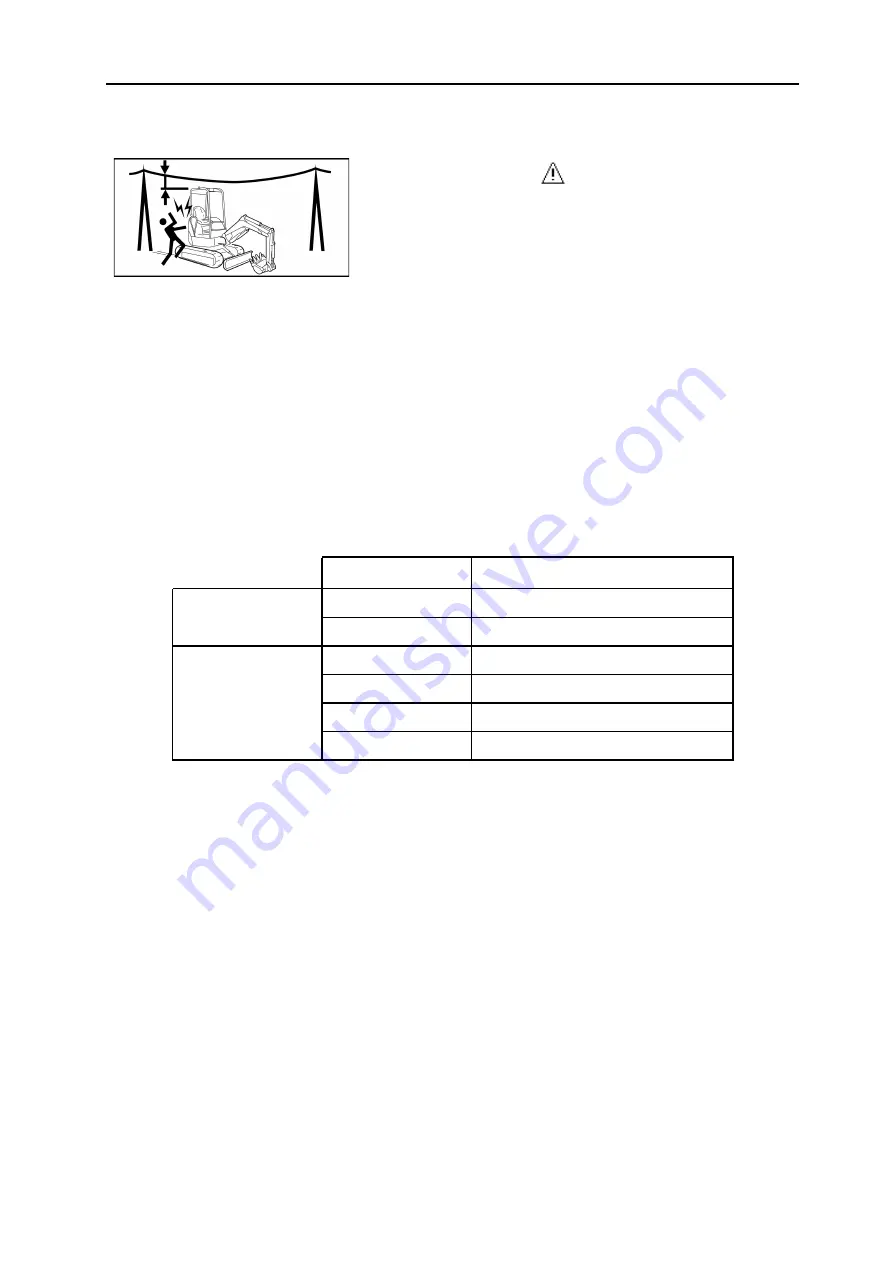
2 Usage precautions
50
2.3.3 Working near electricity lines
DANGER
Working close to overhead electricity lines is very
dangerous and specific precautions must be taken.
• For this manual, you are considered as working near overhead electricity lines once the
equipment or your machine's load can reach the minimum distances indicated in the table
below.
• Follow these procedures to prevent any accident or injury :
– Wear shows with rubber or leather soles.
– Use a signaller to warn the operator when the machine is too close to an electrical line.
– If the machine is to enter into contact with a cable, the operator must not leave his seat.
– Warn all personnel on the ground to stay far enough away from the machine.
• To determine the voltage of the wires on the work site, contact the electricity production
company concerned.
Voltage (V)
Minimum safety distance (m)
Transformer
≤ 100/200
2
≤ 6600
2
Transmission line
≤ 22000
3
≤ 66000
4
≤ 154000
5
≤ 275000
7
2.3.4 Working near obstacles
• When moving in a tunnel, under a bridge or when you are working in an area near tall ob-
stacels, drive the machine carefully to avoid knocking the boom, the arm or the accessory
against these obstacles.
2.3.5 Emergency stop and securing the machine
In case of an emergency stop of the machine, immediately put the accessory or load being hand-
led on the ground according to the following procedure:
In case of hose rupture or imminent dangerous phenomenon due to loss of control of the ma-
chine, release the machine controls and immediately lift the safety lever. The machine's power
circuits are cut, except the one controlling the blade.
Note
If necessary, move the ignition key to OFF to stop the engine.
[S2PU00027ZE02] [1204CsCshWbYs]
Summary of Contents for SK17SR
Page 2: ...S2PU00027ZE02 1204CsCshWbYs...
Page 4: ...S2PU00027ZE02 1204CsCshWbYs...
Page 6: ...S2PU00027ZE02 1204CsCshWbYs...
Page 8: ...S2PU00027ZE02 1204CsCshWbYs...
Page 10: ...S2PU00027ZE02 1204CsCshWbYs...
Page 18: ...2 S2PU00027ZE02 1204CsCshWbYs...
Page 23: ...3 Warning labels 7 S2PU00027ZE02 1204CsCshWbYs...
Page 52: ...36 S2PU00027ZE02 1204CsCshWbYs...
Page 54: ...38 S2PU00027ZE02 1204CsCshWbYs...
Page 114: ...98 S2PU00027ZE02 1204CsCshWbYs...
Page 138: ...122 S2PU00027ZE02 1204CsCshWbYs...
Page 140: ...124 S2PU00027ZE02 1204CsCshWbYs...
Page 144: ...128 S2PU00027ZE02 1204CsCshWbYs...
Page 146: ...130 S2PU00027ZE02 1204CsCshWbYs...
Page 158: ...142 S2PU00027ZE02 1204CsCshWbYs...