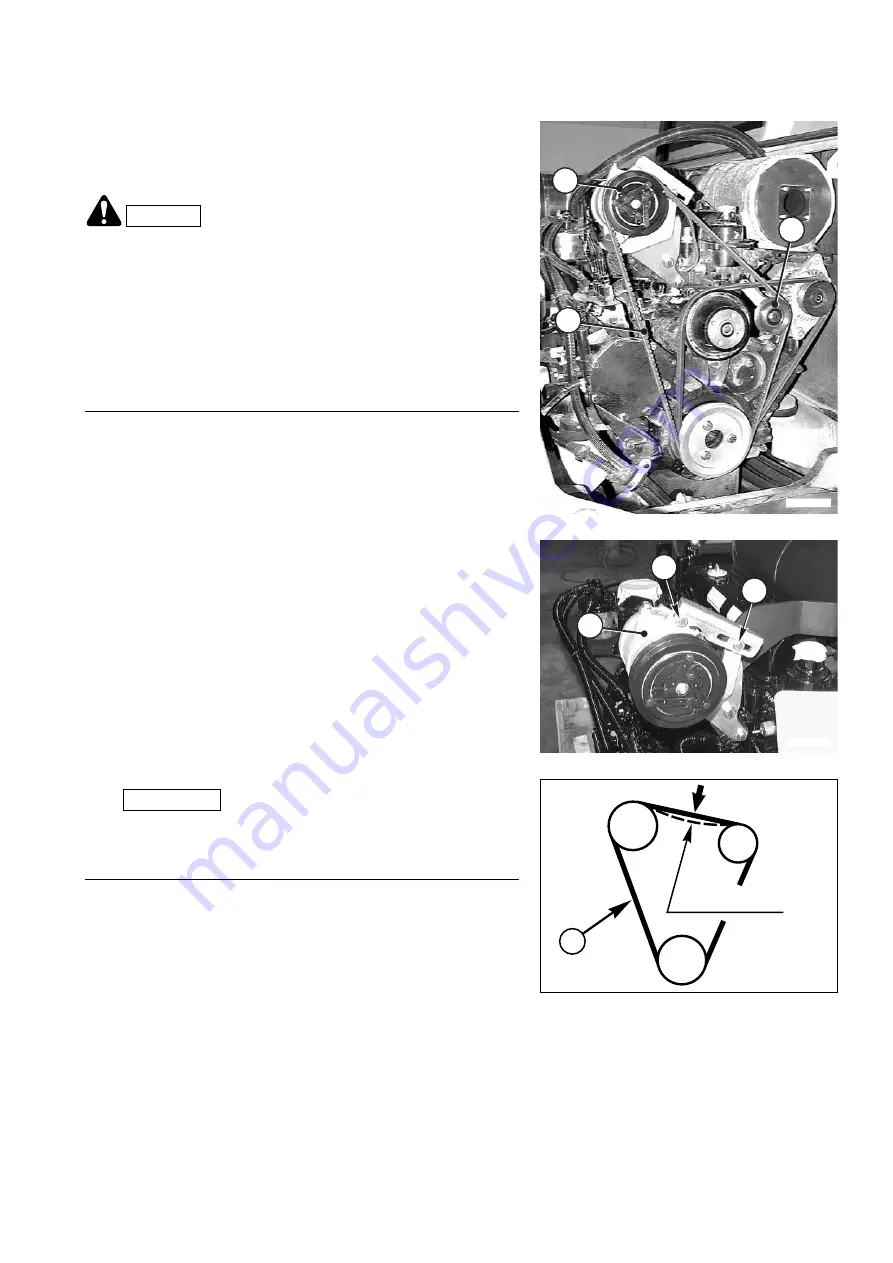
MAINTENANCE PLAN
165
4.7.9.b
ADJUSTING THE TENSION OF THE A/C
COMPRESSOR BELT (only for machines
equipped with air conditioner)
DANGER
•
The coolant contained in the air conditioning system is
very dangerous. If some sprays get into the eyes or come
in contact with the skin, they may cause blindness or con-
gelation. Furthermore, to avoid possible explosions, do not
cause sparks and do not use naked flames near the sys-
tem.
•
The adjustment of the belt tension is a mechanical opera-
tion and must be carried out without intervening on the air
conditioning system.
The compressor belt can be reached after opening the engine
hood (see “3.5.1. ENGINE HOOD”).
The check is manual and consists in pressing the belt (1) with the
thumb at the centre of the section between the compressor (2)
and the pulley (3).
With a pressure of 10 kg the resulting deflection must be approxi-
mately 7-10 mm.
When the belt is new the deflection must be approximately 4-6
mm.
If the deflection exceeds the values indicated, loosen the screws
(4) that fasten the compressor (2) and make the compressor slide
by using a lever that must be inserted between the casing and the
support.
Fix the screws (4) and check again.
Use a 13 mm spanner.
A -Compressor pulley
B -Idle pulley
C -Motor pulley
IMPORTANT
☞
•
If the belt is worn or in case of doubts on its conditions,
change it and check the tension again after a few hours of
operation.
RWAA12190
1
2
3
RWAA12200
4
4
2
RYA14470
7 - 10 mm
B
A
C
10 kg
1
Summary of Contents for PC110R-1
Page 2: ......
Page 19: ...17 SAFETY AND ACCIDENT PREVENTION...
Page 51: ...49 THE MACHINE AND ITS OPERATIONS...
Page 126: ...124 PAGE INTENTIONALLY LEFT BLANK...
Page 127: ...125 MAINTENANCE...
Page 190: ...188 PAGE INTENTIONALLY LEFT BLANK...
Page 191: ...189 TECHNICAL SPECIFICATIONS...
Page 198: ...196 PAGE INTENTIONALLY LEFT BLANK...
Page 199: ...197 AUTHORISED OPTIONAL EQUIPMENT...