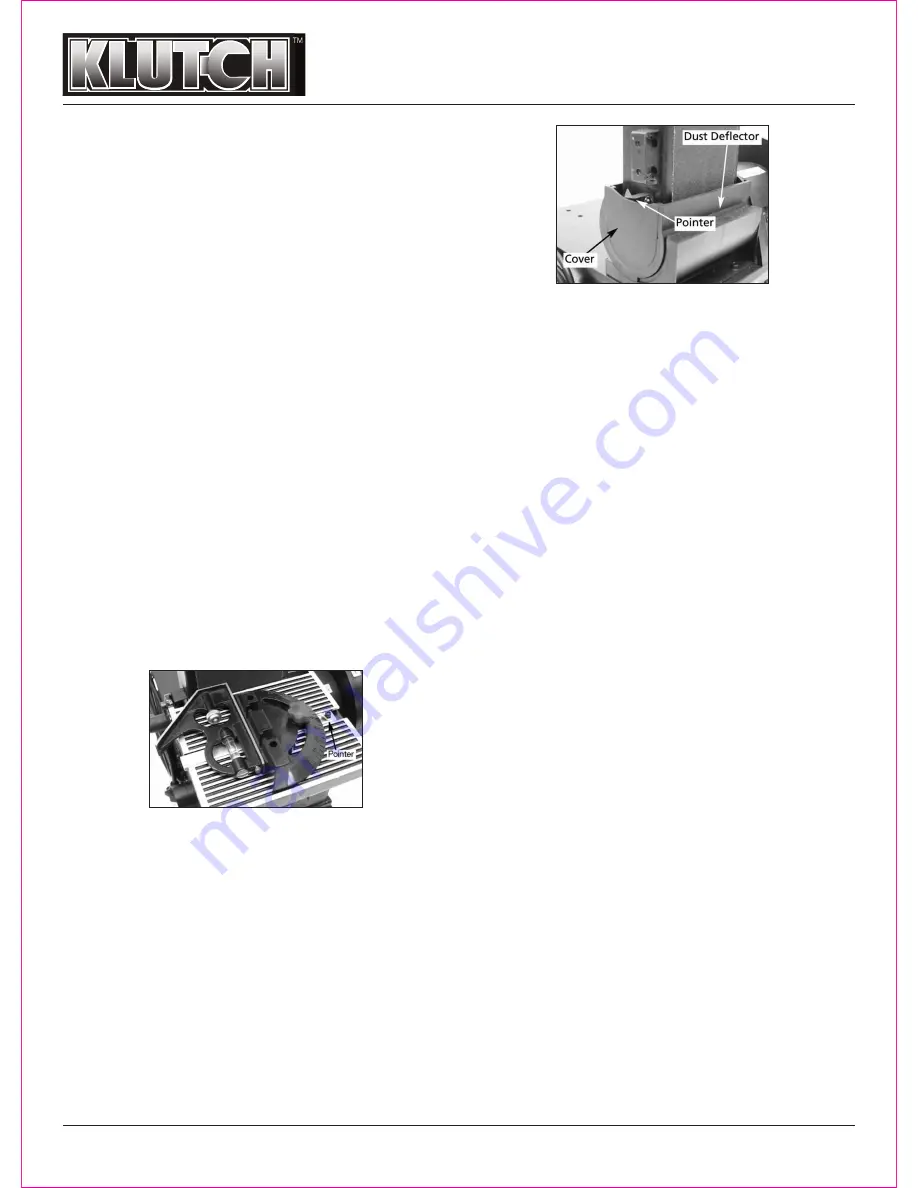
4IN. x 36IN. BELT/6IN. DISC SANDER
OWNER’S MANUAL
5 of 7
work being sanded. Keep end butted against back stop and
move work evenly across abrasive belt. Use extra caution
when finishing very thin pieces.
• Finishing curved edges: Finish outside curves on flat
por¬tion of abrasive belt. Finish inside curves on idler drum
por¬tion of abrasive belt.
• Finishing end grain: It is more convenient to finish ends of
long workpieces with the abrasive belt in a vertical position.
Position table on belt side of sander. Move work evenly
across abrasive belt. For accuracy, use miter gauge. Table
may be tilted for beveled work.
ABRASIVE DISC SANDING
• Abrasive disc sanding is well suited for finishing small flat
surfaces and convex edges.
• Move workpiece across down side (left) of abrasive disc.
Hold workpiece firmly with both hands; keep fingers away
from abrasive disc.
• Abrasive disc moves fastest and removes more material at
outer edge.
• For accuracy, use miter gauge.
USING MITER GAUGE
• Use the miter gauge for securing the work and holding the
proper angle while sanding.
• Use a combination square to adjust miter gauge square to
belt /disc.
• Pointer should be at zero. Loosen screw and reposition
Pointer if necessary.
After setting miter gauge square to belt (disc), adjust to
desired angle by repositioning the miter gauge scale and
locking it into place with knob.
ABBRASIVE BELT REPLACEMENT
• Remove the Table Assembly and Back stop.
• Remove the Pointer, then slide the Side Cover up and out
from the Dust Deflector.
• Release the Belt tension by pushing the Tension Lever
toward the Idler Drum. Slide the old Belt off of the Drive and
Idler Drums.
• Slide the new Belt over the Drive and Idler Drums; Center the
Belt on the Drums.
• Push the Tension Lever towards the Drive Drum to tension
the Belt.
• Check the Tracking.
• Assemble in reverse order.
ABBRASIVEDISC REPLACEMENT
• Remove table assembly.
• Remove disc cover by loosening and removing four screws.
• Remove old abrasive disc by peeling it from the aluminum
disc.
Removing aluminum disc is not necessary.
• Clean aluminum disc if necessary. Select the desired
abrasive disc and apply to aluminum disc.
• Replace disc cover
MAINTENANCE REQUIREMENTS
•
Consult manual for specific maintaining and adjusting
procedures.
Or ask for qualified repair personnel. Service or
maintenance performed by untrained personnel could result
in a risk of injury.
•
Store tools out of reach of children and other untrained
persons.
Tools are dangerous in the hands of untrained
users.
•
Maintain tools with care.
Keep cutting tools sharp and
clean.Properly maintained tools with a sharp cutting edge are
less likely to bind and are easier to control. Do not use a
damaged tool. Tag damaged tools “Do Not Use” until
repaired.
•
Always unplug tool prior to inspection.
•
Keep tool lubricated and clean for safest operation.
•
Remove adjusting tools.
It is importantto ensure that any
adjusting tools are removed before switching machine on.
• K
eep all parts in working order.
Check to determine that the
guard or other parts will operate properly and perform their
intended function.
•
Use a dust extractor unit for eliminating wood chips.
The
airflow rate at the suction connector must be 65.6ft/s
(20m/s).
•
When servicing a tool, use only identical replacement
parts.
Use of unauthorized parts or failure to follow mainte-
nance instructions may create a risk of electric shock or
injury.
•
Check for damaged parts.
Check for alignment of moving
parts, binding, breakage, mounting and any other condition
that may affect a tool’s operation.
•
A guard or other part that is damaged should be properly
repaired or replaced.
Do not perform makeshift repairs. (Use
parts list provided to order replacement parts.)