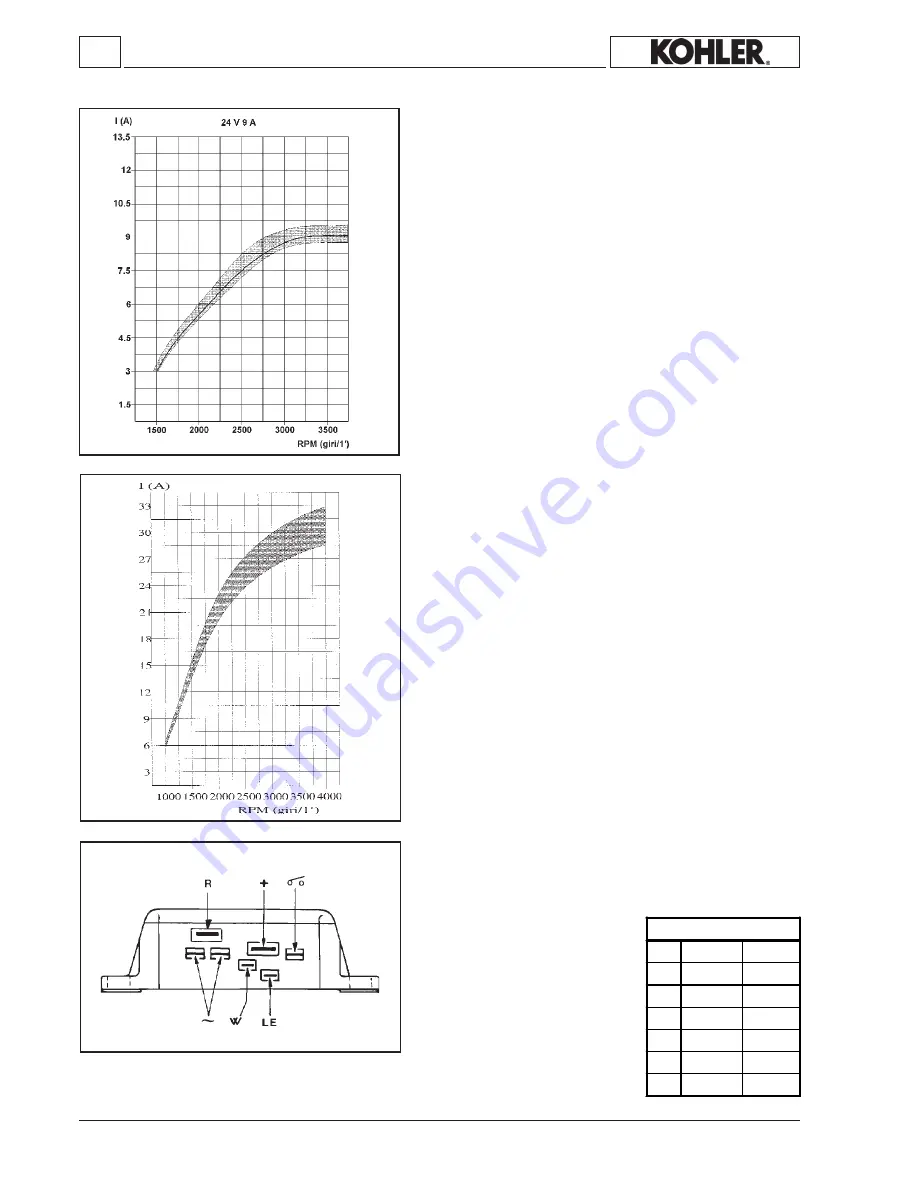
125
127
126
11
- 62 -
ELECTRICAL SYSTEM
24V, 9A alternator battery recharging curve
12V, 30A alternator battery recharging curve
The test was conducted after heat stabilizing at 20°C.
The value of the current delivered in relation to the curve may be
subjected to a variation of b10 % and -5%.
Voltage regulator
12V, 12A: for standard alternators with 3 output wires
12V, 30A: for 12V, 20A alternators with 2 output wires
24V, 9A: for 24V, 9A alternators with two output wires
The tabs are in different sizes to prevent
incorrect connections.
Tab dimensions mm
Width
Thickness
~
6.35
0.80
R
9.50
1.12
+
9.50
1.12
LE
4.75
0.50
0
/
0
6.35
0.80
W
4.75
0.50
KD 225_315_350_400_440 Workshop Manual_cod. ED0053029330_
1° ed
_ rev.
00