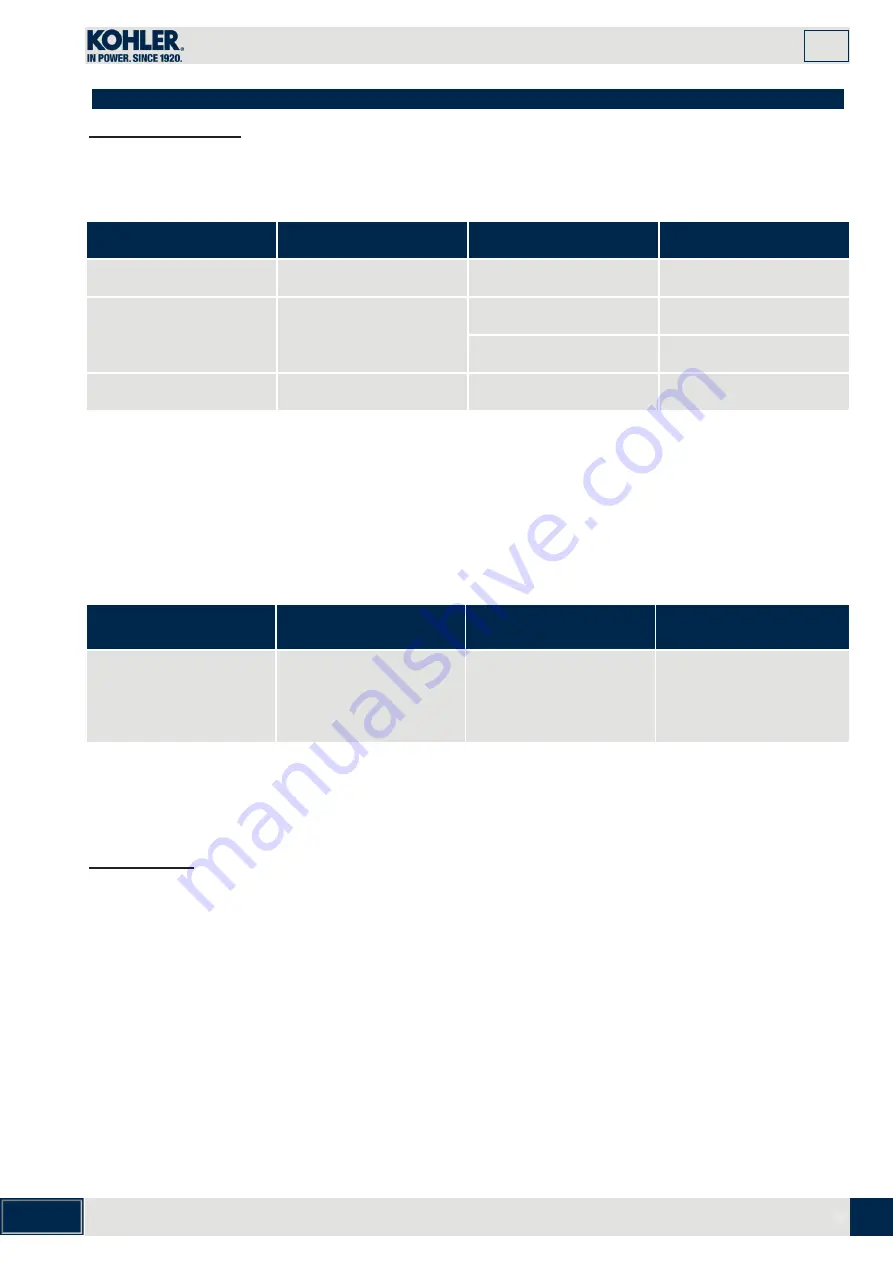
8
_14
35
INFORMATION ABOUT WARRANTY
EN
KOHLER DIESEL ENGINES GLOBAL WARRANTY TERMS
1. WARRANTY PERIOD
Kohler Co. warrants to the End User that each Diesel engine will be free from manufacturing defects in materials or workmanship
in normal service for the applicable coverage period or operating hours (whichever comes first) set forth below, provided the
engine is operated and maintained in accordance with Kohler Co.’s instructions and manuals.
ENGINE SERIES
WARRANTY PERIOD
OPERATING HOURS
WARRANTY COVERAGE
KOHLER Diesel (non KDI)
3 Years
0 – 2.000
100% Parts & Labor
KOHLER KDI
3 Years
0 – 2.000
100% Parts & Labor
2.001 – 6.000
Major Components Only*
Lombardini Diesel
2 Years
0 – 2.000
100% Parts & Labor
*Major component defects are failures related to crankcase casting, cylinder head casting, crankshaft, crankshaft pulley,
camshaft, connecting rod, flywheel, oil pump.
For the Warranty Period stated above, the period begins on the date of purchase of the finished equipment on which the engine
is installed. If no hour meter is installed on the application, the Operating Hours will be calculated as 4 hours of use per day
for 5 days per week beginning on the date of purchase.
Kohler Co.’s obligation under this warranty is expressly limited, at its option, to an appropriate adjustment, repair or replacement
of such part or parts as found to be defective following an inspection by Kohler Co. or an authorized service facility designated
by Kohler Co.
SPARE PARTS
WARRANTY PERIOD
OPERATING HOURS
WARRANTY COVERAGE
KOHLER and Lombardini
Diesel Parts
2 Years
0 – 2.000
100% Parts & Labor
Parts/components that are scheduled to be replaced as part of the required maintenance schedule will be covered under Kohler
Co.’s warranty from date of purchase of the part up to the first scheduled replacement point for the subject parts/ components.
All other Spare Parts items are covered by the above warranty provided that the repairs have been executed by Kohler Co or
by an Authorized Kohler Service Dealer.
2. EXCLUSIONS
The following items are not covered by this warranty.
• Damage caused by: (i) an accident or casualty; (ii) unreasonable use or neglect; (iii) normal wear; (iv) premature wear from
improper maintenance; (v) improper storage; (vi) old or contaminated fuel left within the fuel system, which includes but is not
limited to tanks, fuel lines, or fuel injection components; (vii) unapproved modifications.
• Failures caused by: (i) faulty repairs made by any party other than Kohler Co. or an authorized service facility designated by
Kohler Co.; (ii) use of non-Kohler replacement service parts; or (iii) additional damages caused by a lack of prescribed actions
as a result of an alarm light activation, either caused by fault or negligence or un-attended use of the engine; (iv) an act
beyond the control of Kohler Co., which includes but is not limited to theft, vandalism, fire, lightning, earthquake, windstorm,
hail, volcanic eruption, flood or tornado.
• Transportation charges or travel expenses in connection with the repair or replacement of defective parts on the engine.
• Engine accessories such as fuel tanks, clutches, transmissions, power drive assemblies, and batteries, unless supplied or
installed by Kohler Co.
• Engines installed in an application not formally reviewed by Kohler.
• Rental of other equipment during performance of warranty repairs All items subject to wear and to periodical maintenance
such as listed in the Use & Maintenance Manual (such as air, oil or fuel filters, belts etc.) are warranted for a period equal to
the prescribed interval of replacement as listed in the Manual.
• Fuel, lubricating oil, coolant/antifreeze.
ED0053029510
Index