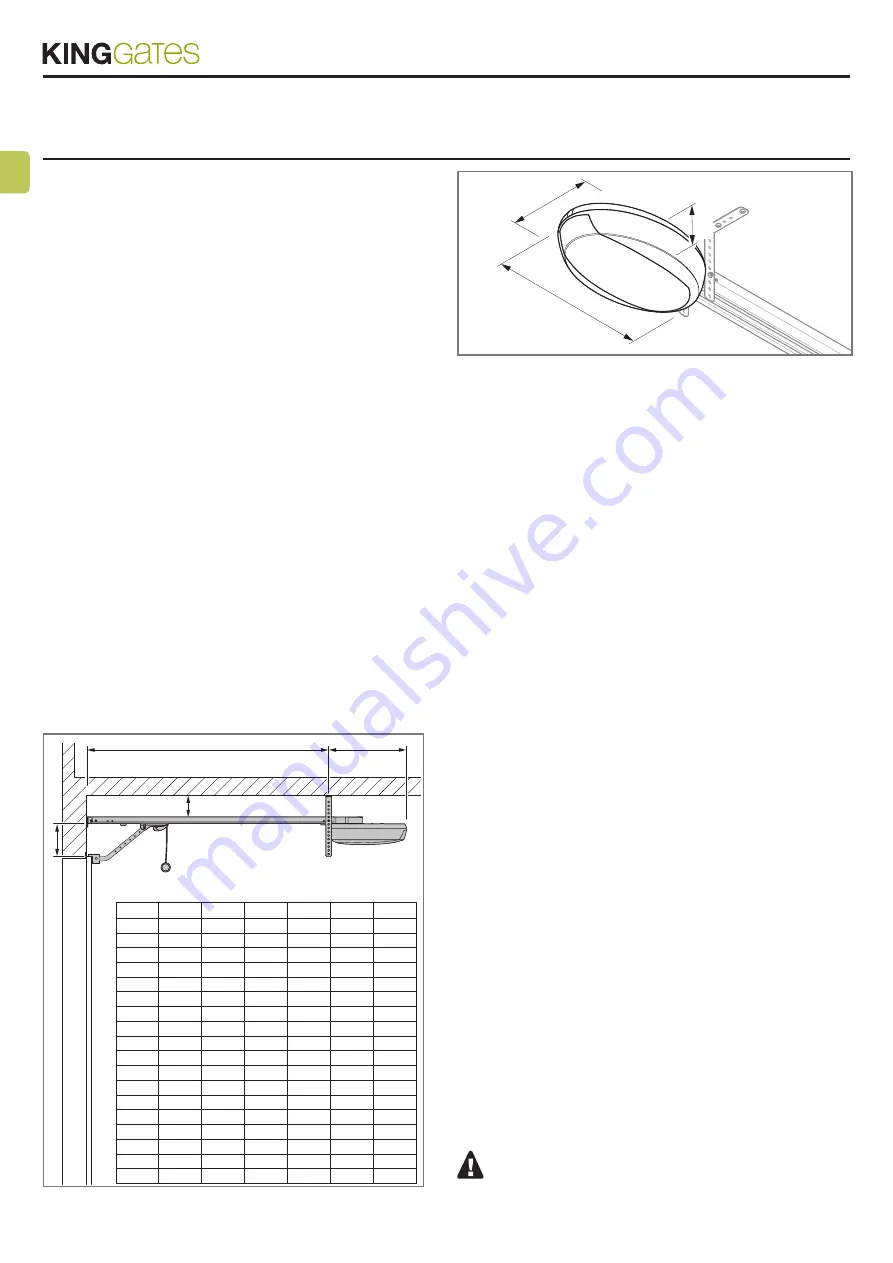
34
EN
3.
Installation
414
264
110
3
• Check and ensure that the manual release is fitted at a maximum
height of 1.8 m.
• Components must never be immersed in water or other liquids.
• Keep all ROLLS components away from heat sources and open
flames; these could damage the components and cause malfunc-
tions, fire or dangerous situations.
• If the door includes an access door, make sure that it does not
obstruct normal travel. Fit a suitable interlock system if necessary.
• Only insert the ROLLS plug into sockets equipped with a safety
grounding system.
• The socket must be protected by suitable magneto-thermal and
differential switches.
3.2 -
Fitting ROLLS
The installation of the ROLLS gearmotor comprises 3 stages:
• Assembly of the GRB23, GRB4 and GRB3 guides (see sections
3.2.1 and 3.2.2).
• Mounting the gearmotor to the guide (see section 3.2.3).
3.2.1 - Assembly of guide supplied GRB23
The guide that is supplied with GRB23 must be assembled as fol-
lows:
01.
Referring to
fig. 4
, remove the belt tensioner device (
4a
); insert
one end of the belt into the pulley (
4b
); reintroduce the belt tensioner
device into the guide (
4c
).
02.
Pass the same end of the belt through the head [A], as in
fig. 5
.
NB - Make sure that the belt is correctly positioned: it must be with the
teeth facing inwards, straight and without twists.
03.
Turn the lower section of the carriage so that the grooves corre-
spond with the two ends of the belt, as in
fig. 6
.
04.
Place both ends of the belt into all the shaped slots of the lower car-
riage [B]. Fix the ends of the belt using the appropriate 2 screws V4. 2 x
9.5 and the 2 R05 washers, as in
fig. 7
.
05.
Fix the belt guide [C] to the upper carriage [D] with the V6x18
screw and relative M6 nut, as in
fig. 8
.
06.
Insert the upper carriage [D] into the lower carriage [B] and place
the entire carriage assembly inside the guide, as in
fig. 9
.
07.
Assemble the two pieces of the guide with the joint [E] and join
the two guides and the joint using the supplied fixings
fig. 10 and
11
.
08.
Carefully position the belt into the guide, making sure that it is
not twisted.
09.
Push the head [A] into the free end of the guide using significant
force, as in
fig. 12
.
10.
Finally, tension the belt with the adjustment screw [F] of the belt
tensioner device, As in
fig. 13
.
WARNING! The gearmotor could break if the belt is TOO
taut, and it could cause unpleasant noise if it is TOO slack.
[F] (fig. 13).
The installation of ROLLS must be carried out by qualified person-
nel in compliance with current legislation, standards and regulations,
and the directions provided in this manual.
3.1 -
Preliminary checks
Before proceeding with the installation of ROLLS you must:
• Verify and ensure that, after installation, no door parts obstruct
public roadways or pavements.
• Check that all the materials are in excellent condition, suitable for
use and that they conform to the standards currently in force.
• Make sure that the structure of the gate is suitable for automation.
• Make sure that the force and dimensions of the door fall within the
specified operating limits provided in chapter 2.1 (“Operating limits”).
• Check that the static friction (that is, the force required to start the
movement of the leaf) is less than half the “maximum torque”, and
that the dynamic friction (that is, the force required to keep the leaf
moving) is less than half the “nominal torque”. Compare the resulting
values with those specified in section 17 (“Technical specifications”).
The manufacturer recommends a 50% margin on the force, as un-
favourable climatic conditions may cause an increase in the friction.
• Make sure that there are no points of greater friction in the opening
or closing travel of the door.
• Make sure that the mechanical stops are sturdy enough, and that
there is no danger of the door derailing.
• Make sure that the door is well balanced: it must not move by itself
when left stationary in any position.
• Make sure that the mounting positions of the various devices (pho-
tocells, keys, etc.) are protected from impact and that the mounting
surfaces are sufficiently sturdy.
• Make sure that the minimum and maximum clearances specified in
fig. 2
and
3
are complied with.
F1
A (cm)
0
2
4
6
8
10
12
14
16
18
20
22
24
26
28
30
32
34
F1
244
244
244
245
245
F2
240
240
240
241
241
242
243
245
F3
236
236
236
237
237
238
239
240
241
243
245
F4
232
232
232
233
233
234
234
235
237
238
239
241
244
F5
228
228
228
229
229
230
230
231
232
233
235
236
238
240
243
F6
224
224
224
225
225
225
226
227
228
229
230
231
233
234
236
239
241
245
F2
F3
F4 F5
F6
2
C
2875 mm
D
414 mm
B
0÷400 mm
A
The values in the table refer to the useful stroke on the guide when
the values of “
A
” and hole “
F
” used, vary.