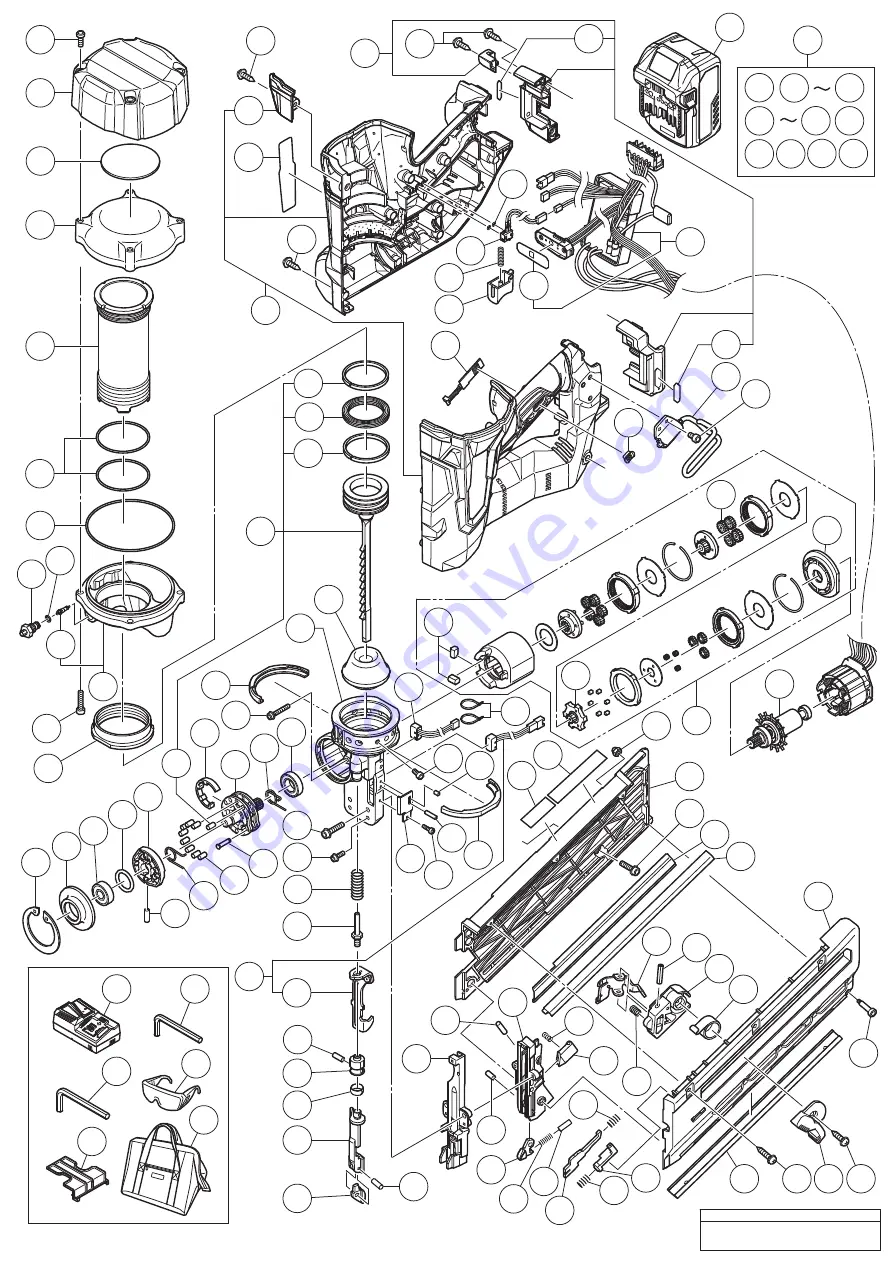
M O D E L
Rev.1
NR3665DA
B
B
10
1
2
3
4
5
6
13
7
8
9
12
11
15
14
16
17
27
23
24
28
29
30
19
21
22
31
32
34
35
36
37
38
40
41
42
43
44
47
48
49
47
50
56
57
54
55
53
58
64
62
63
80
26
81
82
84
99
100
101
102
85
86
91
97
97
96
98
103
104
105 106 107
83
25
26
67
73
66
68
504
501
505
503
506
79
14
69
70
72
71
78
75
18
20
65
76
33
A
A
59
60
47
52
61
3
108
12
9
6
15
17
26
47
48
57
51
92
93
87
89
90
45
46
88
39
77
74
94
95
502