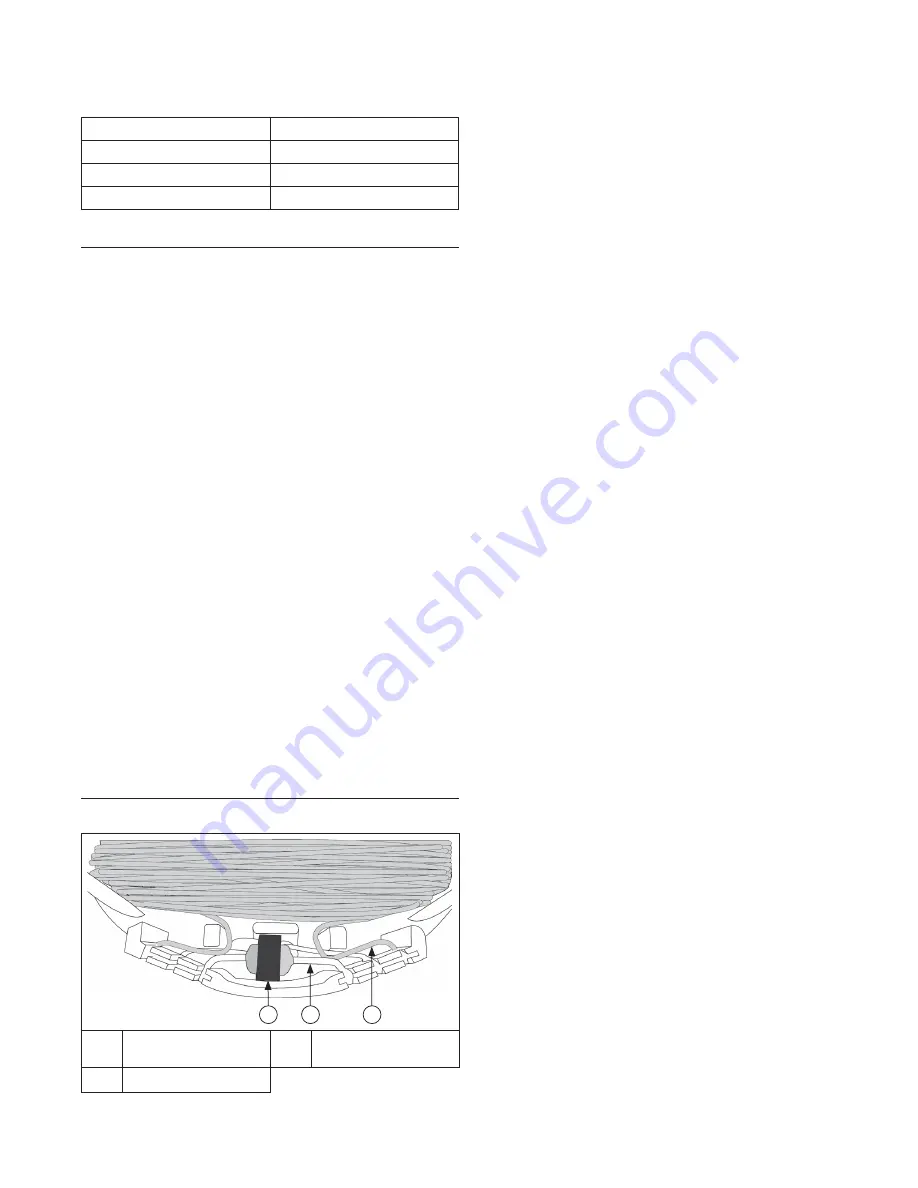
7
34 690 01
8
/16
Troubleshooting
KohlerPower.com
Theory for Capacitor-Excited Generator
On a brushless, capacitor-excited generator, rotor slip
rings are replaced with a diode. Diode also provides
current limiting and surge protection for diodes. A large
capacitor is connected across an auxiliary winding of
stator. On start-up, residual magnetism from rotor iron
provides a sufficient enough magnetic field to induce a
current flow in auxiliary winding and capacitor circuit.
As rotor windings pass through magnetic flux of auxiliary
winding, current flow is induced in rotor field windings.
Diodes rectify this AC current flow to DC current
flow which creates electromagnets at pole pieces on
rotor. This rotor field then induces a voltage on stator
windings. Just like a brush type alternator, revolving field
generator voltages from both stator coils are "in phase"
to each other. Therefore total output voltage is multiplied
by 2 and voltage is induced in each stator winding.
As customer load is increased, more current is induced
in rotor, increasing field strength of rotor. This in turn
increases current in auxiliary winding and capacitor
circuit. As rotor windings pass through increased flux of
auxiliary winding a larger current flow is induced in rotor
field windings. Diodes rectify this increased AC current
to DC. Voltage induced on stator main windings is
increased thus providing voltage regulation as customers
load changes.
Capacitor-excited generators rely on residual magnetism
in rotor in order to build voltage on startup. Residual
magnetism can be lost during assembly/disassembly
and generator will fail to build voltage. It can be restored
(reflashed) by placing an AC potential across capacitor
winding. This will induce a rectified current flow in rotor
winding to re-magnetize poles of rotor. An AC voltage of
30-100 volts can be used to reflash rotor.
Troubleshooting a Capacitor-Excited Generator
Rotor with Diode
A
C
B
A
Diode
B
Cut Diode for
Testing
C
Rotor Winding
No or Low Output Voltage
1. Engine speed set too low. Needs to be set for 3600
RPM at no load. Adjust if necessary. If speed is
correct proceed to next step.
2. Disconnect stator exciter leads from capacitor and
measure resistance between exciter leads. Compare
to value in table. Also check resistance from each
exciter lead to ground. If out of specification or
shows resistance to ground then replace stator. If
within specification proceed to next step.
3. Measure μF (microfarad) value of capacitor with
appropriate meter. If meter will not measure μF value
of capacitor, you can use an analog or digital
ohmmeter and verify if capacitor will charge and
discharge.
a. Using a screw driver, place it across both
terminals of capacitor while unit is not running.
This will discharge capacitor.
b. Remove exciter wires from capacitor. Set meter
to check resistance. If meter has a range setting,
set it to RX1. With leads of meter apart, your
meter should read infinity or open circuit. Place
meter leads across terminals of capacitor. Meter
should read infinity or open circuit, drop from a
high resistance value down to a low resistance
value, then start climbing back up to a high
resistance value.
c. Reverse your meter leads on capacitor. Reading
should go from a high resistance value down to a
low resistance value, then climb back up to a high
value.
1. If meter maintains reading, indicating an open
circuit or infinity, that means capacitor is open
circuited. Capacitor is bad and should be
replaced.
2. If meter goes to very low value and stays
there, that means capacitor is short circuited.
Capacitor is bad and should be replaced.
d. If capacitor checks out correctly then proceed to
next step.
4. With capacitor disconnected, try flashing exciter
winding by momentarily applying 30-100 VAC to
stator exciter wires while unit is not running.
Reconnect capacitor and try running unit.
a. If there is still no output then apply a small
amount of load to unit, for instance 60 watts,
when trying to start unit. If output occurs then let
unit run for a while.
b. Shut unit down and start it back up and see if
output is good.
1. If unit has no output, it could mean rotor will
not hold residual magnetism and may need to
be replaced. Normally if rotor is good and has
some residual magnetism, then you will at
least get some residual output voltage from
main stator leads of about 3-6 VAC.
2. If you get 0 output voltage from main stator
leads, stator checks out good, and diodes are
good on rotor, then rotor is bad. Do not
replace rotor until remaining steps have been
followed.
Alternator Specification
Unit
Ohms
Stator Winding
0.077
Rotor Winding
7.54
Exciter
0.44