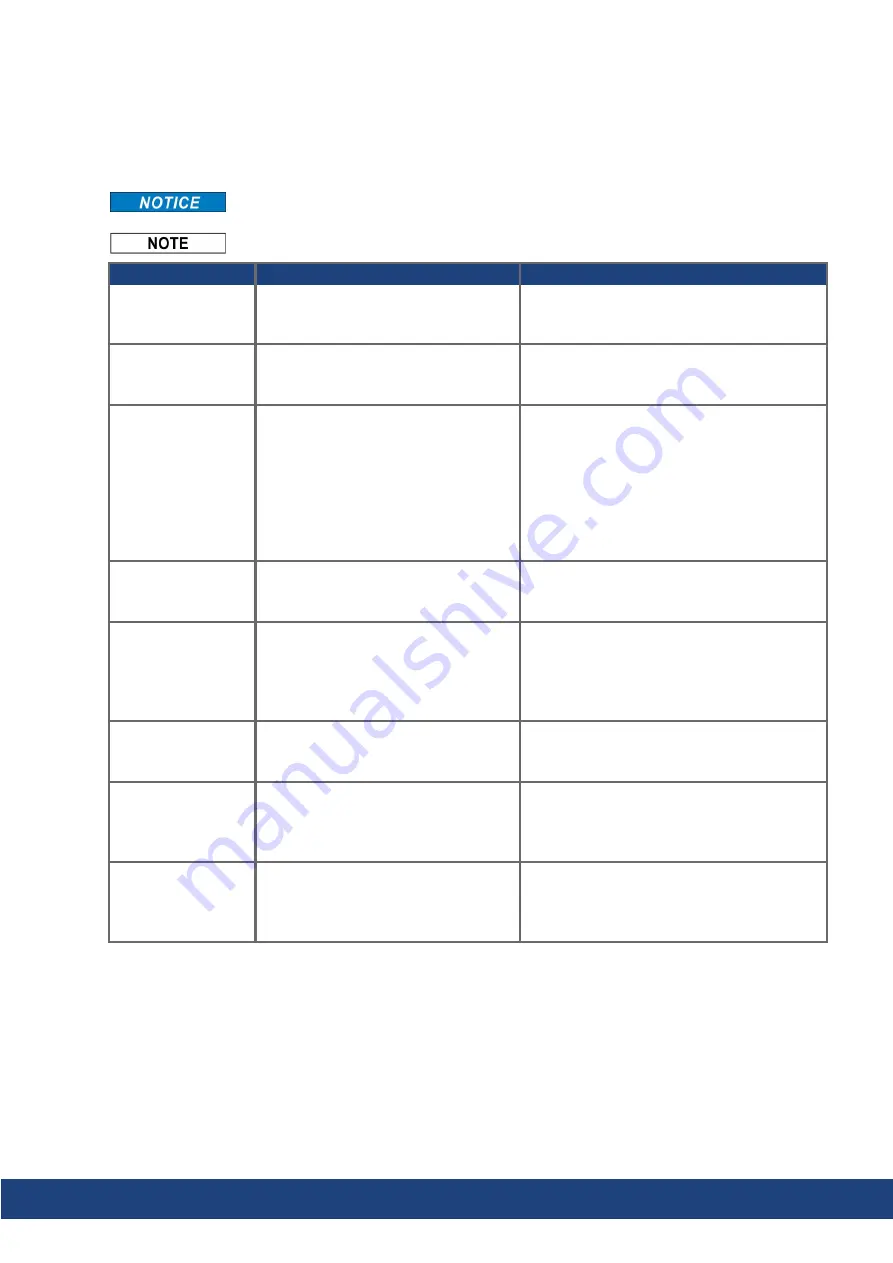
9.5 Troubleshooting
Drive problems occur for a variety of reasons, depending on the conditions in your installation. The causes of
faults in multi-axis systems can be especially complex. If you cannot resolve a fault or other issue using the
troubleshooting guidance presented below, customer support can give you further assistance.
Eliminate errors and faults in compliance with work safety rules. Troubleshooting only by
qualified and trained staff.
More details on the removal of faults can be found in the WorkBench User Manual.
Problem
Possible Causes
Remedy
HMI message:
Communication fault
1. wrong cable used, cable plugged
into wrong position on drive or PC
2. wrong PC interface selected
1. plug cable into the correct sockets on the
drive and PC
2. select correct interface
Drive does not enable 1. HW Enable configured but not wired
2. HW or SW Enable not set
1. connect HW Enable to the selected input
2. Apply 24V to HW Enable and select SW
Enable in WorkBench / Fieldbus
Motor does not rotate 1. drive not enabled
2. software enable not set
3. break in setpoint cable
4. motor phases swapped
5. brake not released
6. drive is mechanically blocked
7. motor pole no. set incorrectly
8. feedback set up incorrectly
1. apply ENABLE signal
2. set software enable
3. check setpoint cable
4. correct motor phase sequence
5. check brake control
6. check mechanics
7. set motor pole no.
8. set up feedback correctly
Motor oscillates
1. gain is too high (speed controller)
2. feedback cable shielding broken
3. AGND not wired up
1. reduce AXIS#.VL.KP (speed controller)
2. replace feedback cable
3. join AGND to CNC-GND
Drive reports
following error
1. Irms or Ipeak set too low
2. current or velocity limits apply
3. accel/decel ramp is too long
1. verify motor/drive sizing
2. verify that AXIS#.IL.LIMITN/P,
AXIS#.VL.LIMITN/P are not limiting the
drive
3. reduce AXIS#.ACC/AXIS#.DEC
Motor overheating
1. motor operating above its rating
2. motor current settings incorrect
1. verify motor/drive sizing
2. verify motor continuous and peak current
values are set correctly
Drive too soft
1. AXIS#.VL.Kp (velocity) too low
2. AXIS#.VL.Ki (velocity) too low
3. filters set too high
1. increase AXIS#.VL.KP (velocity)
2. increase AXIS#.VL.KI (velocity)
3. refer to documentation regarding reducing
filtering (AXIS#.VL.AR*)
Drive runs roughly
1. AXIS#.VL.Kp (velocity) too high
2. AXIS#.VL.Ki (velocity) too high
3. filters set too low
1. reduce AXIS#.VL.KP (velocity)
2. reduce AXIS#.VL.KI (velocity)
3. refer to documentation regarding increas-
ing filtering (AXIS#.VL.AR*)
AKD2G-S Installation Manual, Safety 1 | 9 Setup
Kollmorgen | kdn.kollmorgen.com | July 2020
131