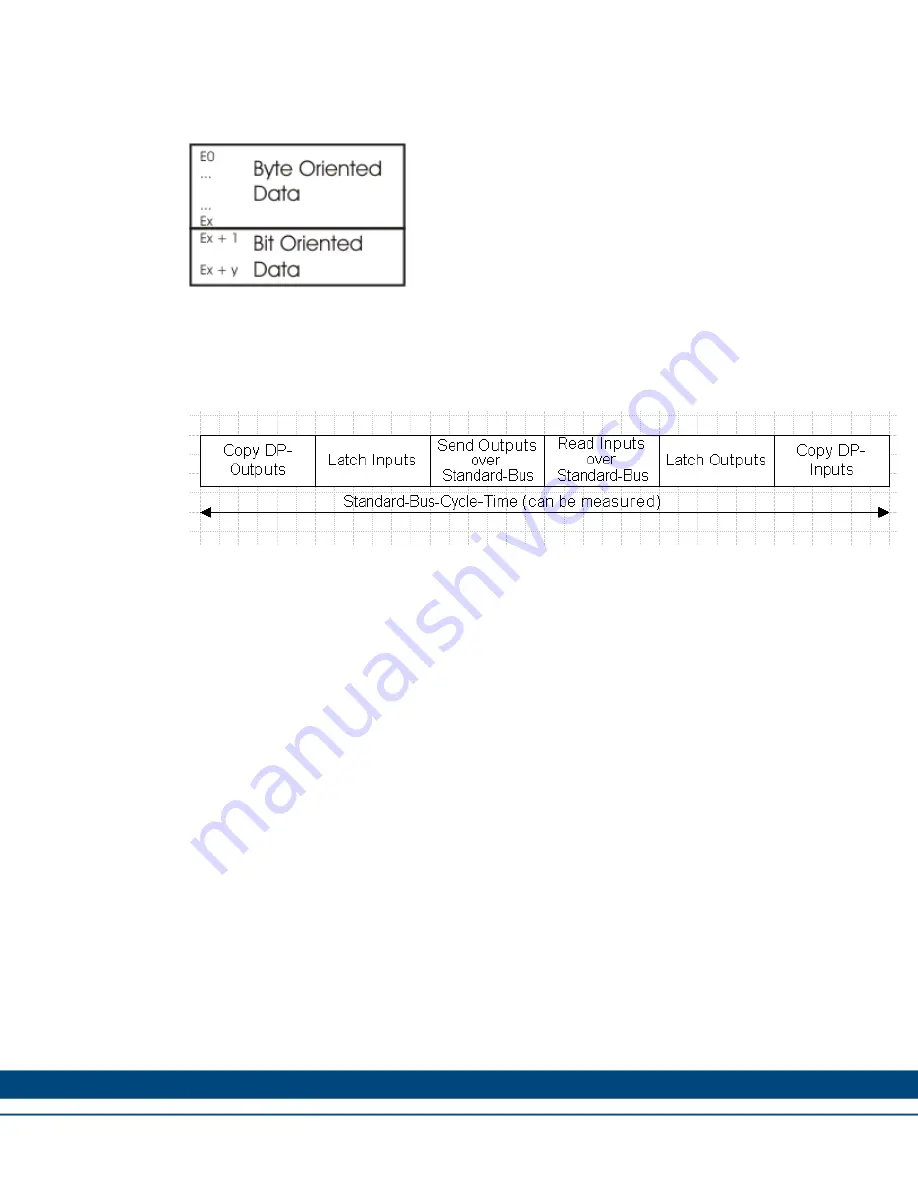
I/O Terminal /
MANUAL CONFIGURATION
35
Input data in the Bus Coupler
6.3.2 Standard-Bus
Cycle
The Standard-Bus cycle can be set to run freely (FreeRun mode) or synchronously
(synchronous mode) with respect to the DP cycle. The Standard-Bus cycle for the DP coupler
consists of the following parts:
The Standard-Bus cycle time can be calculated to a precision of approximately 10% by
means of the following formula (4-channel terminals or terminals with more than 6 bytes of
data require two or more Standard-Bus cycles. The number of Standard-Bus cycles is in
register ?? of table 90):
Tcyc (in µs) = number of Standard-Bus cycles x (600 + number of digital channels x 2.5
+ number of analog input channels x 32 + number of analog output channels x 42)
The Standard-Bus cycle time can be read via DPV1.
Standard-Bus Modes
The Standard-Bus mode (the type of synchronization between the Standard-Bus cycles and
the DP cycle) is set via the UserPrmData: