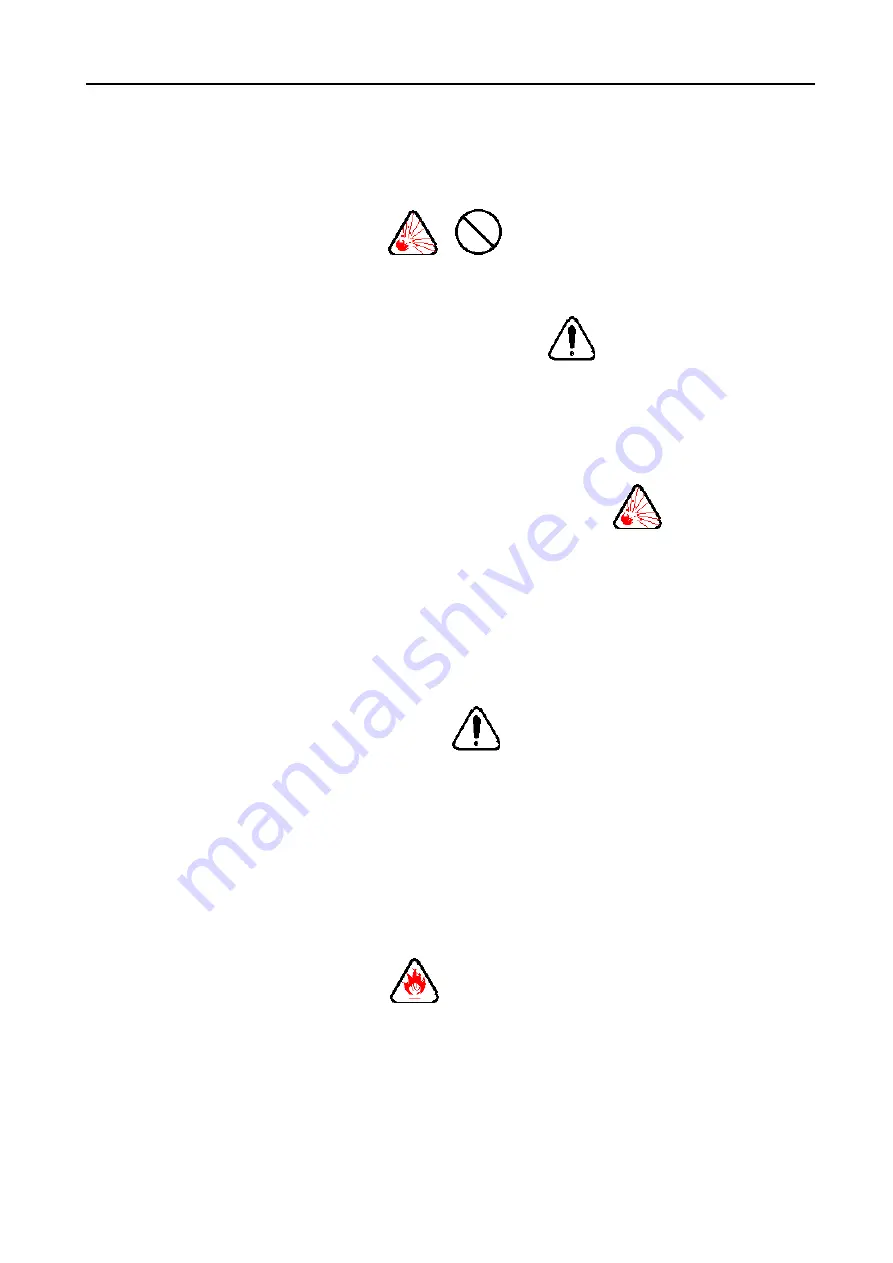
IK-12 NEXT
- 4 -
1.2 Gas cutting safety precautions
Strictly observe the safety rules and precautions to ensure the safety of gas cutting operations.
Operators and supervisors MUST keep safety in mind.
1.2.1 Prevention of explosion
1.Never cut pressurized cylinders or hermetically sealed containers.
2.Ensure sufficient ventilation for gas cutting to prevent the air from becoming stale.
1.2.2 Pressure regulator safety precautions.
1.Before starting operation, check that all pressure regulators are operating correctly.
2.Ask a skilled repair engineer to perform maintenance and inspection service.
3.Do not use pressure regulators from which gas is leaking, nor malfunctioning pressure
regulators.
4.Do not use pressure regulators smeared with oil or grease.
1.2.3 High-pressure gas cylinder safety precautions
1.Never use broken cylinders or cylinders from which gas is leaking
2.Install cylinders upright and take measures to prevent them from falling.
3. Use cylinders only for specified purposes.
4. Do not smear container valves with oil or grease.
5. Install cylinders in a place free from heat, sparks, slag, and naked flame.
6.Contact the distributor if the container valves will not open.
Never use a hammer, wrench, or other tools to forcibly open container valves.
1.2.4 Safety precautions for hoses
1. Use the oxygen hose for oxygen gas only.
2. Replace cracked hoses or other hoses damaged by sparks, heat, unshielded fire, etc.
3. Install hoses without twisting.
4. To prevent breakage of hoses, take great care during operation and transportation.
5. Do not hold the hoses when moving the machine.
6. Periodically check the hoses for damage, leakage, fatigue, loose joints, etc, to ensure
safety.
7. Cut hoses to the minimum possible length. Short hoses reduce hose damage and pressure
drop, as well as reduce the flow resistance
.
1.2.5 Safety precautions for fire
Take safety precautions to prevent fire prior to gas cutting.
Ignoring hot metal, sparks, and slag could cause a fire.
1.Keep a fire extinguisher, fire extinguishing sand, bucket full of water, etc. ready on the site
where gas cutting is performed.
2.Keep flammables away from the cutting area to avoid exposure to sparks.
3.Always cool steel plates that have become hot after cutting, as well as hot cut parts or scrap,
before bringing them close to flammables.
4.Never cut containers to which flammable materials are stuck.