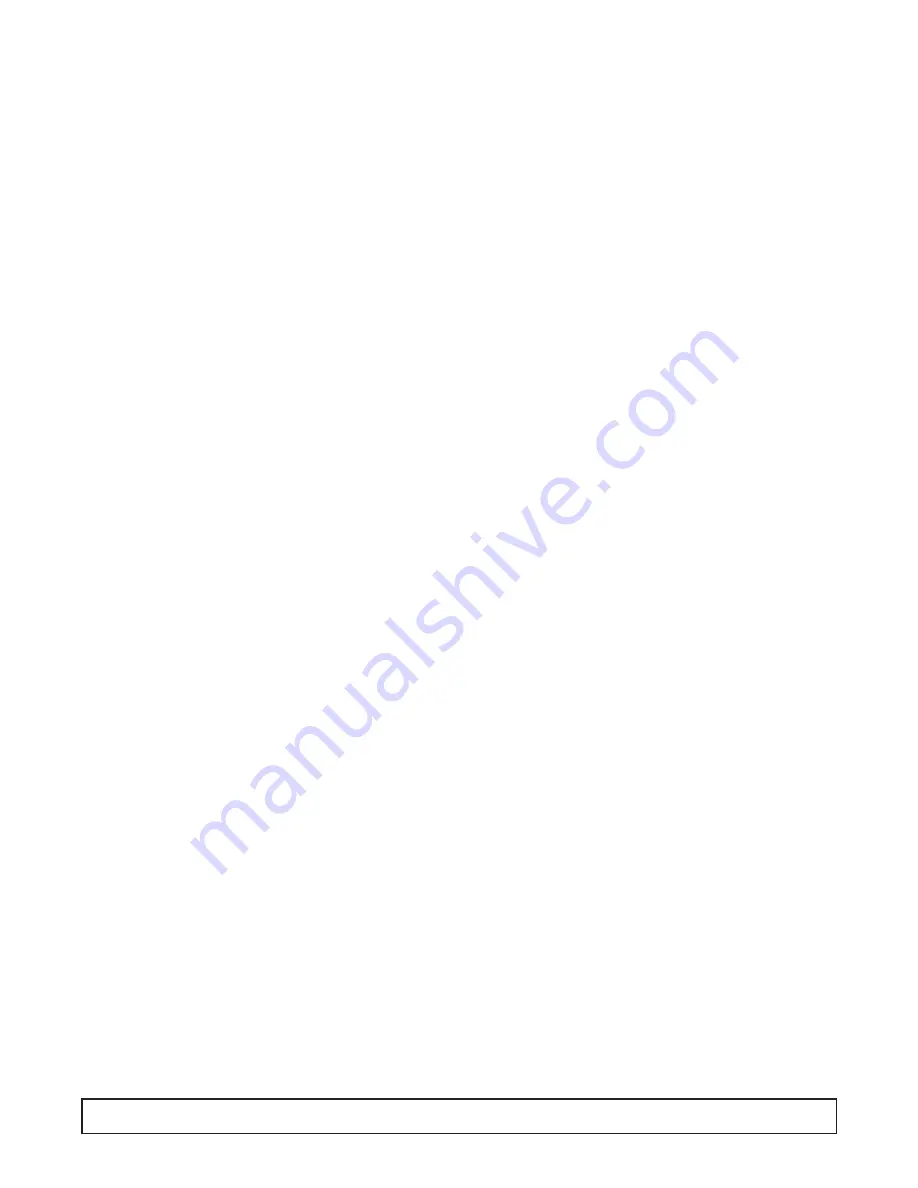
CHECKING FOR ELECTRICAL TROUBLE
When checking for electrical trouble, always be sure
there is a “live” electrical circuit to the cabinet and that the
thermostat dial is not in the “OFF” position. When the
sealed unit will not start and the cabinet temperature is
warm, the trouble may be in the relay, in the thermostat,
in the wiring, or it may be in the compressor motor itself.
If the compressor will not run, make a test across the
power lead terminals (one at the relay, the other at the
overload protector). See Figure 15, page 18. The test
should show a live circuit if the thermostat knob is in the
normal operating position and not in the “OFF” position.
If this check does not show positive, the thermostat and
wiring should be checked for an open circuit.
If the compressor motor does not start, check the line
voltage, to see that there is not more than 10% variation
from the normal 115 volts. If the voltage is correct, relay
and overload check out, and the compressor will not start
and run, change the compressor. Even though the cause
of the electrical trouble is determined, check the com-
plete electrical circuit. Look for broken wire, wires with
frayed ends, and loose terminals.
REFRIGERATION SERVICE
OPERATING CHARACTERISTIC
On the initial startup of a warm cabinet, the suction pres-
sure drops rapidly to about 0 to 5 pounds. This will vary
some with the temperature of the cabinet and the ambi-
ent temperatures. After 15 to 20 minutes of operation, the
suction pressure begins to rise again and will rise to
about 20 to 30 pounds.
The head pressure also rises and they both “peak” or
stop rising about 30 to 60 minutes of operation.
Abnormally warm cabinets and high ambient tempera-
tures will affect both the pressure and the time interval
involved by raising the pressures and lengthening the
intervals.
After this “peak” has been reached, the discharge and
suction pressures begin to drop slowly.
After some 30 minutes of operation, the system starts to
lower the air temperature inside the cabinet. The dis-
charge pressure will gradually lower as the cabinet tem-
perature drops until a point is reached consistent with the
ambient temperature. The suction pressure will drop as
the cabinet temperature drops until the compressor is
shut off by the thermostat. Table 3 on page 15 gives aver-
age suction and discharge pressures for the different
sized cabinets for a thermostat setting of 5 1/2 on the
temperature selector dial. Discharge pressures are given
for both 70°, 80° and 90° ambient temperatures. To
check operating pressure, install service taps and ser-
vice gauges. The capillary tube allows the high pressure
refrigerant to pass into the low side when the unit is on
the “OFF” cycle. The discharge pressure is therefore
lowered and the motor starting load is greatly reduced.
The time required for unloading is about 8 minutes when
the cabinet is down to operating temperatures as the
majority of the refrigerant is in the low side. However,
when a warm cabinet is just started and during the initial
pull down, the unloading is considerably longer.
CHANGING THE COMPRESSORS
Carefully study the section “Refrigeration Service”
before changing the sealed compressor and definitely
determine that this is necessary before proceeding.
TO INSTALL A REPLACEMENT
COMPRESSOR:
1. Disconnect power to the cabinet.
2. Disconnect wire leads from the compressor.
3. Attach a manifold gauge set to both high and low ser-
vice taps of system.
4. Reclaim all refrigerant in system.
5. Unbraze secondary tube connections from the cabi-
net to a compressor assembly.
6. Install primary tubes on new compressor; oil cooler;
discharge, etc.
7. Install the new compressor in the cabinet and
rebraze secondary tube connections.
8. Install a new filter drier.
9. Evacuate below 500 microns and valve off to check
for leaks.
10. Check serial rating plate for refrigerant type and
charge. Weigh in refrigerant and check for leaks
before turning cabinet on.
11. Refer ELECTRICAL & REFRIGERATION INFOR-
MATION pages for the proper refrigerant charge.
Weigh in the proper charge or use a charging cylin-
der to measure in the proper charge.
12. Check high side of system for leaks with compressor
running. Stop compressor and allow pressure to build
up on the low side, then check the low side for leaks.
13. Start compressor. Replace machinery compartment
grill.
REFRIGERANT SERVICE
LEAK TESTING
The serviceman making a leak test on any cabinet that
has urethane foam insulation must first understand the
characteristics of the insulation and what some of its
chemicals are. Number one is that the urethane foam is
charged with Freon R-22 as a blowing agent.
The refrigerant is sealed in the cells of the urethane
foam and when a cell opens, it will release a small
GENERAL OPERATIONS
17