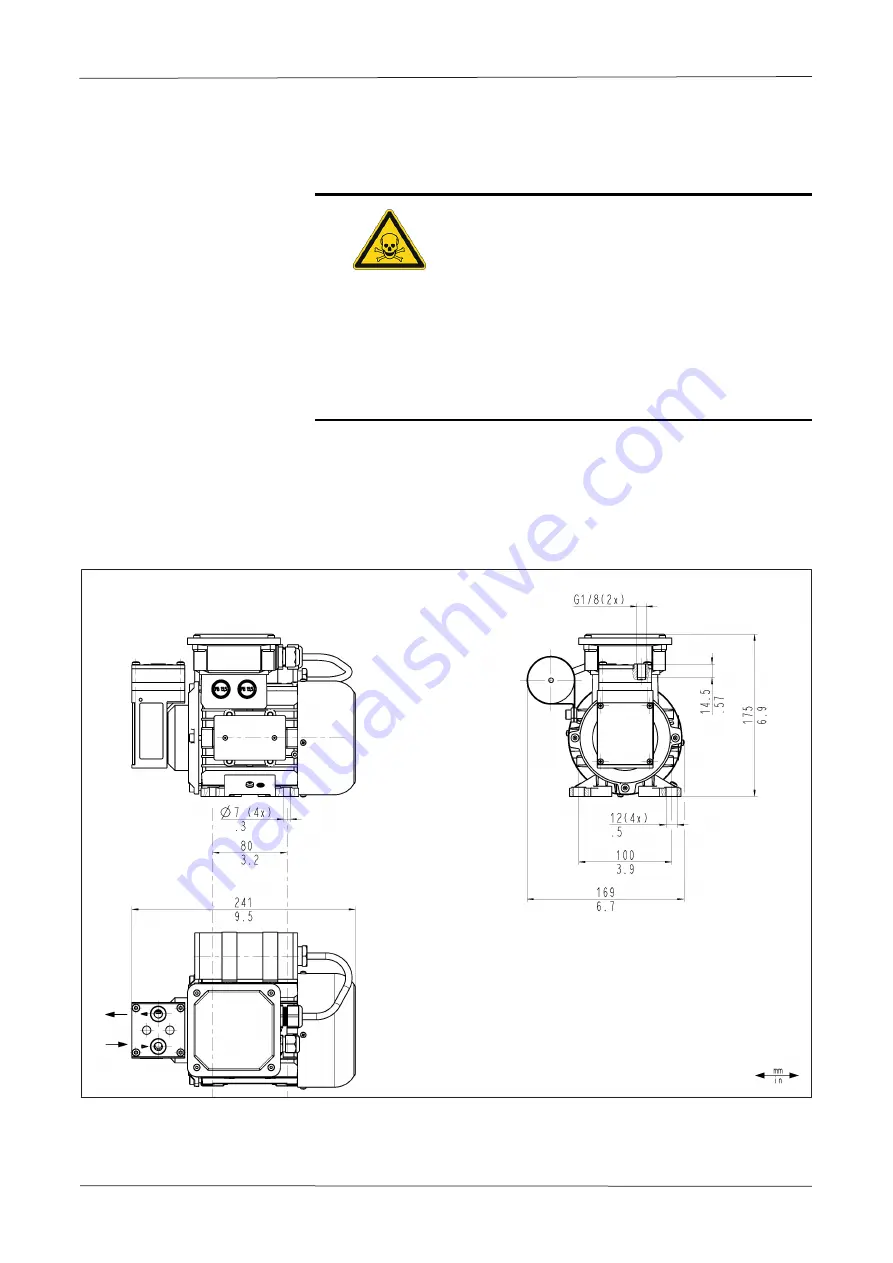
Installation and connection
Diaphragm pump N87.9 EX
18
Translation of Original Operation and Installation Instruction, english, KNF 323252 04/21
7 Installation and connection
The pumps are only to be installed in accordance with the operating pa-
rameters and conditions described in Chapter
à
Observe the safety notices (see Chapter Safety).
DANGER
Risk of dangerous gas mixtures during pump op-
eration
Depending on the medium being transferred,
breakage of the media-contacting components
can result in a dangerous mixture if the medium
mixes with the air in the compressor housing or
the surroundings.
à
Before using a medium, check the compati-
bility of the media-contacting components
(see
7.1 Installing the pump
à
Store the pump at the installation site prior to installation to bring it up
to the ambient temperature.
Mounting dimensions
à
For mounting dimensions, see the following illustrations:
Fig.3 Mounting dimensions N87 EX