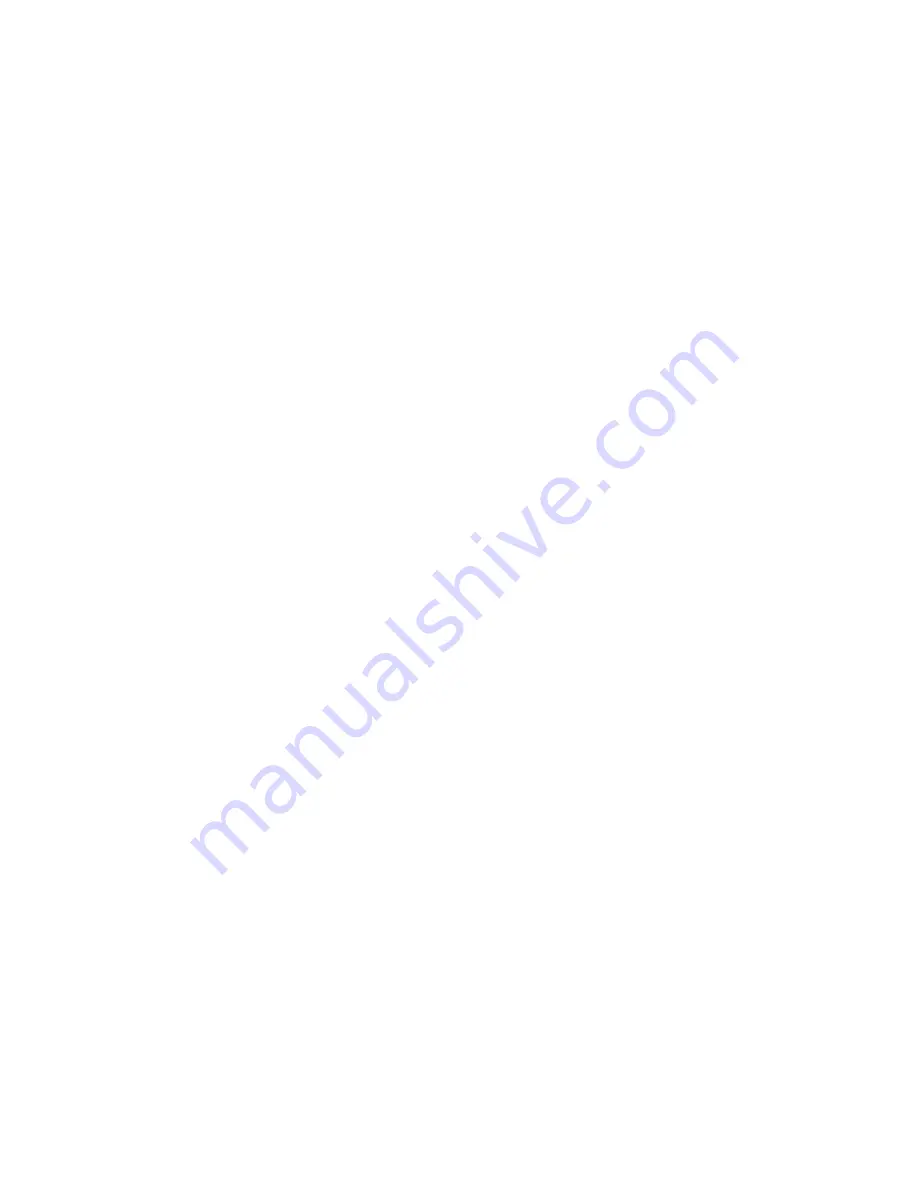
13
※
6. Before operation, always check the sonic wave to ensure the resonance between the
vibration system and oscillator, especially after the welding head is replaced or the
amplitude is changed.
(5) Mold Adjustment Procedure
To acquire the largest throughput, the distance between the welding head and the
work-piece should be as short as possible, but a sufficient space is required for the
placement and removal of the work-piece. Since the maximum stroke of the welding head
is 100 mm, make sure the work-piece will not touch the welding head when it reaches its
maximum stroke. The mold adjustment steps are described as follows:
1. Set the selector switch to the Manual position and turn the pressure governor to
maintain the minimum pressure that can raise the cylinder.
2. Place the work-piece on the base.
3. Release the fixed handles with your left hand. Turn the hand wheel to keep the distance
between the welding head and the work-piece more than 100mm (the max. stroke of the
welding head). Tighten the fixed handles.
4. Push the operator push buttons with both hands to drop the welding head.
5. Loosen the fixed screws and rotate the welding head to align with the work-piece. Then
rotate the hand wheel to drop the welding head to touch the work-piece. Finally, drop
the body of the machine by about 5mm-10mm.
6. Turn the pressure governor to increase the pressure (higher than 3kg/cm
2
). Tighten the
fixed screws in a diagonal sequence (Do not completely tighten the screw on any side at
one time). Then tighten the fixed nuts.
7. Tighten the fixed handles of the large column and screw the fixed screws of the base.
8. Push the emergency rise button to raise the welding head and rotate the stopper screw
so that it and the vibrating cylinder will not touch each other during the operation.
When there is no work-piece on the base, the stopper screw can stop the vibrating
cylinder to prevent the welding head from touching the base and causing damage.
Note:
1. The mold adjustment procedure described above is only for rough
adjustment. When precise mold adjustment is required, observation and
adjustment should be made carefully during the trial period. Or place carbon
paper and white paper between the welding head and work-piece. An
indentation will appear on the white paper. Then adjust the height of the base
depending on the depth of the indentation to ensure even exertion of force on
the work-piece.
2. Place copper plates with different thicknesses between the base and the
foundation to adjust the height of the base and make the work-piece align
with the welding head.
Remarks:
The ultrasonic plastic processing is affected by the following factors:
1. Design of the contact or joint face
2. Design of the energy conducting point