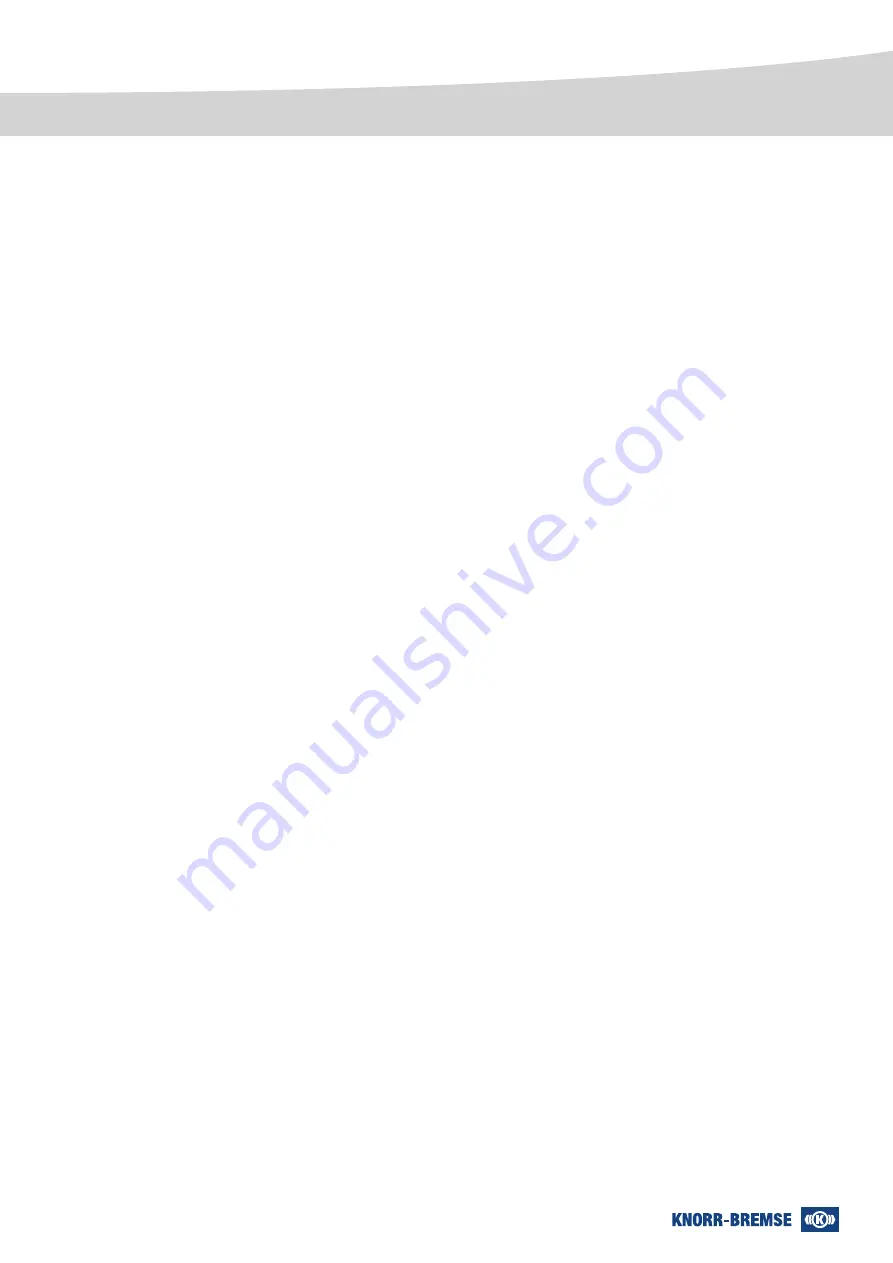
7
Introduction
1
Unloader function
The pressure after the delivery check valve also flows to
the unloader valve. When the increasing system pressure
reaches the preset cut-out pressure, the unloader valve
sends a pressure signal to the purge valve.
Purge function
The pressure from the unloader valve causes the purge
valve to open which connects the initial drainage chamber
to atmosphere through exhaust port
3
and the accumulated
condensate. Oil and solid matter is then ejected. If the
compressor control function is not used and the purge
valve is open, air from the compressor discharges directly to
atmosphere through the purge valve seat and exhaust port
3
.
Regeneration function
The resulting drop in pressure in the initial drainage
chamber causes air to flow back through the desiccant
bed and allows the delivery check valve to close. At the
same time clean, dry air flows back through the desiccant
bed, collecting water from the desiccant and regenerating
it ready for the next
Charge
phase. The wet air then flows
down the outside of the inner desiccant cartridge and is
discharged to atmosphere through the exhaust port
3
.
Subsequent operation of the braking system will cause
the downstream air pressure to fall. When the pressure
drops to the cut-in pressure, the pressure signal from the
unloader valve to the purge valve drops to zero and the
purge valve closes. The
Charge
phase will then begin
again and the braking system pressure will build.
For air processing units with time switch the compressed air
required for regeneration is taken from the supply air reser-
voirs mounted downstream in the system. The regeneration
time is determined by the pneumatic time switch and
depends on the supply volume and the operating pressure
of the pneumatic system. Air processing units without time
switch require a separate reservoir for the regenerating air,
the size of which depends on the system volume and the
cut-out pressure. During the
Charge
phase the separate
purge reservoir is charged through port
25
.
Timing function (optional)
During the
Charge
phase, some of the clean dry air from
the desiccant bed passes through the timing choke and
charges the integral timing reservoir.
During the
Purge
phase, the loss of pressure in the inlet
cavity will close the delivery check valve. Some dry air
from the brake service reservoirs is permitted to return
through the multi-circuit protection valve then through the
purge choke. This air flows back through the desiccant
bed and the oil separator and collects water from the
desiccant regenerating it ready for the next charge cycle.
After a predetermined time, determined by the size of the
timing choke, the air pressure in the timing reservoir will
drop sufficiently for its piston to close and stop the return
feed from the brake system. This stops the purge phase,
but the compressor remains unloaded. The sizes of the
timing choke and the purge choke are designed to match
the system requirements such that the
Purge
phase is
completed well within the compressor off-load cycle and
sufficient air is returned to fully regenerate the desiccant.
1 2 4
Multi-circuit protection element
Basic function
The multi-circuit protection valve consists of four individual
pressure protection valves connected together in various
configurations and each having limited feedback capability.
Air is supplied through the delivery check valve in the
air dryer element, and is delivered from ports
21
-
24
to
circuits
1
to
4
respectively. Circuits
1
and
2
may have a
bypass feature (optional).
When the opening pressure of each valve element
is reached, the diaphragm will lift, allowing air to
flow past the valve seat into the respective delivery
port and to circuits 23 and 24 from circuits 21
and 22 depending on the valve configuration.
Due to air usage or leakage etc, when the falling pressure
reaches the closing pressure, the diaphragm will drop
and the supply-to-delivery path will close.
Opening pressure
The opening pressure is the pressure required to open a
valve element when the respective downstream circuit is
at zero pressure. If a circuit is not at zero pressure, the
downstream pressure will also be acting on the diaphragm.
This means that a lower pressure will be required to open
the valve element, i.e. the actual opening pressure is
dependent on the downstream pressure and is therefore
usually lower than the stated value for the valve.