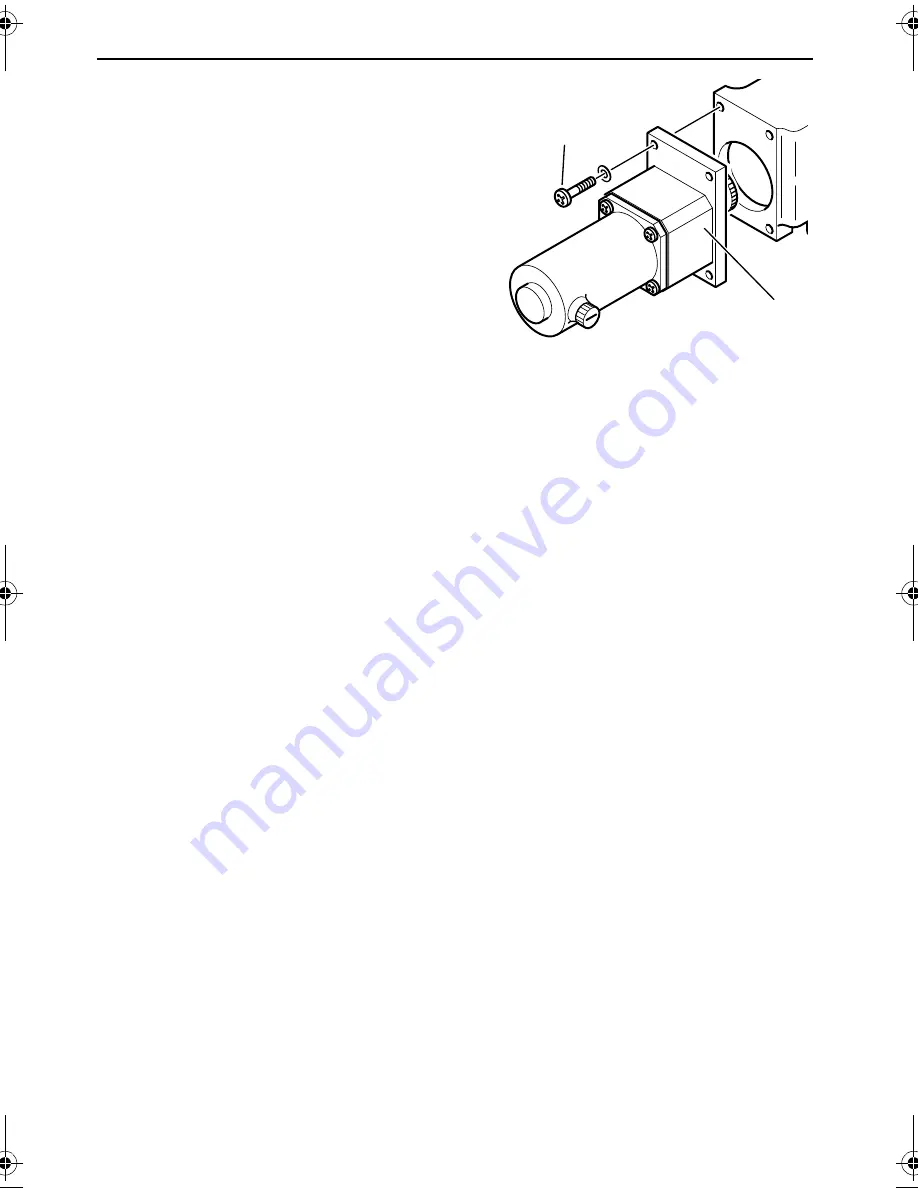
AUTO PICLE-S
32
6.1.2 Disassembly for maintenance and
inspection of the gear case
Disassemble the gear case in the
same manner as the maintenance
and inspection of the motor in
section 6.1.1. Remove the four round
crosshead screws (M6x16) (8) that
are securing the casing (9) and apply
the notemp grease to the gear case.
6.2
Daily inspection
Oil the threaded section of the lift shaft and the sliding section of the shaft
column every week.
6.3
3-Month or 1000-hour inspection
Remove the carbon cap and check the carbon brush for abrasion.
6.4
6-Month inspection
Disassemble, clean and oil the gear case. Refer to 6.1.2 for the
disassembling procedure.
8
9
figure 6 - 3
Auto Picle-S.book Page 32 Thursday, April 11, 2002 11:15 AM
Summary of Contents for AUTO PICLE-S
Page 1: ...AUTO PICLE S REMOTE CONTROL GAS MOTORIZED PIPE CUTTING MACHINE KOIKE SANSO KOGYO CO LTD...
Page 11: ...AUTO PICLE S 10...
Page 13: ...AUTO PICLE S 12...
Page 25: ...AUTO PICLE S 24...
Page 31: ...AUTO PICLE S 30...
Page 37: ...AUTO PICLE S 36...
Page 39: ...AUTO PICLE S 38 8 2 Assembly drawing figure 8 2...
Page 40: ...AUTO PICLE S 39 9 Parts list 9 1 Body unit...
Page 43: ...AUTO PICLE S 42 9 2 Driving unit...
Page 46: ...AUTO PICLE S 45 9 3 Electrical and gas unit...
Page 49: ...AUTO PICLE S 48 9 4 Guide rail...
Page 51: ...AUTO PICLE S 50...