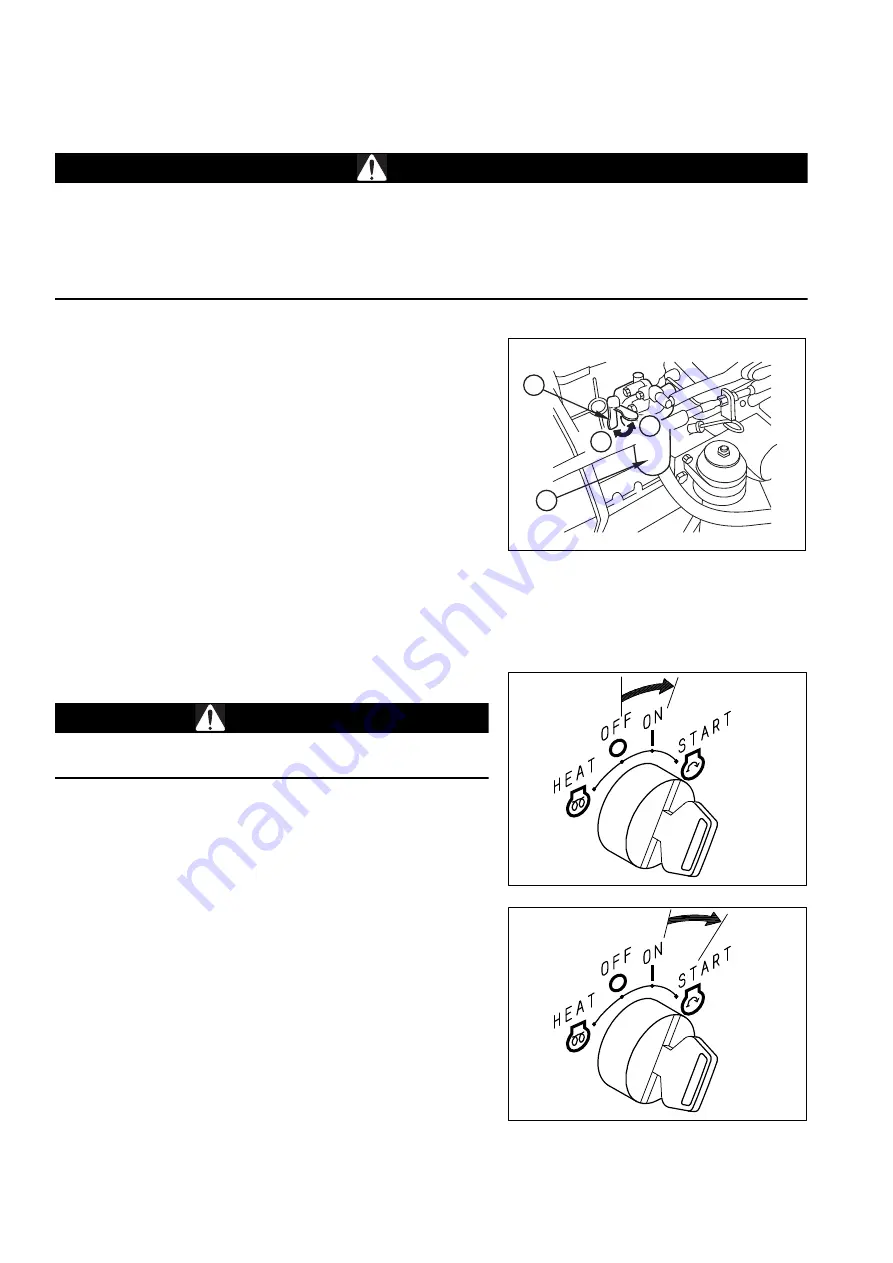
MAINTENANCE PROCEDURES
230
4.9.6.b
CHANGING THE FUEL FILTER CARTRIDGE
WARNING
q
Change the filtering element after work, when the engine has cooled down to 40–45°C.
q
During these operations some fuel may be spilled; clean the dirty areas immediately, in order to prevent
any risk of slipping or fire.
q
Oils, filters, the coolant and the battery are considered special waste and must be collected and dis-
posed of according to the regulations in force.
FUEL FILTER
1.
Open the engine hood.
(For details, see "3.2.6 ENGINE HOOD").
2. Turn the valve (1) of the filter to the closed position (A).
3. Using a filter wrench, loosen the metal ring of the filter and
remove the casing (2).
4. Clean the head of the filter holder and the inside of the cas-
ing, install a new filter and fill the casing with fuel.
5.
Lubricate the casing seal, install it on the filter holder and
tighten the metal ring until it touches the seal.
6.
Give the metal ring a further 2/3 turn.
IMPORTANT
• If the casing is tightened excessively, the seal may be dam-
aged and cause fuel leakages. Fuel leakages may also be
due to insufficient tightening. Therefore, it is advisable to
fix the casing by tightening the metal ring correctly.
BLEEDING THE FUEL CIRCUIT
WARNING
q
The engine may start during the bleeding operations; make
sure that there is no one near the machine.
1.
After filling the fuel tank, make sure that the valve (1) of the
filter is in open position (B).
3.
Turn the ignition key to position ON and wait approximately
15-20 seconds, in such a way as to allow the fuel system to
be automatically bled.
3.
Turn the ignition key to position START and start the engine.
IMPORTANT
q
If the engine starts regularly and then stops or functions ir-
regularly, check if there is air in the circuit; in this case,
check the tightness of the fuel filter and of the fuel pump
prefilter.
q
When all the fuel in the tank has run out, bleed the circuit
by proceeding as described above and repeat the opera-
tion at least twice.
RKA14340
A
1
2
B
RYA17290
RYA17360
WEAM012405
Summary of Contents for PC16R-3
Page 2: ......
Page 24: ...22 THIS PAGE WAS INTENTIONALLY LEFT EMPTY WEAM012405...
Page 25: ...SAFETY AND ACCIDENT PREVENTION 23 WEAM012405...
Page 79: ...THE MACHINE AND ITS OPERATIONS 77 WEAM012405...
Page 190: ...188 THIS PAGE WAS INTENTIONALLY LEFT EMPTY WEAM012405...
Page 191: ...MAINTENANCE 189 WEAM012405...
Page 244: ...242 THIS PAGE WAS INTENTIONALLY LEFT EMPTY WEAM012405...
Page 245: ...TECHNICAL SPECIFICATIONS 243 WEAM012405...
Page 253: ...AUTHORISED OPTIONAL EQUIPMENT 251 WEAM012405...
Page 286: ...284 WEAM012405...
Page 287: ......
Page 288: ...2017 KOMATSU ITALIA MANUFACTURING S p A All Rights Reserved Printed in Europe 02 2017...