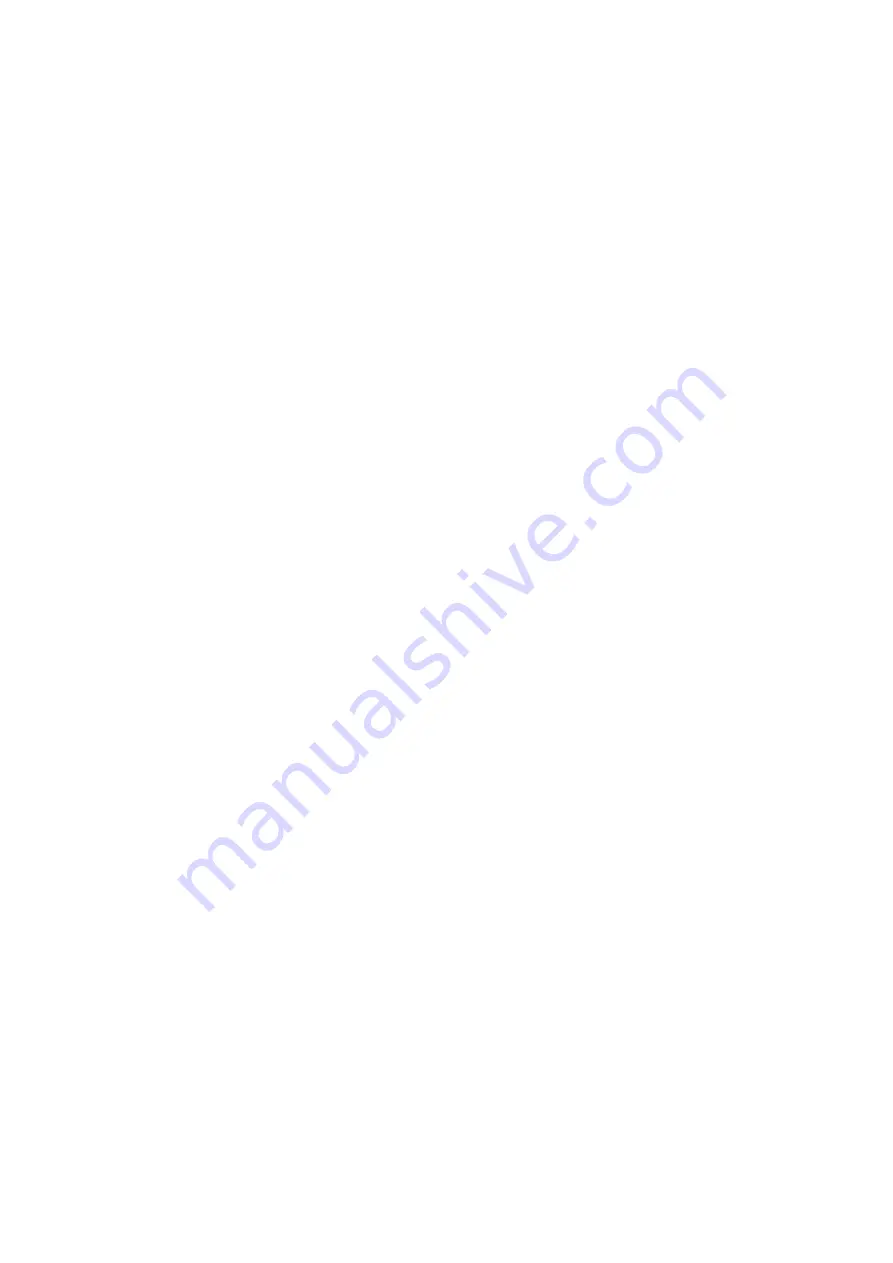
11
PBJ_N-SH-e-1810.docx
4
Basic Information (General)
4.1 Proper use
The balance you purchased is intended to determine the weighing value of material to be
weighed.
It is intended to be used as a “non-automatic balcance”, i.e. the material to be
weighed is manually and carefully placed in the centre of the weighing pan.. As soon as a
stable weighing value is reached the weighing value can be read.
4.2 Improper Use
Do not use balance for dynamic add-on weighing procedures, if small amounts of goods to be
weighed are removed or added.
The “stability compensation“ installed in the balance may
result in displaying an incorrect measuring value! (Example: Slowly draining fluids from a
container on the balance.)
Do not leave permanent load on the weighing pan. This may damage the measuring system.
Impacts and overloading exceeding the stated maximum load (max) of the balance, minus a
possibly existing tare load, must be strictly avoided. Balance may be damage by this.
Never operate balance in explosive environment. The serial version is not explosion
protected.
The structure of the balance may not be modified. This may lead to incorrect weighing results,
safety-related faults and destruction of the balance.
The balance may only be used according to the described conditions. Other areas of use
must be released by KERN in writing.
4.3 Warranty
Warranty claims shall be voided in case
Our conditions in the operation manual are ignored
The appliance is used outside the described uses
The appliance is modified or opened
Mechanical damage or damage by media, liquids, natural wear and tear
The appliance is improperly set up or incorrectly electrically connected
The measuring system is overloaded
Summary of Contents for PBJ-N
Page 4: ...PBJ_N SH e 1810 docx 4 ...
Page 40: ...PBJ_N SH e 1810 docx 40 Fig 7 Fig 8 ...
Page 47: ...47 PBJ_N SH e 1810 docx Fig 22 Fig 23 ...
Page 55: ...55 PBJ_N SH e 1810 docx 23 Drawing Fig 31 ...
Page 56: ...PBJ_N SH e 1810 docx 56 ...
Page 57: ...57 PBJ_N SH e 1810 docx Fig 33 ...