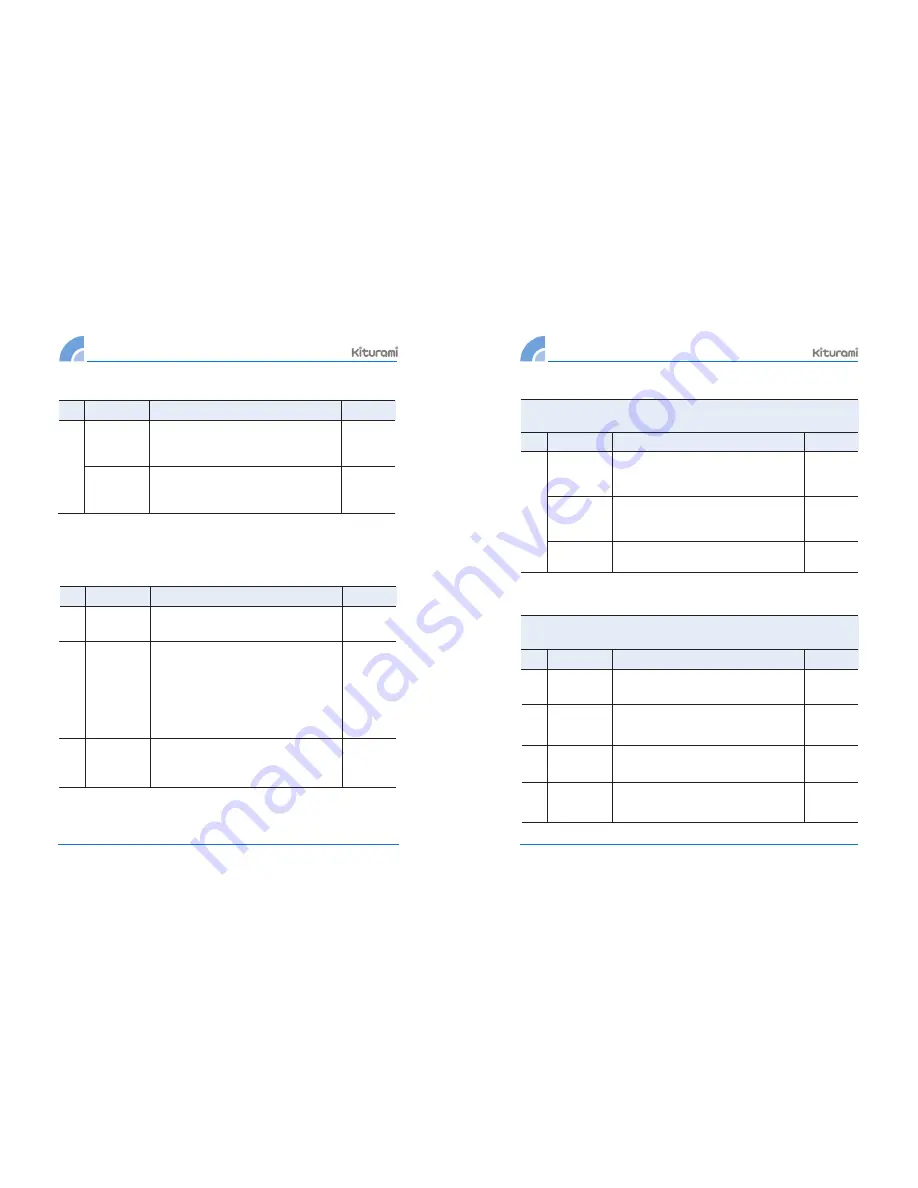
22
04
05
▶
08
06
07
▶
Troubleshooting
Trouble: Disconnection of temperature sensor and overheat sensor
No
Failure
Troubleshooting
Remarks
No
Failure
Troubleshooting
Remarks
Trouble: Defective transmission/reception
1. Water temp.
sensor
disconnected
2. Overheat
sensor
disconnected
1. Blower RPM
not detected
2. Low limit,
High limit
3. Defective
transmission/
reception
①
Check the water temperature sensor for
correct connection.
②
Check the wiring for damage.
③
Replace the temperature sensor.
①
Check the overheat sensor for correct
connection.
②
Check the wiring for damage.
③
Replace the temperature sensor.
①
Check the wiring of the blower for
damage.
②
Replace the blower.
①
The RPM of the blower is too low or too high due to foreign
materials caught on the blower housing
②
Too high RPM of the blower or the exhaust may be caused by
strong wind when the flue is installed in the wind pressure zone
Contact the installation shop about changing the location of the
flue.
③
Remove condensate from the curved part of the flue, if any.
④
Contact your distributor or the after-sales service center.
①
Defective transmission/reception of the room controller and
the main controller: Ignition travel turned off
②
If the problem persists for more than ten minutes, Error 08
has occurred, and the power LED blinks.
③
Replace the room controller (automatic recovery).
Disassembled
part of burner
23
98
▶
96
▶
Troubleshooting
Trouble: Overheat error
Trouble: Triggering of the overheat sensor (bimetal) due to
counter-flow of flame
No
Failure
Troubleshooting
Remarks
No
Failure
Troubleshooting
Remarks
1) Symptom: Detecting water temperature higher than 93
℃
by the water temperature sensor/detecting
temperature higher than 92
℃
by the overheat sensor
2) Recovery: Automatic recovery upon water temperature lower than 88
℃
/overheat lower than 87
℃
1) Step 1: Temperature at the water temperature sensor lower than 10
℃
- Released when the circulation
pump operates at temperature higher than 12
℃
2) Step 2: Temperature at the water temperature sensor lower than 7
℃
- The circulation pump and the burner
start operation.
1. The circulation
pump
inoperable
2. The CH valve kept
lock to cause rapid
elevation of temp
erature
3. Controller
failure
Installing
detachable
pump
Installing the
boiler in the
boiler room
①
Check the circulation pump circuit of the coil.
The measurement result for a resistance of ‘0’
indicates normal operation; ‘infinite’ indicates a
circuit of the coil. Replace the circulation pump.
①
Check whether the distributor valve is locked;
if it is, open the locked valve.
①
The feed motor continues operating even
when the fuel feed is in the halting mode.
②
Replace the controller.
1. Fuel clogged
2. No Tee installed
on the flue causing
head wind
3. Fire tube
clogged
4. Poor air-tightness
of the fuel feed line
①
Clean the flue.
①
Install a Tee on the flue to prevent head wind.
①
Clean the fire tube of the boiler.
①
Poor air-tightness of the hoses and the pipes used
for feeding the fuel to the burner causes overheat
ing. Disassemble the band, check the air-tightness,
and reassemble the band.
Summary of Contents for KRP-20A
Page 14: ...26 Memo 27 Memo ...
Page 15: ...30 Memo ...