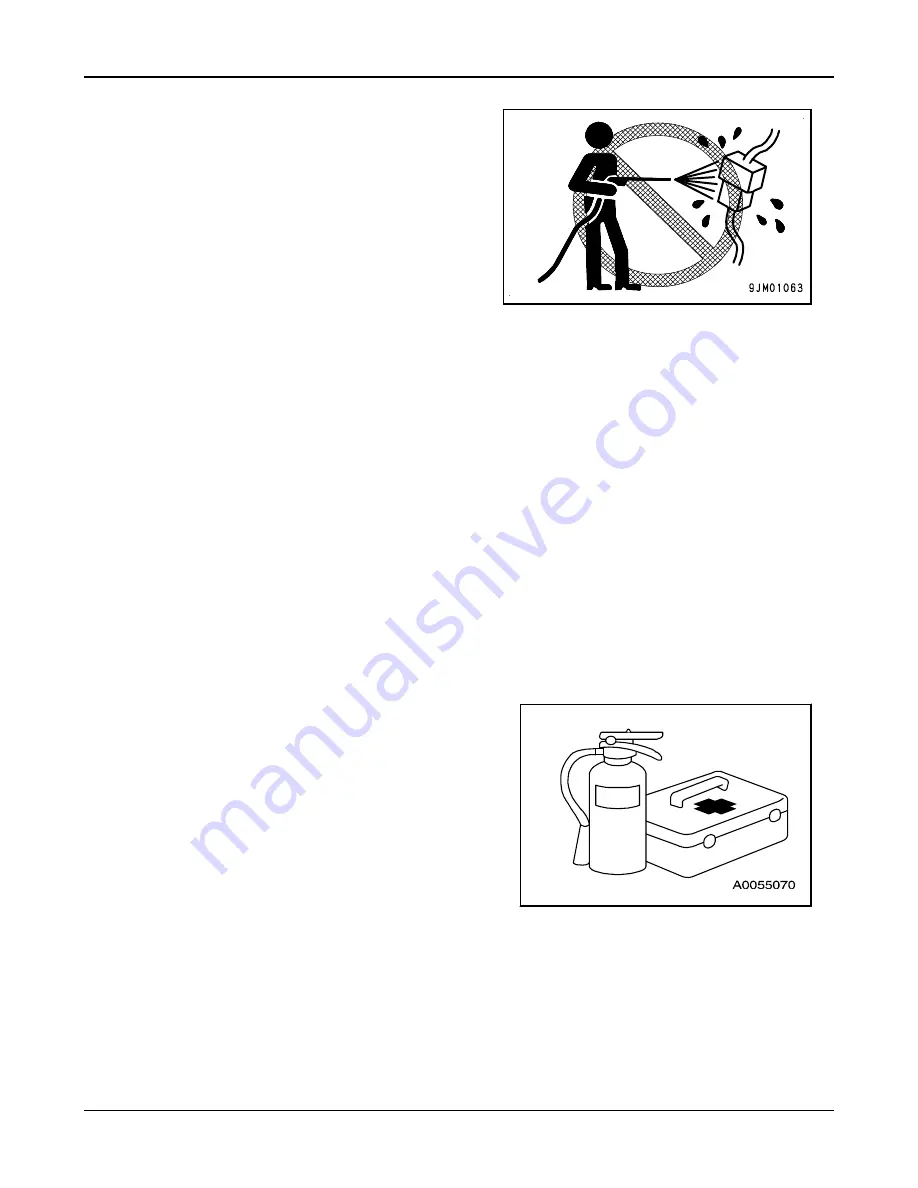
Keep Machine Clean
• If you get on or off the machine, or carry out inspection
and maintenance when the machine is dirty with mud or
oil, you can slip and fall. Wipe off any mud or oil from
the machine. Always keep the machine clean.
• If water gets into the electrical system, there is a hazard
that it will cause malfunctions or misoperation. If there is
misoperation, there is danger the machine may move
unexpectedly or cause serious personal injury or death.
When washing the machine with water or steam, do not
allow the water or steam to come into direct contact
with electrical components.
• When washing the machine with high-pressure water,
do not directly spray the camera as it may cause malfunctions in the camera. Clean the camera by wiping
off any dirt on the lens with a soft, dry cloth.
• When cleaning the camera, if you stand on something unstable or are positioned in an unstable posture,
you may fall and be injured. Use the proper stepladder or step on level and firm ground, then clean the
camera in a secure posture.
Inside Operator's Compartment
• When entering the operator's compartment, remove all the mud and oil from the soles of your shoes. If you
operate the pedal with mud or oil affixed to your shoes, your foot may slip which may cause a serious
accident.
• Do not leave tools or machine parts lying around inside the operator's compartment. If tools or parts get
into the control devices, it may obstruct operation and cause the machine to move unexpectedly, resulting
in serious injury or death.
• Do not stick suction pads to the window glass. Suction pads act as a lens and may cause a fire.
• Do not use a cell phone when driving or operating the machine. This may lead to mistakes in operation,
which could cause serious personal injury or death.
• Never bring any dangerous objects, including flammable or explosive items, into the operator's
compartment.
Provide Fire Extinguisher and First Aid Kit
• Be sure that fire extinguishers have been provided and
you have read the labels to ensure that you know how to
use them in emergencies.
• Carry out periodic inspection and maintenance to ensure
that the fire extinguisher is fully charged, located in the
correct place on the machine, and can always be used.
• Provide a first aid kit in the storage area. Carry out
periodic checks of the contents in the first aid kit and add
to them if necessary.
If Any Problems Are Found
If you find any problems in or on the machine during operation or maintenance (noise, vibration, smell,
incorrect gauges, smoke, oil leakage etc., or any abnormal display on the warning devices or monitor), report
it to the person in charge and make sure the necessary actions are taken. Do not operate the machine until
the problem has been corrected.
FIRE AND EXPLOSION PREVENTION
Be aware of the necessary actions to take in event of a fire, and know the precaution to prevent fires.
GENERAL PRECAUTIONS COMMON TO
OPERATION AND MAINTENANCE
SAFETY
2-14
PC240LC-10