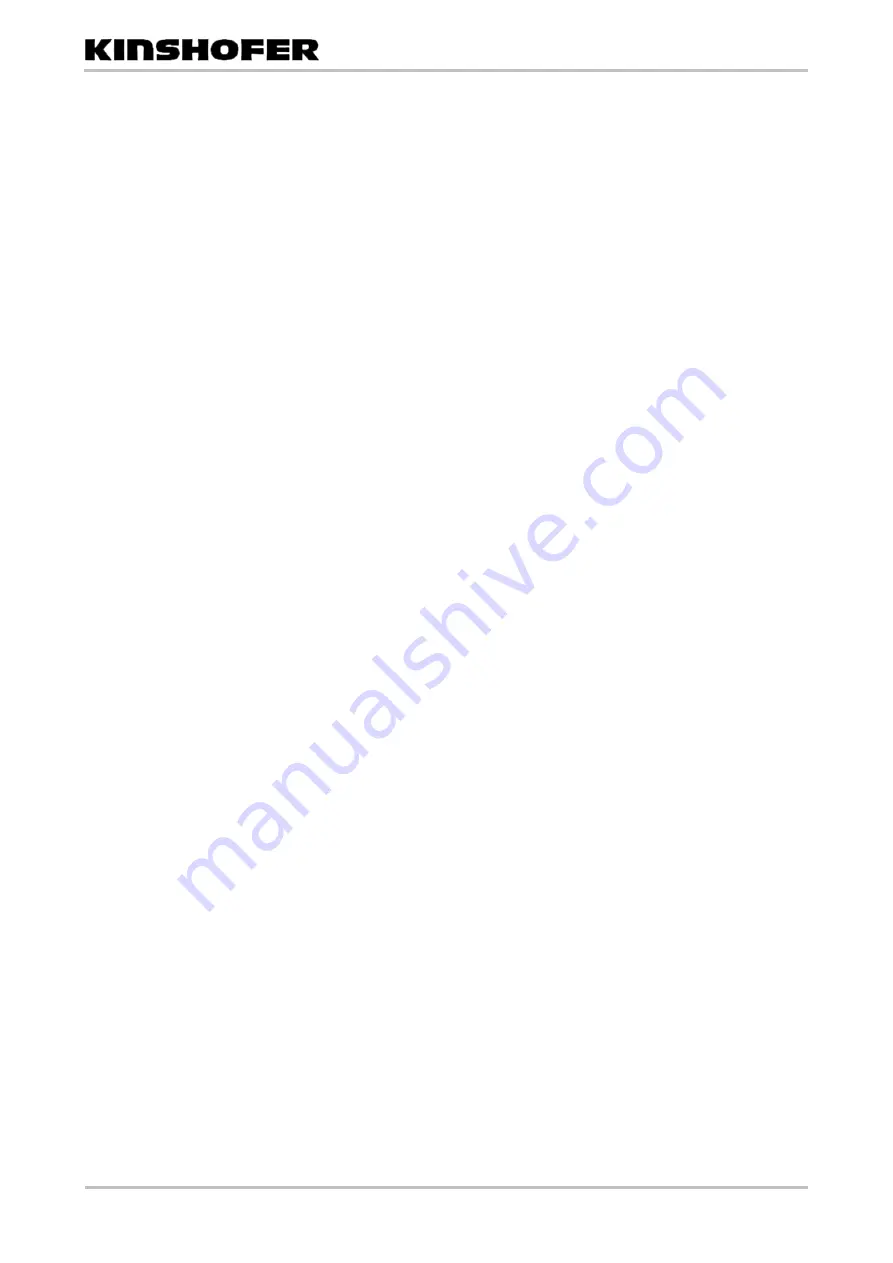
Important notes
8
01.04.2020
1.2.2.
Safety guidelines for controls
European Directives
Directive 2006/42/EC
Directive 2004/108/EC (EMC)
DIN EN ISO 12100 Safety of machines –
General principles for design
DIN EN 60204-1 Safety of machines -
Electrical equipment of machines, Part 1: General requirements
DIN EN ISO 13849-1 Safety of machines -
Safety-related parts of control systems
ISO 13031 Earth-moving machinery - Quick couplers - Safety
1.3.
Package consists of
The following components are included in the delivery:
•
Terminal
•
Joystick grips with additional parts
•
Cab module
•
NOX module
•
Cable loom:
•
Jib cable
•
2x Joystick cable
•
Cable for pressure reduction valve
•
2x Cable for analogue pressure reduction valve
•
CAN distributor
•
NOX cable
•
Pressure reduction valve
•
USB stick with software
•
USB OTG cable
•
Micro USB cable
•
Cable ties
•
Fuse holder with 15A fuse
•
RAM Mount
•
Adhesive and cleaning cloth
1.4.
Personnel qualifications
Unqualified personnel cannot recognise risks and are therefore exposed to a
higher level of danger.
Only trained personnel may be tasked with the activities described in these
installation instructions.
The operating company must ensure that the personnel comply with the locally
applicable rules and regulations for safe and hazard-free work.
The responsibility for tasks must be stipulated and made known by the operating
company.
These installation instructions are aimed at the following target groups:
•
Kinshofer service personnel
•
Certified partner's workshop personnel
Personnel who carry out the installation and commissioning work.
Personnel who carry out the installation and commissioning work. They are
professionally trained and have successfully completed manufacturer's training.
EC
DIN EN ISO
Service personnel
Manufacturer
Certified partner's
workshop personnel