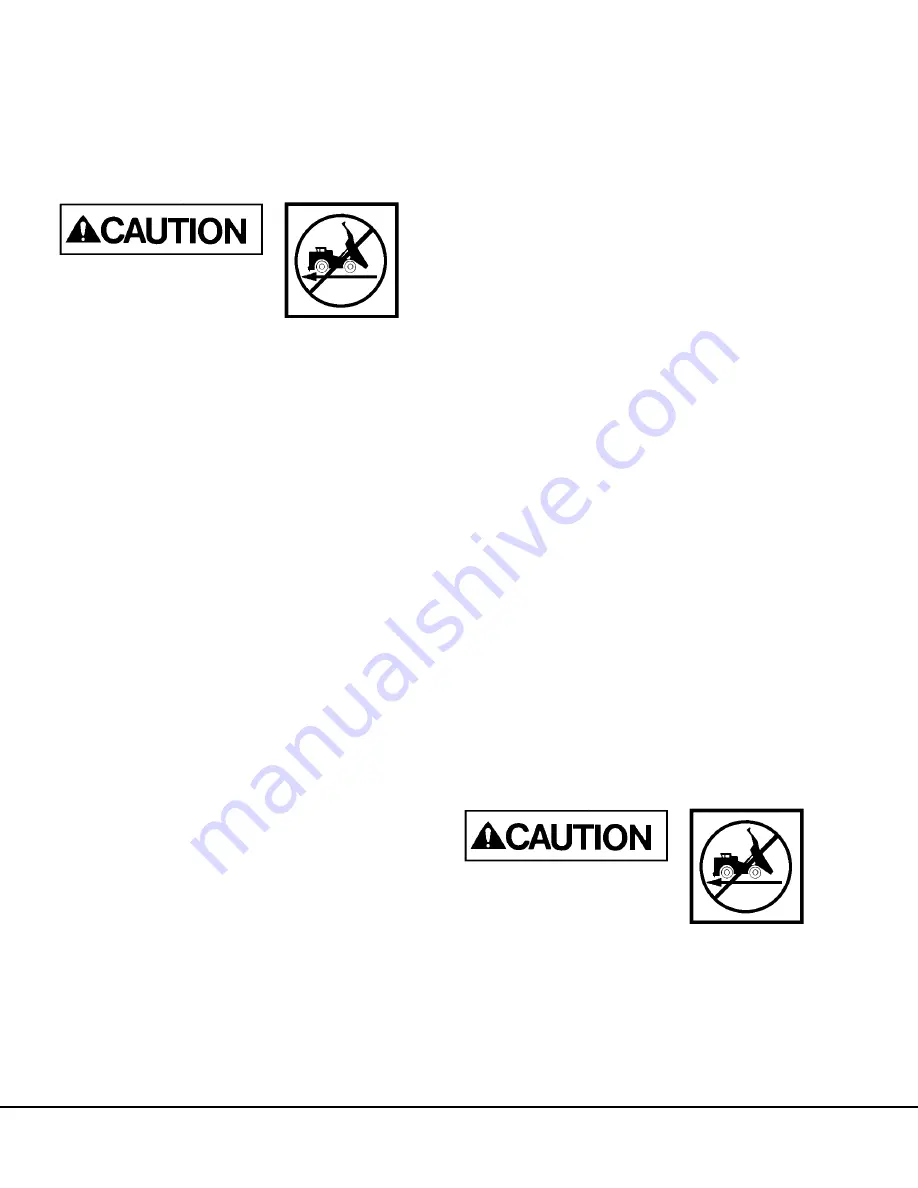
A3-30
General Safety & Operation
A03048
To Lower The Dump Body:
(When dumping over a berm or into a crusher):
8. Move the hoist lever forward to the DOWN posi-
tion and release. Releasing the lever places the
hoist control valve in the FLOAT position, allow-
ing the body to return to the frame.
DO NOT drive forward in the
fully raised position if the
dump body will not clear an
obstacle, such as a crusher
wall. DO NOT move the truck with a raised dump
body raised except in an emergency. Failure to
lower the body before moving the truck may
cause damage to the hoist cylinders, frame, and/
or body hinge pins.
NOTE: If the dumped material builds up at the rear of
the truck and the body cannot be lowered, perform
the following steps:
a. Move the hoist lever back to the HOIST posi-
tion and fully raise the dump body. Continue
to hold the hoist lever until the body is com-
pletely raised.
NOTE: If the body is not completely raised, it may
lower very rapidly when the truck is moved forward
and the material is cleared from the rear of the truck.
b. Once the body is fully raised, release the
hoist lever (it will return to the HOLD posi-
tion).
c. Shift the selector switch to FORWARD,
release the brake lock, and press the over-
ride button.
d. Slowly drive forward to clear the material.
e. Once the material is cleared, stop the truck,
place the selector switch in NEUTRAL, and
apply the brake lock.
f. Completely lower the body.
NOTE: Failure to hoist the body, after making an
unsuccessful attempt at lowering the body, may
result in the dump body suddenly lowering after the
truck has pulled ahead of the material that was
previously preventing the body from lowering.
To Lower The Dump Body
(When dumping on flat ground):
9. It is very likely when dumping on flat ground
that the dumped material will prevent the body
from lowering. In this instance, the truck will
have to be driven forward a short distance (just
enough to clear the material) before the body can
be lowered.
a. Shift the selector switch to FORWARD,
release the brake lock, and depress the
override button. Drive forward enough for the
body to clear the material. Stop, shift the
selector switch to NEUTRAL, and apply the
brake lock.
b. Move the hoist lever forward to the DOWN
position and release. Releasing the lever
places the hoist control valve in the FLOAT
position, allowing the body to return to the
frame.
NOTE: If the dumped material builds up at the rear
of the body and the body cannot be lowered, then
perform steps c and d below:
c. Move the hoist lever back to the HOIST posi-
tion to fully raise the dump body. Then
release the hoist lever so it returns to the
HOLD position.
d. Shift the selector switch to forward, release
the brake lock, and depress the override but-
ton. Drive forward to clear the material. Stop,
shift the selector switch to NEUTRAL, and
apply the brake lock. Lower the body again.
NOTE: Failure to hoist the body, after making an
unsuccessful attempt at lowering the body, may
result in the dump body suddenly lowering after the
truck has pulled ahead of the material that was
previously preventing the body from lowering.
DO NOT move the truck with a
raised dump body raised
except in an emergency. Fail-
ure to lower the body before
moving the truck may cause damage to the hoist
cylinders, frame, and/or body hinge pins.
10. With the body returned to the frame, move the
selector switch to FORWARD, release the
brake lock, and exit the dump area carefully.
Summary of Contents for 730E
Page 2: ...Find manuals at https best manuals com ...
Page 8: ...A 4 Introduction A00044 KOMATSU MODEL 730E DUMP TRUCK Find manuals at https best manuals com ...
Page 10: ...A1 2 Index 8 10 A01001 NOTES Find manuals at https best manuals com ...
Page 48: ...A3 34 General Safety Operation A03048 NOTES ...
Page 51: ...This as a preview PDF file from best manuals com Download full PDF manual at best manuals com ...