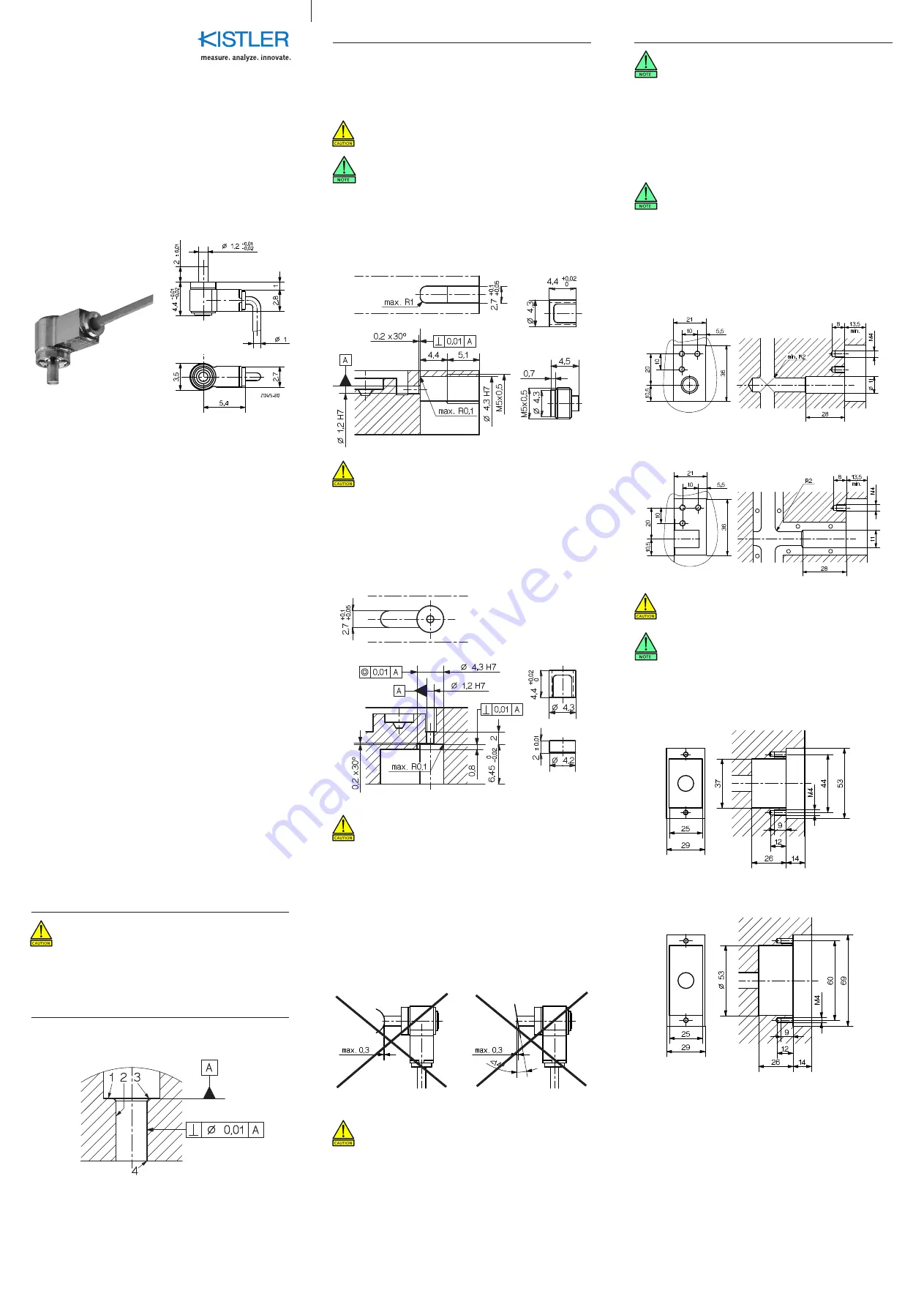
Observe radii
•
Cover open channel to prevent cable damage
•
3. Hole
3.1 Unmachined Sensor
For use in flat cavity wall with sensor fitted at right angles
to cavity.
Hole and thread must be free of debris and shav-
•
ings
Use checking tool Type 1365, also to lapp hole
•
Quick Start Installation
1,2 mm Mini Cavity Pressure Sensor with Chrome-plated
Front
Type 6184AC… (–1,2 pC/bar, 2 000 bar, 200 °C)
6184A_002-504e-07.09
Content
Front Page: Machining the Mold
1. General Notes
2. Important Areas of Sensor Hole
3. Hole
3.1 Unmachined Sensor
3.2 for Cavity-Matched Sensor
4. Cable Channeling and Connector
Rear Page: Sensor Installation, Service and Repair
5. Installing Sensor
6. Installing Cable and Connector
7. Installing Identification Plate
8. Functional Test
9. Service and Repair
Foreword
Information in this document is subject to change without
notice. Kistler reserves the right to change or improve its
products and make changes in the content without obliga-
tion to notify any person or organization of such changes or
improvements.
To the extent permitted by law Kistler does not accept any
liability if this quick start installation is not followed or prod-
ucts other than those listed under Accessories are used.
© 2009, Kistler Group. All rights reserved.
1. General Notes
Sensor ø3,5 mm may not be machined
•
Front of sensor must be clean and without notches
•
Only use recommended installation accessories
•
Do not use cable to pull sensor out of hole
•
1. Sensor contact surface must be flat and perpendicular
2. Hole with H7 tolerance to center sensor
3. Chamfer to assist installation
4. Sharp edges reduce witness mark on part
3.1.1 Sensor with Mounting Nut Type 6465
Electrical discharge machine (EDM), mill or precision grind H7
hole in hardened tool steel. Check centering and alignment.
Clean thread of debris and shavings.
2. Important Areas of Sensor Hole
Note the following critical installation criteria:
Always use spacer sleeve Type 6466
•
3.1.2 Sensor with Thrust Washer Type 6470
EDM, mill or precision grind H7 hole in hardened tool steel.
Check centering and alignment. Clean thread of debris and
shavings.
Always use spacer sleeve Type 6466
•
3.2 Cavity-Matched Sensor
This sensor have a chrome-plated front surface.
This sensor may not be machined.
All liability and warranty claims become void in the case of a
sensor whose front has been machined.
4.1.1 Single-Wire Cut and Grip Connector Type 1839
Machine cable channel and recess for mounting plate.
Example shown: Drilled hole
This sensor may NOT be machined
•
4. Cable Channeling and Connector
Fixed cable reduces mounting
•
Do not run cables next to hot runner cartridge
•
Chamfer all sharp edges
•
Cover open channels/slots
•
4.1 Single-Wire Cable Technology
The single-wire technology uses the tool steel to ensure elec-
trical shielding of the sensor signal. Thus the wiring is routed
through drilled holes or channels.
Single-wire cable must be completely enclosed in mold
•
Single-wire cable must not be routed with power
•
cables
4.1.2 Multichannel Single-Wire Connectors
Recess for 4-channel connector Type 1708A…
Recess for 8-channel connector Type 1710A…
Example shown: Channel