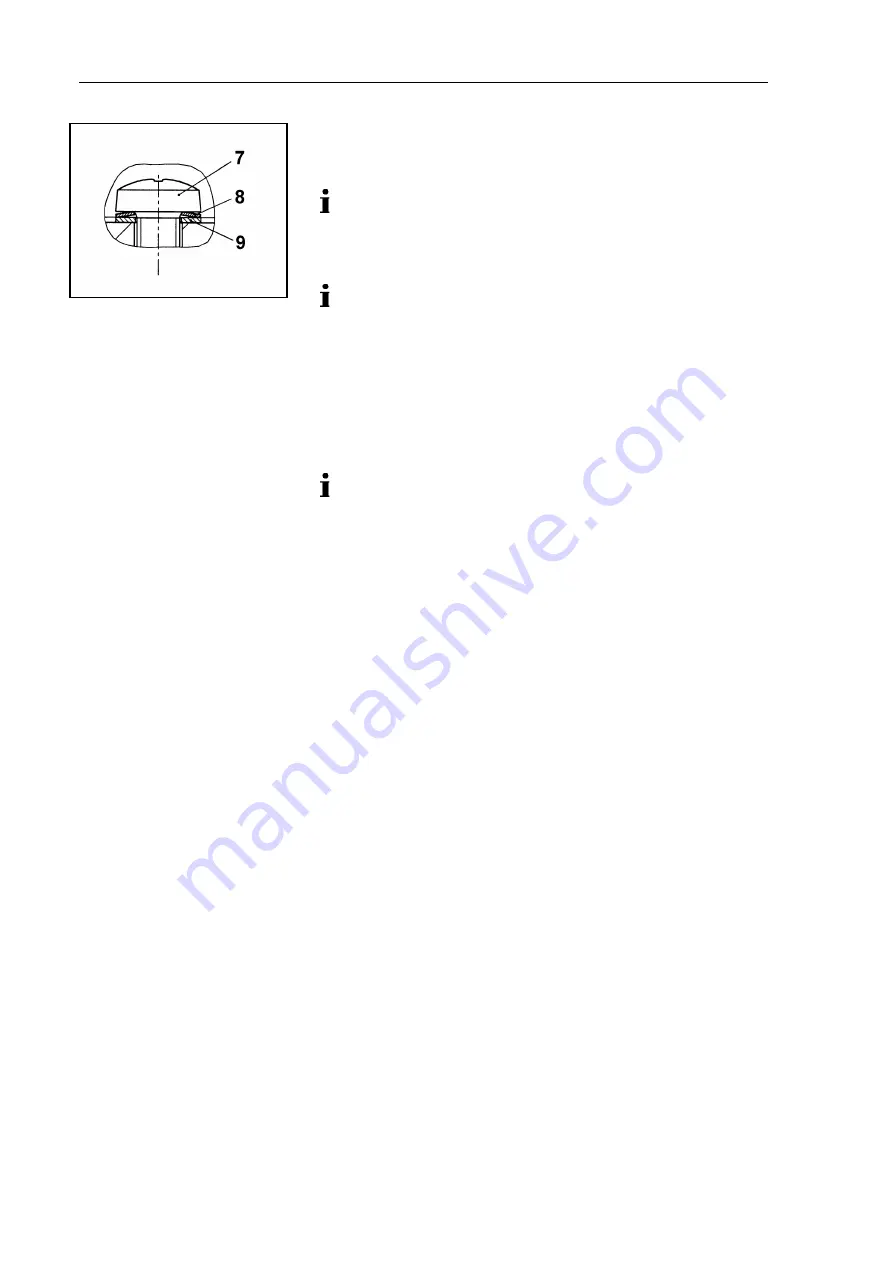
Servicing
Diaphragm Vacuum Pumps N 920__.18 and N 920 KT.29.18G
24
Translation of original Operating Instructions, English, KNF 121416-121419 07/18
Mount pump head
1. Place head plate (
10
) on intermediate plates (
11
), (
14
) and
(
15
) in the position indicated by the drawing lines.
At the front edge the three intermediate plates must lie in a
line on which head plate is placed flushly.
2. Tighten the three screws (
7
) of head plate (
10
) carefully slightly
hand-tight.
For position and orientation of disk spring (
8
) and washer (
9
)
of screw (
7
) see fig. 10.
3. Place head cover (
4
) on pump housing (
18
).
4. Tighten the nine screws (
3
) of head cover (
4
) slightly in the first
instance. Start with the screws of medium pump stage, then
tighten the screws on the right, at least these on the left.
5. Now, tighten the screws (
3
) firmly; tighten the center screws
first, then continue outward.
If the screws are stiff to turn, the intermediate plates do not
lie in a line at front edge, or intermediate plates and head
plate are not placed flushly (see step 1).
6. Remount the covers (
5
).
7. Remount pump handhold (
2
).
Final steps
1. Reconnect suction and pressure line to the pump.
2. Reconnect the pump to the electricity supply.
If you have any questions about servicing, call your KNF technical
adviser (see last page for contact telephone number).
Fig. 10: Posit ion and orient at ion
of disk (
8
) and washer (
9
) at
screw (
7
)
Summary of Contents for N920 AP.18
Page 2: ......
Page 30: ......
Page 31: ......
Page 32: ...KNF worldwide Please find our local KNF partners at www knf com ...