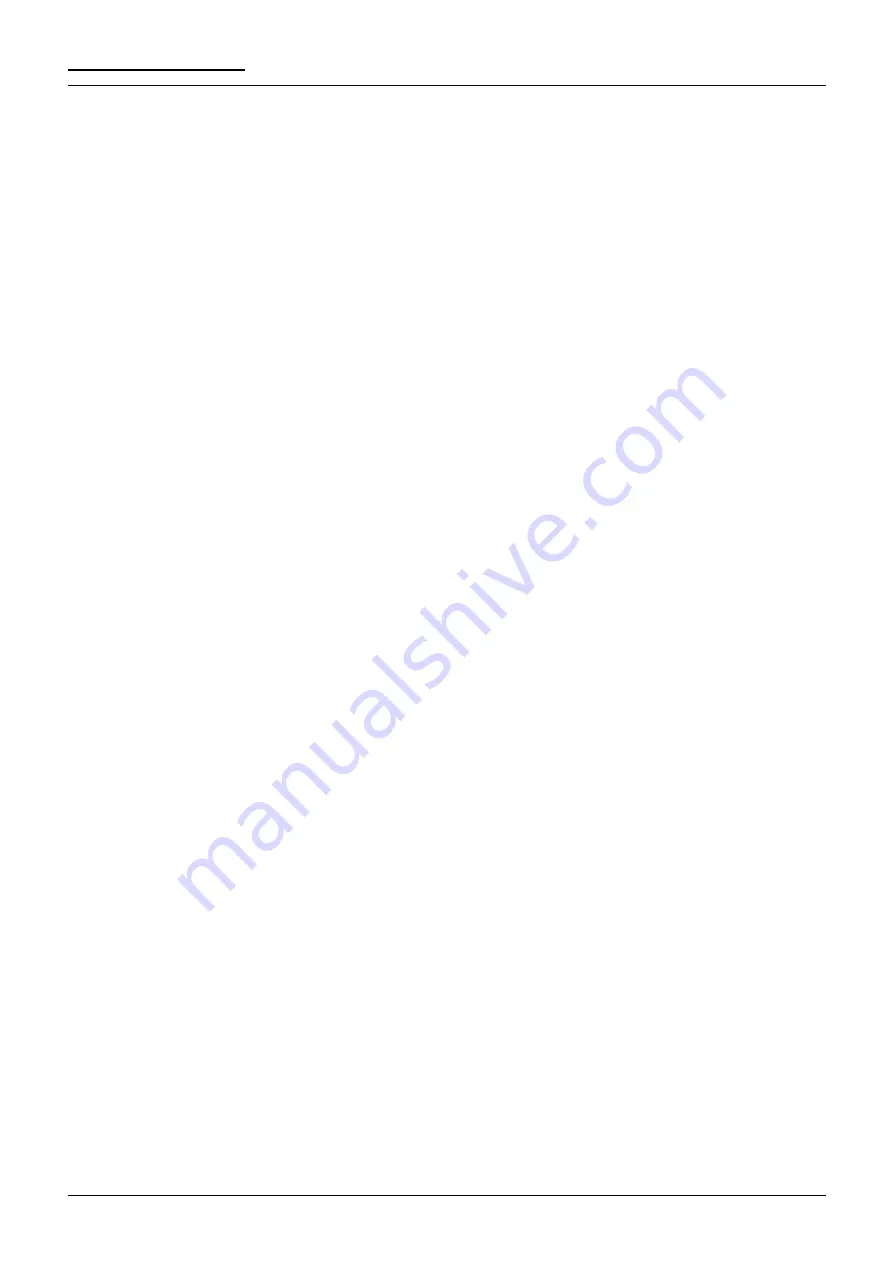
17/9/2013
KEN DW 410
Ret til ændringer forbeholdes
General .............................................................................1
Safety/environment ...........................................................2
Technical description ........................................................3
Installation instructions ......................................................4
User instructions ...............................................................5
Program built-up................................................................6
Maintenance......................................................................7
General information about stainless steel....................................................7.2
-general information about stainless steel, continued..................................7.3
Instructions -keep the good corrosion resistance of the steel......................7.3
Removal of stains and discoloration on stainless surfaces. ........................7.4
Adjustments by computer control ......................................8
Service Menu - detergent consultant menu .................................................8.3
Other adjustments/inspection............................................9
Adjustment of Rinse aid pump.....................................................................9.1
Detergent consultant .........................................................10
Calibrating detergent by conductivity dosing ...............................................10.1
-calibrating detergent by condutivity dosing, continued ...............................10.2
Table of Contents
Summary of Contents for 59.480
Page 2: ......
Page 33: ......
Page 40: ...KEN DW 412 Section page 17 1 Subject to alterations 17 9 2013 Diagrams ...