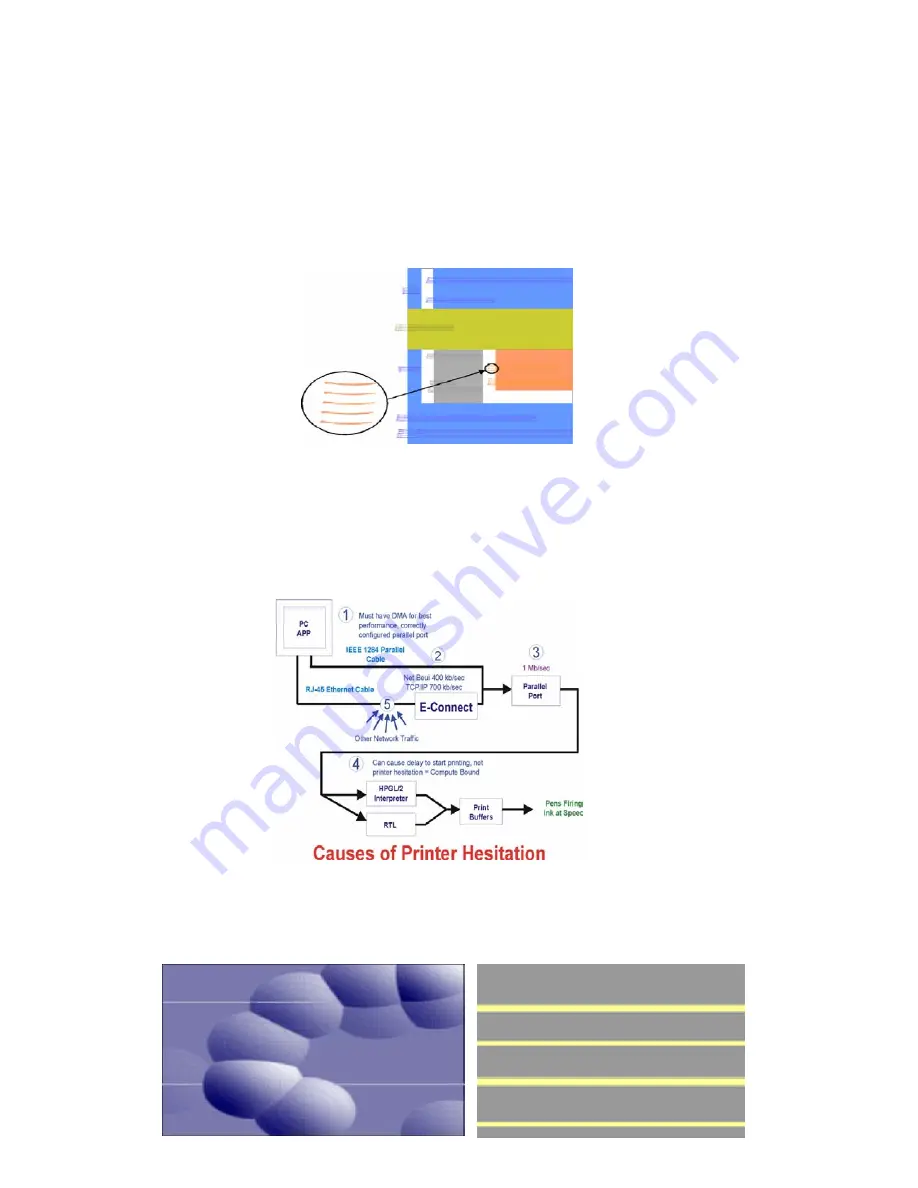
NovaJet 800 Series Training Guide
26
4.
Faint cut lines or heavy lines which angle slightly on one end are caused
by the carriage head hitting the media surface. Media up to a 20 mil
thickness can pass through the printer. Ensure media has not been
exposed to humidity for long periods as this will cause media to become
stiff. Check with technical support for media types which can pass
through the printer.
5.
Printer carriage delayed printing/hesitation. Hesitation of the carriage
assembly during printing can be due to various factors; i.e. Slow processor
in workstation for Software RIPs, screen saver turned on, improperly
configured parallel port for non-networked environments, incorrect speed
setting for driver data transfer rate, Firewall interference, print server setup
(untested print server used/incorrect SEH setup), other network traffic, etc.
6.
Horizontal bands which extend the width of the image and repeat at a
relatively consistent rate are usually caused by the Autowipe feature being
turned on or improper ink pre-heat settings.