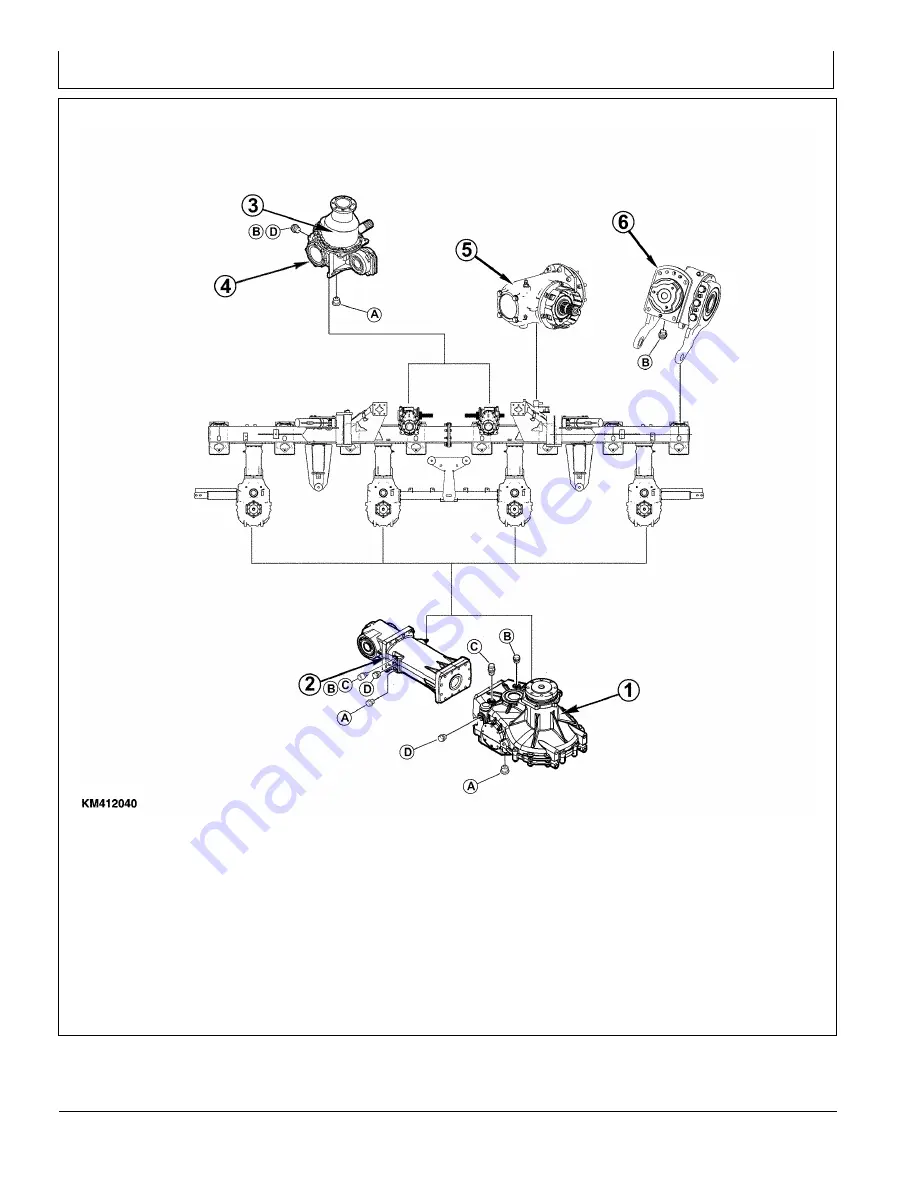
Lubrication and Periodic Service
KM00321,0000A9A -19-15MAY20-1/1
Overview of Transmissions and Oil Levels
KM412040
—UN—06MA
Y21
A—Oil Drain Plug
B—Oil Filler Plug
C—Breather
D—Oil Level Plug
1— Gathering Drum Spur Gear
Angle Drive - 8.5 L (2.25 US.
gal.)
2— Angle Drive - 1.5 L (0.4 US.
gal.)
3— Feed Drum Spur Gear Angle
Drive (Filled Lifetime with 1.1
kg (2.42 lb.) of Low-Viscosity
Grease for Gears)
4— Spur Gear Angle Drive - 1.1 L
(0.29 US. gal.)
5— FENDT Gearbox - 0.8 L (0.21
US. gal.)
6— StalkBuster™ Spur Gear
Angle Drive - 0.4 L (0.11 US.
gal.) Oil Castrol Alphasyn EP
150
IMPORTANT: The oil in the drives must be changed
after the first 100 operating hours and then
every 500 operating hours.
1. Raise the rotary harvesting unit until it is horizontal.
2. Unfold the rotary harvesting unit as described under
Unfolding and Folding the Rotary Harvesting Unit.
60-7
061721
PN=80
Summary of Contents for 460plus
Page 6: ...Contents iv 061721 PN 4...
Page 108: ...Serial Number 80 2 061721 PN 108...
Page 111: ...Index Index 3 061721 PN 3...
Page 112: ...Index Index 4 061721 PN 4...