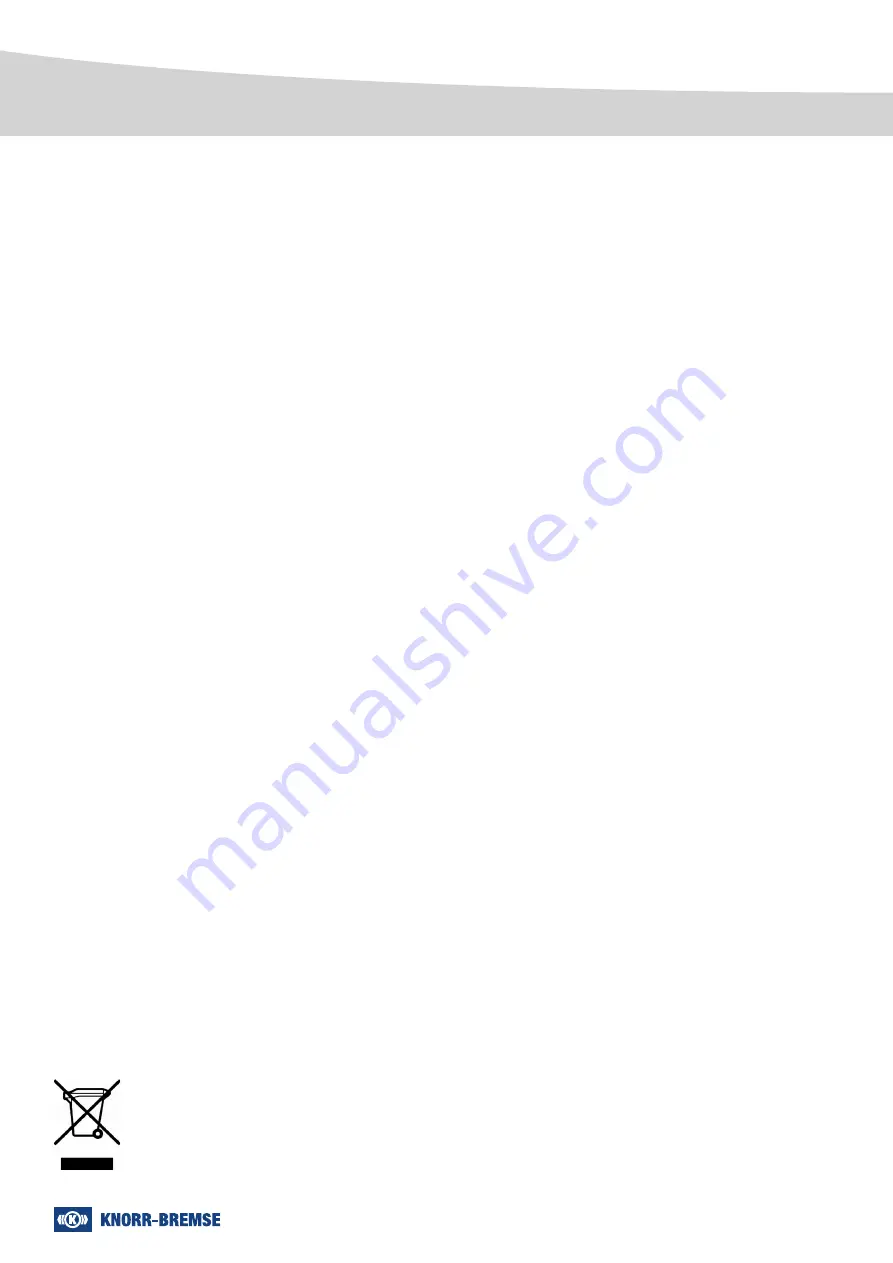
4
Safety and Environment Guidelines
Note: The safety advice listed below is applicable to general service and diagnostic work on braking systems. Also observe any recommendations from
the axle or vehicle manufacturer concerning towing, jacking-up and securing the vehicle.
Before and during working on or around compressed air systems and devices, the following precautions should be observed:
1
Always wear safety glasses when working with air pressure.
2
Never exceed the vehicle manufacturer’s recommended air pressures.
3
Never look into air jets or direct them at anyone.
4
Never connect or disconnect a hose or line containing pressure; it may whip as air escapes.
5
When removing or servicing a product, ensure all pressure related to the specific system it is contained in has been depleted to 0 bar. Be aware
that if the vehicle is equipped with an air dryer system, it can also contain air pressure along with its purge reservoir, if fitted, even after pressure has
been drained from the other reservoirs.
6
If it is necessary to drain the air pressure from reservoirs, etc., keep away from brake actuator push rods and levers since they may move as system
pressure drops. On vehicles fitted with air suspension, it is advised when undertaking such work, to support the chassis from sudden lowering and
therefore prevent any possibility of being trapped between the chassis and axle or ground.
7
Park the vehicle on a level surface, apply the parking brakes, and always chock the wheels as depleting vehicle air system pressure may cause the
vehicle to roll.
8
When working under or around the vehicle, and particularly when working in the engine compartment, the engine should be shut off and the ignition
key removed. Where circumstances require that the engine be running, EXTREME CAUTION should be taken to prevent personal injury resulting
from contact with moving, rotating, leaking, heated or electrically charged components. Additionally, it is advisable to place a clear sign on or near
the steering wheel advising that there is work in progress on the vehicle.
9
Examine all pipework for signs of kinks, dents, abrasion, drying out or overheating. Be aware that kinks in pipework may result in air pressure being
trapped in the pipework and associated equipment. Replacement hardware, tubing, hose, fittings, etc. must be of equivalent size, type and strength
as original equipment and be designed specifically for such applications and systems. Check the attachment of all pipework; it should be installed
so that it cannot abrade or be subjected to excessive heat.
10 Components with stripped threads or damaged/corroded parts must be replaced completely. Do not attempt repairs requiring machining or welding
unless specifically stated and approved by the vehicle or component manufacturer.
11 Never attempt to install, remove, disassemble or assemble a device until you have read and thoroughly understood the recommended procedures.
Some units contain powerful springs and injury can result if not properly dismantled and reassembled. Use only the correct tools and observe all
precautions pertaining to use of those tools.
12 Before removing any device note its position and the connections of all pipework so that the replacement/serviced device can be properly installed.
Ensure that adequate support or assistance is provided for the removal/installation of heavy items.
13 Use only genuine replacement parts, components and kits as supplied by Knorr-Bremse or the vehicle manufacturer.
14 The serviced or replaced product must be checked for correct function and effectiveness.
15 If products have been dismantled, serviced or replaced, whose performance could affect braking performance or system behaviour, this should
be checked on a roller dynamometer. Bear in mind that a lower performance may be experienced during the bedding-in phase if new brake pads/
linings and/or brake discs/drums have been fitted.
16 Prior to returning the vehicle to service, make certain that all components and the complete brake systems are leak free and restored to their proper
operating condition.
Welding
To avoid damage to electronic components when carrying out electrical welding, the following precautions should be observed:
1
In all cases, before starting any electrical welding, remove all connections from any electronic control units or modules, noting their position and the
order in which they are removed.
2
When re-inserting the electrical connectors (in reverse order) it is essential that they are fitted to their correct assigned position - if necessary this
must be checked by PC Diagnostics.
Disposal of Waste Equipment by Business Users in the European Union
This symbol on the product, packaging or in user instructions, indicates that this product must not be disposed of with other general waste. Instead,
it is your responsibility to dispose of the waste electrical and electronic parts of this product by handing them over to a company or organisation
authorised for the recycling of waste electrical and electrical equipment. For more information about arrangements for waste equipment
disposal please contact your Knorr-Bremse distributor or local Knorr-Bremse representative.