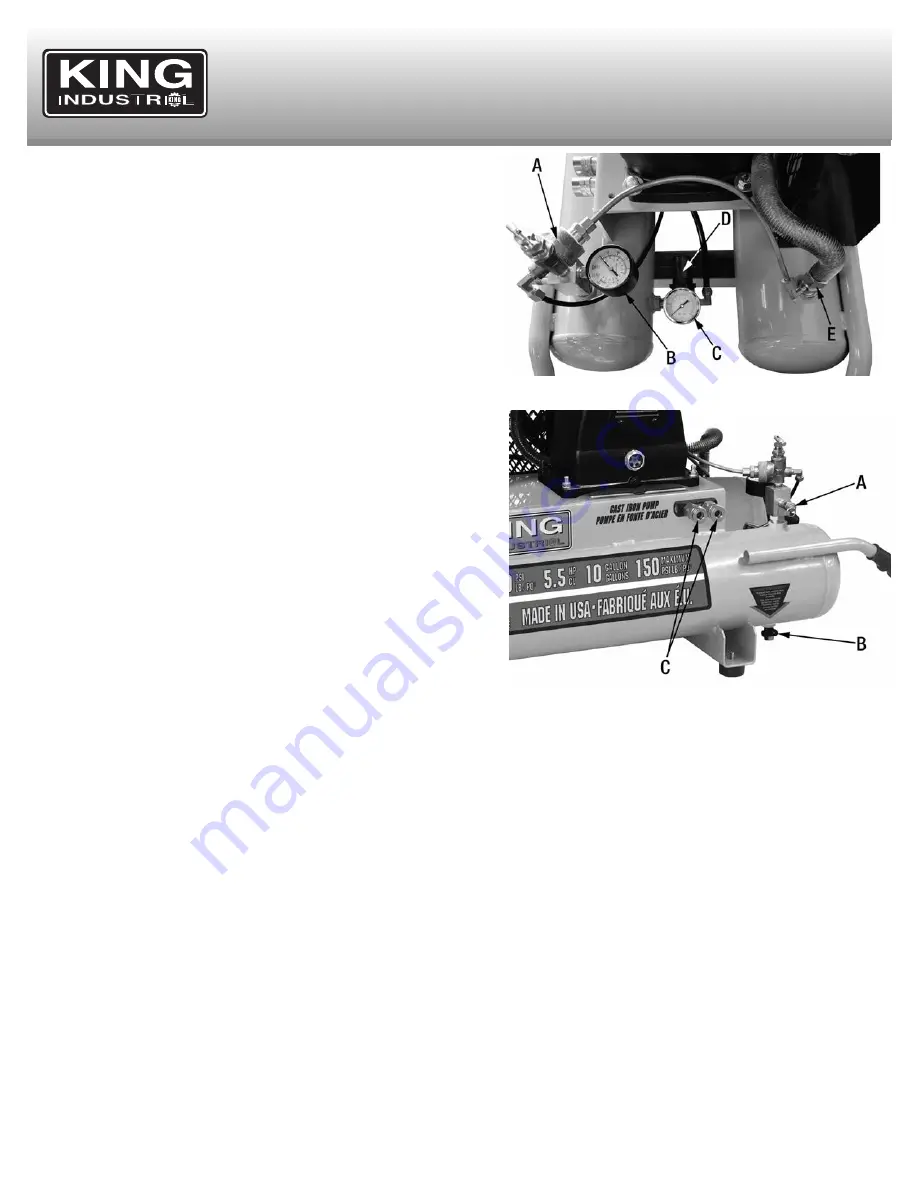
COMPRESSOR CONTROLS
FIGURE 4
FIGURE 5
ADDITIONAL REGULATORS AND CONTROLS
Since the air tank pressure is usually greater than that which is needed, an
air pressure regulator is employed to control the air pressure ahead of any
individual driven device. Separate air transformers which combine the
function of air regulation, moisture and dirt removal should be used where
applicable.
OPERATION CONTROLS
THROTTLE UNLOADER (A) FIG.4.
The throttle unloader automatically
slows down the engine to idle speed when the air tank pressure reaches the
factory set “Cut-Out” pressure (maximum pressure). When the tank pressure
drops below the factory set “Cut-In” pressure, the engine will automatically
accelerate and the compressor will pump additional air into the air tanks.
TANK PRESSURE GAUGE (B) FIG.4.
The tank pressure gauge indicates
the reserve air pressure in the air tanks.
OUTLET PRESSURE GAUGE (C) FIG.4.
The outlet pressure gauge
indicates the air pressure available at the outlet side of the regulator. The
pressure is controlled by the regulator and is always less than or equal to the
tank pressure.
REGULATOR (D) FIG.4.
The air pressure coming from the air tanks is
controlled by the regulator. To unlock the regulator, pull it outwards then turn
the regulator knob clockwise to increase pressure or counterclockwise to
decrease pressure. To avoid minor readjustment after making a change in the
pressure setting, always approach the desired pressure from a lower
pressure. When reducing from a higher to a lower setting, first reduce the
pressure less than that desired, then bring it up to the desired pressure.
Depending on the air requirements of each particular accessory, the outlet
regulated air pressure may have to be adjusted while operating the accessory.
ASME SAFETY VALVE (A) FIG.5.
The safety valve protect against
overpressurization by “popping out” at its factory set pressure of 150 PSI.
WARNING!
: If the safety valve does not work properly, over pressurization
may occur, causing air tank rupture or an explosion. Daily pull the ring on the
safety valve to make sure that the safety valve operates freely. If the valve is
stuck or does not operate smoothly, it must be replaced with an identical 150
PSI ASME approved safety valve.
CHECK VALVE (E) FIG.4.
When the air compressor is operating, the check
valve opens, allowing compressed air to enter the air tanks. When the air
compressor reaches its “Cut-Out” pressure, the check valve closes, allowing
air pressure to remain inside the air tanks.
DRAIN VALVES (B) FIG.5 (1 OF 2).
The drain valves are located underneath
each end of the air tanks and are used to drain condensation at the end of
each use. Turn drain valve counterclockwise to open (no tank pressure build-
up) or clockwise to close it (pressure build-up).
1/4” QUICK CONNECT COUPLERS (C) FIG.5.
These 1/4” universal “one
touch” quick connect couplers allow user to connect up to 2 air hoses to
operate 2 air tools.