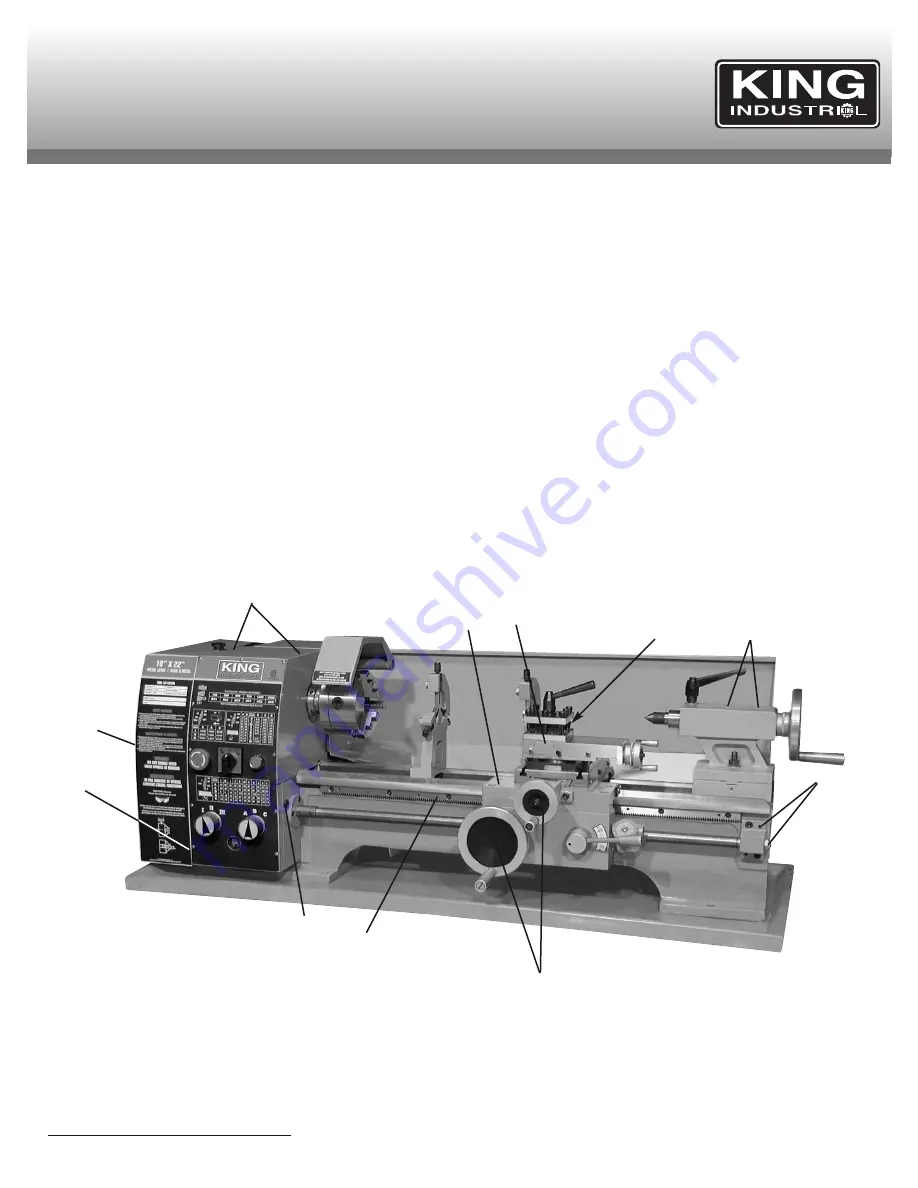
LUBRICATION POINTS
Before operating the metal lathe,
check the oil level and lubricate all sliding surfaces such as the half nut, worm gear, feed rod, handle rod,
tailstock quill before and after operating. Follow the main lubrication points illustrated below.
Lubrication Notes
Note: After running for the first 3 months, change the gear box oil (20W Machine Oil). Change oil once a year after first initial oil change. Remove
set screw on left side of gear box and drain oil, replace set screw. To fill gear box with oil, remove set screw on right side of gear box and pour
oil into gear box until it reaches the 3/4 mark on the oil level indicator.
Lubrication Points
Headstock lubrication points (1).
Gear Box lubrication points (2 & 3).
Gear Change lubrication points (4). Oil nipples and grease gears.
Saddle lubrication point (5).
Handwheel lubrication points (6).
Feedscrew & Bracket lubrication points (7).
Tailstock lubrication points (8).
Tool Post Slide lubrication point (9).
Top slide lubrication points (10). (Behind Tool Post)
Rack lubrication (11). Grease.
A light oil should be used on the bedway and all other reflective parts such as the tailstock quill.
9
10
8
7
6
11
4
5
1
3
2
FIGURE 20
PARTS DIAGRAM & PARTS LISTS
Refer to the Parts section of the King Canada web site for the most updated parts diagram and parts list.