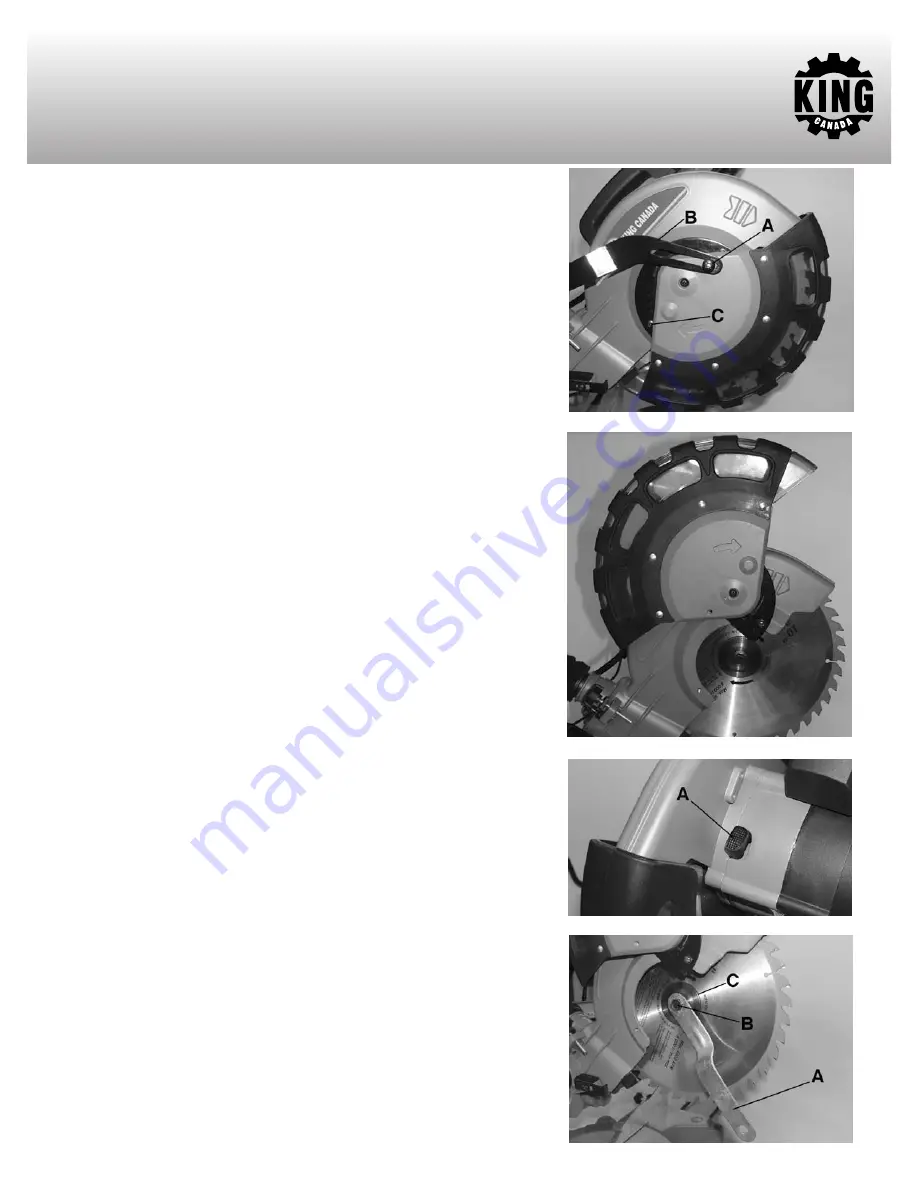
REPLACING/INSTALLING BLADE
REPLACING/INSTALLING BLADE
DANGER!
• Never attempt to use a blade larger than the stated capacity of the saw (10”). It
will come into contact with the blade guards.
• Never use a blade that is too thick to allow the outer blade flange to engage with
the flats on the spindle. It will prevent the blade screw from properly securing the
blade on the spindle.
• Do not use this saw to cut metal or masonry.
1. Make sure that the power cord is removed from the main power supply.
2. Push down on the saw arm and pull and turn the saw head release knob to
disengage the saw head.
3. Raise the saw head to its highest position.
4. Unscrew and remove large screw (A) Fig.18, and move the blade guard pivot
link arm (B) out of the way. Unscrew and remove pan head screw (C) which
fixes the guard plate and lower blade guard to the upper blade guard.
5. Once pan head screw (C) is removed, swing the guard plate and lower blade
guard upwards to allow access to the blade bolt as shown in Fig.19.
6. Completely depress the spindle lock button (A) Fig. 20 using one hand. Rotate
the blade by hand until the spindle locks.
7. Use the blade wrench (A) Fig.21 supplied to remove the blade bolt (B), loosen
in a clockwise direction as the blade bolt has a left hand thread.
8. Remove the outer blade flange (C) and the blade.
9. Wipe a drop of oil onto the inner and outer blade flanges.
10. Fit the new blade onto the spindle, make sure that the blade has the
appropriate arbor size (5/8”) and that the inner blade flange sits properly
behind the blade.
CAUTION:
Always install the blade with the blade teeth pointing downwards. The
direction of the blade rotation is also stamped with an arrow on the upper blade
guard.
11. Reposition the outer blade flange.
12. Depress the spindle lock, reposition and secure the blade bolt using the blade
wrench. Tighten the blade bolt in a counterclockwise direction as the blade bolt
has a left hand thread.
13. Reposition the lower blade guard and guard plate and secure the guard plate with
pan head screw and large screw removed in step 4.
Figure 18
Figure 19
Figure 20
Figure 21