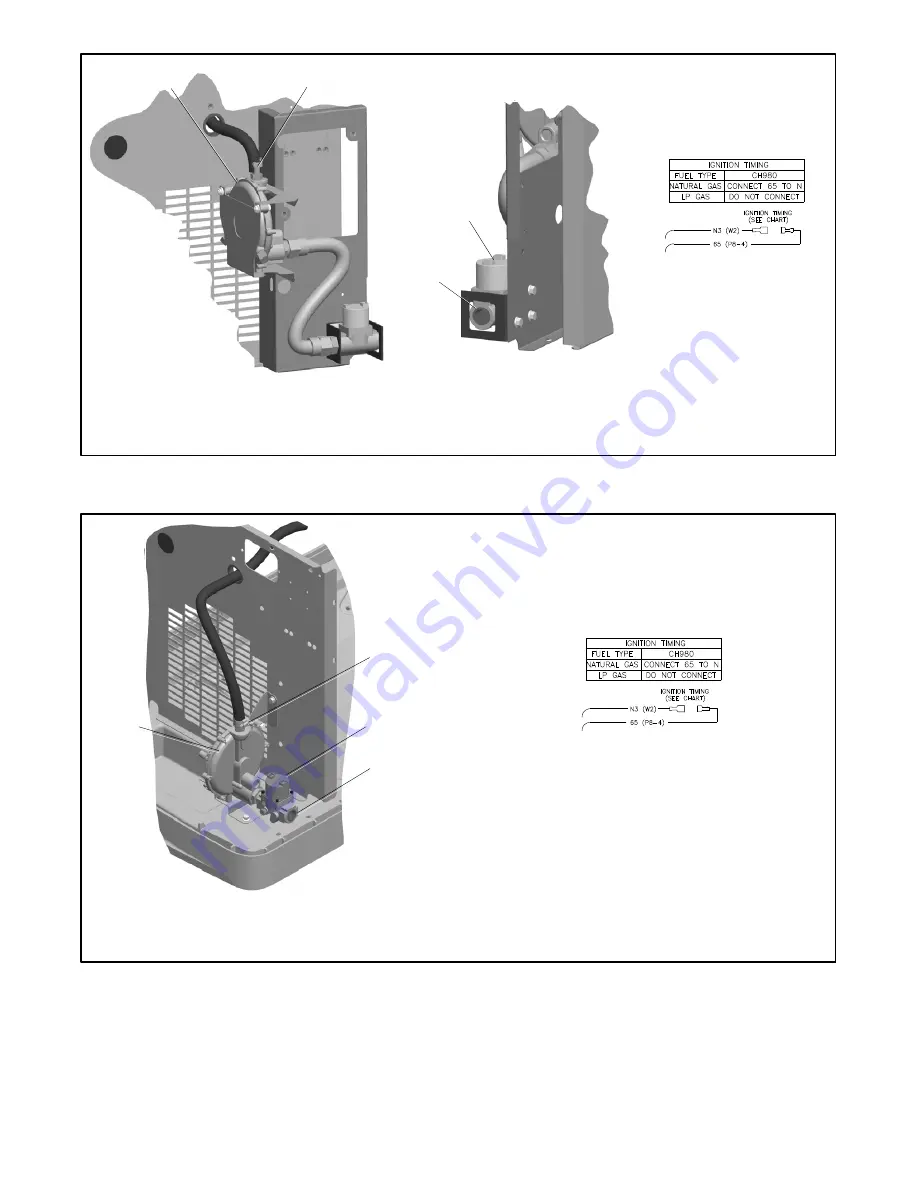
TP-6735 7/17
79
Section 5 Component Testing and Adjustment
1
GM66563
1. Regulator
2. Fuel block (not shown) or LP orifice location (see
Figure 5-29)
3. Fuel inlet, 1/2 in. NPT female
4. Fuel solenoid valve and digital spark advance ignition (DSAI)
leads
4
2
3
(Enlarged to
show detail)
DSAI Lead Connection
Figure 5-27
Fuel System
GM80110
1. Regulator
2. Fuel block (not shown; see Figure 5-32) or LP orifice location
(see Figure 5-30)
3. Fuel solenoid valve and digital spark advance ignition (DSAI)
leads
4. Fuel inlet, 1/2 in. NPT female
1
2
3
4
DSAI Lead Connection
Figure 5-28
Revised Fuel System
Summary of Contents for 14RES
Page 2: ......
Page 6: ...TP 6735 7 17 6...
Page 16: ...TP 6735 7 17 16 Section 1 Specifications Notes...
Page 102: ...TP 6735 7 17 102 Section 6 Disassembly Reassembly Notes...
Page 108: ...TP 6735 7 17 108 Section 7 Wiring Diagrams Notes...
Page 120: ...TP 6735 7 17 120 Notes...
Page 121: ...TP 6735 7 17 121 Notes...
Page 122: ...TP 6735 7 17 122 Notes...
Page 123: ......