness by using torque wrench to the corresponding values
within the full operations manual.
Compressor Oil:
-
Check oil level every week and top off if necessary. Fill the oil tank with
recommended oil until the sight glass is ¾ full.
Use the Same Brand Oil Every Time, Do Not Mix Oil Types, Weights, or Brands!
-
Compressors are filled with Kellogg break-in lubricant. This is an ISO non-
detergent industrial lubricant with rust and oxidation inhibitors specifically
formulated for reciprocating compressors.
-
Normal break-in period of Kellogg air compressors is 25 hours. After which, the
compressor oil needs to be drained and replaced with Kellogg Synthetic
Lubricant.
Compressors must run for a 25-hour break-in period, using Kellogg ISO
100 oil.
After 25 hours, thoroughly drain existing oil from crankcase, and replace
with synthetic lubricant.
Run compressor for 200 hours. Thoroughly drain and replace again with
synthetic lubricant.
-
For the first 500 hours of compressor operation, a careful and regular check of the
oil level should be made. Maintain full oil level at all times.
-
After the first 500 hours the compressor is now ready to run for extended periods
before next lubricant change is required. Maintain full oil level at all times in
between oil changes.
-
Frequency Of Oil Changes:
Change oil every 3000 operating hours.
All manuals and user guides at all-guides.com